Proposal for Aircraft Service Life Extensions Part 3: What To Know About Service Life Limits
The calendar life limits established by aircraft manufacturers are the service life limit and Time Between Overhaul (TBO). To illustrate the differences in limits across manufacturers, this example will focus on the variations in the SA-330 Puma, Bell 412 and MI-8 helicopters.
Puma Helicopter, manufactured by Eurocopter of France, does not set a service life limit for the SA-330. This means the helicopter can be kept in service for as long as its operational condition permits, subject to its overhauls at laid down intervals.
The MI-8 Helicopter is manufactured in Russia and has specific recommendations for the total service life limit. The manufacturers give these helicopters 25 years of operation in a temperate climate and 20 years in a tropical climate.
The Bell 412 helicopter is manufactured by Bell Helicopter Textron, based in the USA. The manufacturer of this helicopter does not impose any limits on their structures for overhaul or retirement.
The American approach by Bell Helicopter Textron allows for establishing the structural life of different aircraft at the time that’s ideal for each one. For instance, a Bell 412 helicopter operating in a coastal region might be deemed Beyond Economical Repair (BER) after 11 years of operation, while another in a more temperate climate might fly for 20 years without displaying any signs of structural deterioration.
However, even without specified limits, it’s necessary for owners and operators to evaluate an aircraft’s physical condition regularly to ensure it remains airworthy. This includes completing routine inspections, performing an overhaul when necessary and retiring the aircraft when it reaches a clear end to its structural life.
Elements Affecting Structure Life of SEMINOLE Aircraft Wing, Wing Carry-Through, and Their Attaching Structure
Numerous variables can impact the physical state of an aircraft's wing, wing carry-through, and their attaching structure and other components, which sometimes shortens their service life. These include:
Temperature
An aircraft's structure is impacted by temperature in a variety of ways. Since aircraft can perform differently when navigating temperature ranges and fluctuations, manufacturers often specify the acceptable temperature ranges in which a particular aircraft should operate.
Every aircraft is subject to temperature changes, whether in the air or on the ground. Minor variations in temperature that are within maximum and minimum limits generally improve the endurance limit of the materials.
However, more significant variations in temperature, even occurring for short durations, reduce an aircraft’s endurance limit due to the cyclic strain. This may become severe when the structures are frequently exposed to drastically different temperatures. For example, when aircraft operate in hot temperatures, this mobilizes dislocations and reduces fatigue resistance and strength, thereby causing an overall reduction in endurance limit.
Temperature changes and their effects also become more complex within the aircraft's flying envelope. At higher altitudes, a chill factor occurs across the aircraft skin due to the lower temperature. At the same time, skin friction drag causes the aircraft's surface temperature to rise. The skin of an airplane is therefore subject to multidimensional cyclic temperature changes.
Corrosion
When operating in corrosive environments, the fatigue resistance of an aircraft is reduced. This happens when corrosive substance pits and roughens its surfaces. Because corrosion and operational stress happen at the same time, it is often difficult to assess how corrosion alone affects an aircraft’s structure. The following aspects must be taken into account when assessing the impact of corrosion:
- Frequency of Cyclic Stress: Cyclic stress becomes even more important when an aircraft is operating in a corrosive environment. The general rule is that the slower the frequency and higher the temperature, the higher the crack propagation and shorter the life at a stress level.
- Humidity and Salt Laden Atmosphere: Corrosion is accelerated by high humidity and atmospheric salt content. This increases the likelihood of corrosion for airplanes flying near coastlines. Extra caution must be used during dealing with wings in order to prevent scratches.
- Fretting Corrosion: This is caused by the microscopic motions of tightly fitted parts and structures. The process is visible through discoloration and pitting. Undergoing hard landings or near hard landings consistently is a common cause of fretting corrosion.
- Industrial Waste Gas Emissions: Because these emissions contain nitrides and sulfides, they are harmful to the environment and to an aircraft’s structure. These toxic compounds combine with water and form acids, causing aircraft structures to corrode after prolonged exposure. Emission of industrial waste gases into an environment containing salt also accelerates the corrosion process. This is common in port environments or other areas near the sea.
