The Bright Side of Locating Reliable, Cost-Effective Aircraft Lighting Replacements
Exterior aircraft lighting may seem like a minor replacement part investment for airlines. However, the right selection of these components can provide airlines with a positive return on their investments by providing less downtime for aircraft for maintenance and greater reliability for the safety of aircraft and their occupants. While newly built aircraft today have built-in LEDs, most airline fleets continue to operate older planes that require halogen and xenon exterior lamps used for everything from the landing and taxi lights to wingtip navigation lights, logo lighting and more. These lamps can’t always be replaced with LEDs because of the high cost or because no drop-in replacements are available, making it important for airlines to choose lighting part replacements that deliver the same quality and reliability as the original lights that were once installed on the aircraft.
The selection of replacement halogen and xenon lamps is made easy with parts that have received FAA Parts Manufacturer Approval (PMA) or that are purchased through an OEM’s Illustrated Parts Catalog (IPC). Both of these options ensure that the lighting products are designed, tested and built to meet the exact specifications required by OEMs.
Breaking down the IPC and PMA
Both the IPC-approved and PMA provide airlines with options for lighting products that can be trusted to deliver quality just as well as the original lights from when the aircraft were first assembled. Choosing an OEM’s IPC (ex. Boeing IPC) means that a third-party lighting product manufacturer has received approval from the aircraft OEM to produce the part. While IPC products are a simple way to ensure the selection of the correct parts, they are not always the most cost-effective.
As airlines are often looking to find the lowest cost parts they can obtain, PMA parts provide operators with an alternative choice that is supported by the FAA. These lamps are often less expensive than their IPC counterparts while still providing the same dependability and long-life.
Manufacturers of FAA PMA products design and engineer their parts to meet strict specifications. While the aircraft manufacturer does not have to approve the parts, unlike the IPC, the lamp product manufacturer does have to submit a packet of documentation to the FAA to show how the part was designed to the required specifications and tested. This packet includes a drawing, all the testing documents, and proof that the parts manufacturer is meeting all the requirements that were initially set by the original aircraft manufacturer. FAA PMA parts are also regularly tested and monitored.
Additionally, airlines ordering FAA PMA parts can always be sure of the high standard of product they’re receiving. Quality control with FAA PMA products is done through statistical process control (SPC) testing where a certain percentage of each new batch of products is required to be tested thoroughly. PMA parts are also noteworthy because they may be designed through proprietary processes that could yield better durability, higher quality and longer lamp life. An example of one of these processes is if a manufacturer uses a specialized filament setting process.
Design and Testing to Meet Stringent Requirements
Aviation lighting manufacturers use American National Standards Institute (ANSI) standards along with other specifications to design, build and test lamps. Before a product can receive an FAA PMA or IPC designation, it must be put through a battery of tests, including tests of the voltage-wattage, tests of vibration characteristics and light output (photometric testing). The purpose of this photometric testing is to ensure the light output is equal to what was originally approved for the aircraft. This also ensures, for instance, that there is enough light output for pilots to see when using a taxiway at night. This test is performed in a dark room at a specific wattage. PMA or IPC parts must be rated to specific candela measurements (a unit of measurement for the intensity of light). Lighting products that are not PMA or IPC are often made cheaper and have lower candela ratings. Tests of the vibration characteristics makes certain the product’s filament remains durable when lit, without deformation or sagging.
Consideration of all the components of an aircraft is critical for safety, including the lighting parts that provide visibility to pilots, and make aircraft visible to ATC or other aircraft. When airlines choose quality lighting parts that are FAA PMA or IPC, they ensure they are putting the safety of their crews and passengers first while also acquiring products that reduce costs by lasting longer, hence requiring less downtime for changing them out.
John Fogel, Product Manager at Amglo, has worked with the company for more than 15 years in product development, qualifying products with the FAA and building partnerships.
For more information, visit www.amglo.com
About the Author
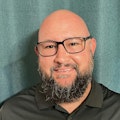
John Fogel
Halogen Product Manager
John Fogel, Product Manager at Amglo, has worked with the company for more than 15 years in product development, qualifying products with the FAA and building partnerships. For more information, visit www.amglo.com.