Proposal for Aircraft Service Life Extensions Part 5: Considerations and Conclusions
The extension of aircraft lifespan is a significant issue in the aviation industry, and it must be approached with the utmost care.
Programs intended to increase the operational longevity of an aircraft should emphasize the improvement of surface protection, in addition to control, inspection and maintenance while it remains in active service.
For the research explored in this series, analysis of results would be the next step, which involves evaluating outcomes from both NDT and experimental testing.
Since many variables are associated, it’s important to thoroughly examine and assess all components and assemblies after testing. For example, if we find no damage during the initial inspection of test results, we may infer that faults in the structure could have resulted from fatigue or exceeding the limits of flight loads.
Alternatively, NDT tests may indicate the presence of only a few localized areas of surface corrosion on the primary structural elements. Based on NDT tests conducted on aircraft structures that have been operational for over 20 years, we could determine that there is no damage to critical aircraft structural components attributable to service loads, corrosion or other similar factors. This finding would provide a foundation for extending the operational lifespan of the aircraft structures.
Important Considerations for Life Extension
When proposing the implementation of a service life extension for an aircraft, there are a few crucial considerations to ensure a safe approach. For example, it is recommended that extensions be granted in phases of three to six months, in conjunction with major periodic inspections.
It’s also essential to take into account the modification status of the aircraft. An aircraft that has been entirely modified and has met the required compliance deadlines for modifications should be allowed extensions more leniently than aircraft that have not been modified in many years, provided that all other conditions are satisfied.
This means that a life extension inspection criterion would have to be developed for each aircraft by its respective operator. Aircraft manufacturers can aid this as well by creating safe life extension criteria and establishing a maximum value beyond which extension might not be safe.
Recommendations for Developing Service Life Extension Policies
Although an aircraft structure’s aging is inevitable, the process can be slowed by a variety of strategies, including:
- Finding critical points in the aircraft’s structure based on calculation stress and strength studies
- Identifying regions where aging's effects might have a significantly negative impact
- Maintaining visual oversight and analysis of the aging process of the oldest operating aircraft
- Analyzing the formal maintenance practices for the aircraft related to aging
- Improving protective maintenance methods to address and prevent aging early on
While using these procedures to protect an aircraft’s structure from aging is typically effective, it’s still crucial to assess fatigue levels before finalizing a life extension program.
Adopting the measures outlined below would contribute to an accurate assessment of the cumulative fatigue levels of each aircraft, ensuring that any extensions granted are safe:
Components and Recording
For each operator, it is essential to identify the critical areas of an aircraft most susceptible to damage. This differs among users due to the varied interactions between humans, machines and environmental factors. It’s advisable to communicate with the manufacturer to obtain a realistic evaluation.
It’s crucial for every aircraft to be equipped with a G-Meter as well. This device must be installed with a predetermined threshold value, beyond which the stress levels should be assessed following each mission. The record of “G” would help determine the stresses the aircraft has encountered during its service life.
The aircraft manufacturer is also responsible for installing stress-coated panels in critical areas. Conducting post-flight inspections of these panels would make it easier to identify whether the aircraft experienced excessive stress throughout its flight envelope.
In combination, the vibration log and the Helmut Chadwick vibration measurement and fault isolation system offer a reliable way to record vibration levels. This can be used in one of two ways.
For the first option, a threshold value for vibration levels can be defined for different modes, and only those values that exceed this threshold should be recorded. This methodology can aid in deriving a multiplying factor for the estimation of fatigue stress within the aircraft structure.
Alternatively, a vibration log can be maintained on a computer as a record of vibration levels, and this can be viewed to determine stress due to vibrations on each aircraft. However, the direct implementation of this strategy alone would not offer a clear criterion for life extension. A reference aircraft within the fleet can be utilized to derive a baseline, which teams can then compare with the bottom line and vibration logs of other aircraft.
Operational Conditions and Usage History
The history of an individual aircraft is a highly crucial factor. Accurate and up-to-date records of operating hours, inspections, occurrences and especially hard landings should be kept to ensure proper testing and analysis.
To aid this, manufacturers ought to establish service life limits for various global regions based on the specific environmental conditions, as is done in Russia.
An extension of the time between overhauls (TBO) or the service life limit would then benefit users by reducing life cycle costs and enhancing fleet availability over an extended period. Additionally, manufacturers could benefit by being able to establish longer structural life limits and offer spare parts, which allows them to support their customers for an extended duration.
Conclusions Regarding the Piper PA-44-180 SEMINOLE
The wing, wing carry-through and their attaching structure on Piper SEMINOLE aircraft are crafted with high-quality fabrication, constructive material, surface treatment and protection. This makes the aircraft the ideal subject for researching the possibility of life limit extensions.
Following the evaluation of NDT results after inspecting all the provided aircraft, it may be concluded that no unacceptable defects were found in any of the critical structural components of the airplanes. These findings would indicate a strong compliance with the relevant standards, confirming that the results align with the necessary criteria for continued safe operation of the aircraft beyond its original service life limit.
After the discussed NDT testing and other fatigue testing recommended for SEMINOLE vital airframe parts, we’ll hopefully be able to conclude that the service life of the inspected SEMINOLE aircraft structures can be extended. The ideas for additional revised maintenance and inspection programs and reduced crucial limitations in this series have been recommended to enable a formal certification of the aircraft for the extended period.
NDT methods play a main role in my research involved in the controlling and inspection of the wing, wing carry-through and their attaching structure. Should a life limit extension program be implemented, they must be conducted regularly and at the appropriate times in the aircraft’s life to ensure safety even after a potential extension is granted.
Should it pass all the checks listed above, I would recommend extending the service life limit of the Piper PA-44-180 SEMINOLE aircraft’s wing, wing carry-through and their attaching structure to 25,000 flying hours and consider the calendar life limit to be 30 years, adhering to whichever comes first.
To review previous installments in this series, see the related articles below.
Related:
- Proposal for Aircraft Service Life Extensions Part 1: Why Extend Life Limit?
- Proposal for Aircraft Service Life Extensions Part 2: What Influences Aircraft Aging?
- Proposal for Aircraft Service Life Extensions Part 3: What To Know About Service Life Limits
- Proposal for Aircraft Service Life Extensions Part 4: NDT and Experimental Testing Methods
About the Author
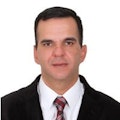