- Dust and Sand: Long-term use of an aircraft in dusty or sandy weather accelerates wear and degradation of the aircraft's exterior and, sometimes, internal components. Sand and dust particles get into cracks and between the mating surfaces of structural elements, which increases fretting corrosion. This impact is more noticeable with cyclic expansion/contraction due to the large variation of temperature between day and night.
Pilot Ability and Reporting
Aside from environmental impacts, an aircraft’s structure life is often shortened by its operational conditions. One example of this is the ability of the aircraft’s pilot.
While all pilots must meet core competencies and minimum ability requirements, there can be great variation in ability between pilots, even when operating the same types of aircraft.
For example, pilots may vary in their ability to recognize or prevent hard landings, and some may not report this occurrence every time it happens, impacting the validity of the aircraft’s usage history. Additionally, some pilots are more skilled than others when flying in adverse or challenging weather conditions with high levels of turbulence.
When evaluating an aircraft’s structure, precise documentation of vibration levels is essential, as the aircraft should only be approved for operational flight once the vibrations have been reduced to acceptable thresholds. If not properly documented by the pilot, this data and conclusions about its structure life will be skewed.
Collisions with birds and the contact of aircraft wings with trees are also stimuli that can quickly worsen an aircraft’s condition. This means it’s essential for pilots to avoid these situations and to document them meticulously when they occur.
Quality of Aircraft Maintenance
Proper routine maintenance may reduce an aircraft's overall wear and tear during its lifetime, making it a key element in evaluating and extending structure life. Some strategies that help to minimize degradation of aircraft structures include:
- Promptly addressing issues following a hard landing to prevent the onset of fretting corrosion and ensure the timely repair of loose rivets in two neighboring structural components
- Alleviating the effects of corrosion by applying fresh paint to damaged areas, including small chips and scratches
- Ensuring that vibration levels remain within acceptable thresholds
- Keeping accurate documentation of aircraft occurrences, the follow-up measures implemented and the records of periodic inspections
Aircraft Down Time and Parking Conditions
While the aircraft structure experiences significant fatigue during flight, it is also important to note that the aging process of the structure is accelerated during extended periods of inactivity.
This is especially true for aircraft with unsatisfactory parking circumstances. Aircraft that are stored outside are more susceptible to environmental factors, require more maintenance and, as a result, have a shorter structural life.
Aircraft Modifications (Considering Material Fabrication Processes and Design)
If an aircraft’s structure life is affected by damage to a certain component or controlled degradation, it’s sometimes possible to modify the aircraft to increase its service life. The current criterion for aircraft modifications incorporates the following factors:
- Chemical composition of materials to get the required strength
- The machine's design, including its dimensions and shape
- Manufacturing processes
- Heat treatment procedures
- Characteristics of the surface finish
The most important factors in increasing the service life limit are the materials and manufacturing processes. However, this is addressed by establishing stringent airworthiness standards and regularly releasing modifications to eliminate flaws in designs, materials and methods of manufacture and designs.
Widely known and reputable aircraft manufacturers are typically guaranteed to ensure that research and development are properly managed. This is why it’s often easier to secure an extension for an airplane made by a popular manufacturer than one made under license or by more obscure or newer manufacturers. As Piper is a reputed aircraft manufacturer, the use of the Piper SEMINOLE aircraft is an ideal choice for my research and experimentation regarding life limit extensions.
In all cases, if all these factors have been thoroughly considered, the timely implementation of the manufacturer's instructions and modifications would make it easier to secure safe extensions of the aircraft life limitations.
In next week’s installment of this series, I’ll explain the testing methods planned for this project. This will include a discussion of NDT methods, as well as additional methods that would aid in determining the potential service life limit of a Piper PA-44-180 SEMINOLE’s wing, wing carry-through and their attaching structure.
Make sure to read the first two installments in this series:
- Proposal for Aircraft Service Life Extensions Part 1: Why Extend Life Limit?
- Proposal for Aircraft Service Life Extensions Part 2: What Influences Aircraft Aging?
If you're ready for the next installment and concluding article, you can find them here:
About the Author
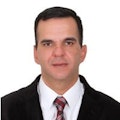