LED Industrial Lighting Enhances Safety & Operational Efficiency for Aviation Facilities
Safety and efficiency are two of the aviation industry’s biggest priorities and balancing the two is sometimes a difficult challenge. Critical safety features and protocols can be quite expensive and time-consuming, but they’re absolutely necessary to protect the traveling public.
At the same time, protecting the safety and wellbeing of personnel on the ground is paramount as well. From maintenance crews, mechanics and new aircraft construction teams to logistics specialists and other ground crews, there might be hundreds of people involved in building and maintaining an aircraft. Ensuring a safe and efficient work environment here also requires leveraging the latest technology at the most economical cost.
Upgrading to modern, high-efficiency industrial LED lighting in aviation facilities like airplane hangars is proving to be one of the best investments in safety and operational efficiency for aviation companies around the world. Originally intended for the rigors of heavy industrial applications, industrial LEDs are extremely well suited for aviation hangars due to their outstanding durability, long-life performance and high output that’s ideal for higher mounting heights.
The bright, crisp and ample light output are obvious benefits of upgrading from conventional technology, such as metal halide or fluorescents, to industrial LED fixtures. But, there are also a number of other advantages that make LED fixtures the clear choice for aviation, where precision, safety, attention to detail and operational efficiency are critical to business success.
Here’s how industrial LED technology outperforms most conventional lighting solutions in aviation applications:
Better Visibility Improves Safety
Poor lighting has proven to be a leading cause of slip, trip and fall accidents, along with contact with objects and equipment—some of the most common workplace incidents.
Clear visibility is critical in aviation construction and maintenance facilities where components and parts are often lying around during the build process or teardown/rebuild work. Improving visibility through better lighting has shown to reduce the risk of accidents by as much as 60 percent, simply because workers are better able to see what they’re doing.
At the Duncan Aviation facility in Michigan, with just 45-50 footcandles on the ground from their antiquated metal halides, technicians were forced to work with headlamps to see their work clearly and safely. An upgrade to high-output industrial LED high bay lighting solved that problem and workers now enjoy a much safer work environment.
“It’s absolutely amazing, like a night and day difference,” says Ryan Herbstreith, facility services manager at Duncan. “The guys love it, and they want to know when we’re going to replace the lights in Hangar 3, and all the other hangars.”
At the Anglo-Normandy Aero Engineering hangar in the UK, the company upgraded its antiquated 400W metal halides to 250W LED high bays and saw lux levels nearly triple, from 140 to 400 at work level.
“The quality of light exceeds my expectations,” said projects and facilities manager Chris Roussel. He also notes the improved visibility creates a better working environment for staff.
Color accuracy Improves Visual Acuity
Color rendering, measured on the Color Rendering Index (CRI), can also be a significant safety concern in aviation facilities. The CRI of metal halide fixtures is around 65-70 on a scale of 100, where 100 is equivalent to natural daylight. This unnatural orange glow makes it extremely difficult to distinguish colors.
For electricians who rely on the color-coding of wiring to work accurately and safely, the inability to distinguish a blue wire from a red one could result in a very serious injury, or worse. It’s also a problem for color-matching paint and other aesthetic or quality assurance work.
Industrial LED technology produces a crisp, bright light that mimics natural daylight at 80+ CRI, depending on the manufacturer, model and desired color. This makes colors appear naturally and easier to distinguish, allowing workers to clearly differentiate wiring, warning placards and fluids.
LED Eliminates Toxic Materials
Conventional lighting contains toxic chemicals that can put exposed individuals at serious risk. A single metal halide fixture contains enough mercury to poison an entire classroom full of children. A single broken bulb could affect dozens of workers with immediate symptoms, and for maintenance crews, long-term exposure can cause chronic illness. Fluorescents and other fixtures can also contain mercury, phosphorous and other rare earth minerals that are harmful when inhaled.
Industrial LED fixtures contain no hazardous materials, which means zero risk of exposure for workers. It also means aviation facilities can eliminate the cost of hazardous material disposal and achieve sustainability goals to operate with minimal environmental impact.
Maximum Efficiency Minimizes Costs
In addition to making for a safer, more vibrant work environment, LED lighting technology can also substantially reduce operating costs and improve overall facility efficiency.
Aside from being the most energy efficient lighting solution on the market—Anglo-Normandy saw its power draw drop from 3.37W/square meter to 3.96W and Duncan cut its energy use by 44 percent per fixture—they’re also virtually maintenance free. With some fixture models now carrying a 10-year warranty, aviation companies can dramatically reduce their maintenance costs, directing those resources into more useful, strategic efforts besides changing lightbulbs.
For even greater efficiency, LEDs are the only industrial lighting source that’s fully compatible with the use of occupancy sensors, dimmers, timers and other smart controls. This allows facilities to reduce fixture burn time by actually turning off the lights when not in use. At Duncan Aviation’s aircraft paint facility, the company used a 1-10V dimming cable wired into the lighting control at the panel box, married to a Rockwell PLC located outside the Class I Div 1 environment. This allows the lights to be dimmed as much as desired when they’re not needed, saving both electricity and money. That’s not possible with conventional fixtures like metal halides, which can take up to 20 minutes to warm up, forcing facilities to leave them burning 16/7 or 24/7, wasting energy and money.
Superior Technology, Outstanding Facility Performance
Industrial LED technology is an outstanding choice for maximizing aviation business performance. LED fixtures are well-suited for high mounting heights and effectively lighting large, voluminous spaces with pleasing, natural light. They’re also a sustainable and energy-efficient choice which contributes significantly to personnel safety with superior visibility that reduces the risk of accidents and injury.
And, with a combined energy, maintenance and operational cost savings, facilities like Duncan Aviation can see a payback on their investment in LED lighting in as little as four years, for savings that go straight to the bottom line for years to come.
Luis Ramirez is Dialight’s Chief Operations Officer and is responsible for global operations, including: direct and contract manufacturing; supply chain, planning and logistics; quality, warranty and technical services; and sustainability initiatives. He is a charismatic, “hands-on” and people-centric executive with over 23 years of global experience leading change in technology organizations with senior leadership roles in engineering, manufacturing, global operations and general management. Prior to Dialight, Luis served as Chief Operating Officer of MC Assembly, an electronics manufacturing services company. He also previously worked for Cooper’s Bussmann division, Laird Technologies, Thomas & Betts, and Eaton’s Cutler Hammer division. Luis holds an MBA from Washington University’s Olin School of Business; a Masters in Engineering Management from the Polytechnic University of Puerto Rico; and a Bachelor of Science in Industrial Engineering from the University of Puerto Rico.
About the Author
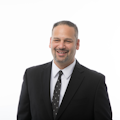