The FAA is responsible for the regulation and oversight of civil aviation within the U.S. Its primary mission is to ensure the safety of civil aviation.
As part of its mission, the FAA’s major responsibilities include:
Regulating civil aviation to promote safety
Encouraging and developing civil aeronautics, including new aviation technology
Developing and operating a system of air traffic control and navigation for both civil and military aircraft
Researching and developing the National Airspace System and civil aeronautics
Developing and carrying out programs to control aircraft noise and other environmental effects of civil aviation
Even with the FAA’s stated mission of encouraging and developing civil aeronautics, including new aviation technology, the rules governing FAA compliance – especially with respect to an aircraft’s maintenance history – are anything but new. Still guided by the insight and knowledge we had available to us when the agency was formed, the rules for aircraft maintenance records have gone from practical, to problematic, to borderline dysfunctional in the decades following.
According to Title 14 CFR Part 91.417, for a maintenance record to be a binding document in support of the airworthiness of the aircraft, it must contain the following:
A description of the work performed
The date of completion of the work performed, and
The signature and certificate number of the person approving the aircraft for return to service.
That seems clear enough. But it’s not. At least not when making a copy of this information. Most FAA inspectors and Flight Standards District Offices (FSDOs) in general have repeatably been advised by FAA legal that there is precedent in the U.S. court system that only original copies of CFR Part 43 documentation have been consistently accepted in a court of law. This, of course, has caused quite a bit of trepidation among both the FAA and industry.
So, what exactly is an original copy? When aviation regulation guidelines were established decades ago, a copy was obvious. Since there were no copy machines, no personal computers, no high-quality multi-color printers and no digital imagery, copies were only made by one method: copy paper. A copy was easily discernable because the copy was often discolored due to the copy ink of the paper, severely lacking in any kind of detail that would distinguish it as a bona fide original, and often smudged from handling the original and copy paper together.
But that world is now in the rearview mirror. Today’s world allows us to use any number of different means and/or software programs to create or modify and print a document.
This, of course, is the very essence of what the FAA and the business aviation community are struggling with. In an attempt to exercise some kind of control over this brave new world, the FAA issued Advisory Circular AC120-78 in 2003.
But it seems, AC120-78 has created as many problems as it has tried to solve. Advisory Circulars, like any forms of “guidance,” are not a set of rules that can be used to judge whether the operator is adhering to Title 14 or not. They are simply a set of guidelines to follow if your desire is to stay compliant with FAA recommendations. In other words, you can follow an Advisory Circular to the letter, but that doesn’t mean the local FAA FSDO needs to accept them as a way of your company operating its aircraft.
Herein lies the problem. Although an operator has elected to follow an Advisory Circular to the letter in order to make it easier for a local FDSO’s inspector to “accept” the procedure, it, unfortunately does not guarantee that every FSDO will accept this procedure as valid. Again, it is up to the FSDO’s discretion. This puts both the inspector at the local FSDO at risk of misinterpretation of the guidelines, and the operator at risk of having one FDSO accept this procedure, only to have another FSDO decide the procedure is “not acceptable” and invalid. This scenario could potentially place an operator in a “violation” position when they are using the procedure to perform business in different FAA jurisdictions, as airplanes usually do.
This conundrum has gotten our industry to a point of paralysis. But, clearly as an industry, we can do better than just throwing our hands up and accepting this as our destiny. In fact, we must do better! We now operate aircraft that fly faster, travel farther and operate more efficiently than ever before. The technology we use to accomplish this is state –of –the art. So why are we allowing the critically important maintenance history and airworthiness records of these amazing aircraft to be treated the same as we did over one-half century ago, despite the technological advancements that have made these methods practically obsolete?
We didn’t wait for the FAA to make a ruling allowing us to build pressurized aircraft, nor did we wait for weather radar or electronic flight instruments to become a rule before we incorporated these technologies in our aircraft. So why are we continuing to wait for the FAA to make a rule to allow us to use electronic recordkeeping and digital signatures?
So, where do we go from here? Here are a few suggestions of what we could, and should, as an industry, do to bring the 21st Century system of electronic recordkeeping into our daily operations:
Scan your existing paper records into electronic images in order to have both a back-up of the paper record, and to begin the important process of converting the world of aircraft recordkeeping from paper to electronic.
Begin an electronic recordkeeping system containing the same information that you are currently keeping in your paper system. Since a paper system is still the accepted “norm,” run both systems in parallel (the time and manpower it takes to do this will be more than made up by the efficiencies that the electronic recordkeeping system adds to your operation).
Start using a digital signature program to sign documents that do not require FAA approval to use. (Digital signature programs are readily available from several different sources you can find on the internet).
Write your congressman to insist that congress investigate passing new laws that will allow regulators to add language to Title 14 CFR that include electronic recordkeeping and digital signatures.
The first step is always the hardest and the most critical. As operators of the most sophisticated business aircraft in the world, we need to take this first step. Both the aircraft we operate, and the people operating these aircraft will benefit. But it’s imperative we act now!
Larry Hinebaugh is currently the executive director of a non-profit company called The Foundation for Business Aircraft Records Excellence. Hinebaugh was instrumental in creating this company after seeing so many aircraft operators inconvenienced, and aircraft owners financially harmed, by our industry’s poor logbook practices. A 40-year veteran of the business aviation Industry, Hinebaugh started his career as an A&P technician in a small jet maintenance shop in California and has since worked as a field service representative for Gulfstream Aerospace, director of maintenance for several corporations operating large business aircraft, and president of Aviation Consulting Group providing maintenance and completion representation to companies operating aircraft from Cessna’s to Boeing’s; before accepting his position with Business Aircraft Records (BAR).
About the Author
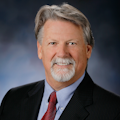
Larry Hinebaugh
Larry Hinebaugh is currently the executive director of a non-profit company called The Foundation for Business Aircraft Records Excellence. Hinebaugh was instrumental in creating this company after seeing so many aircraft operators inconvenienced, and aircraft owners financially harmed, by our industry’s poor logbook practices. A 40-year veteran of the business aviation Industry, Hinebaugh started his career as an A&P technician in a small jet maintenance shop in California and has since worked as a field service representative for Gulfstream Aerospace, director of maintenance for several corporations operating large business aircraft, and president of Aviation Consulting Group providing maintenance and completion representation to companies operating aircraft from Cessna’s to Boeing’s; before accepting his position with Business Aircraft Records (BAR).