Nondestructive testing (NDT) is the acquisition of information about conditions and defects in a material, part or structure without damaging it or rendering it unfit for service. NDT is one of the foundations of safety for the aerospace and aviation industries. In this feature, we have reached to Roger Engelbart, from the board of directors of the American Society for Nondestructive Testing, to assess how NDT has evolved in recent years, what the newest NDT technologies are, and how an aircraft maintenance, repair and overhaul (MRO) organization can become NDT certified.
Evolution of NDT
Engelbart observes that NDT is known by several different acronyms.
“They are often used interchangeably, and practitioners understand what is meant, but each has a specific meaning regarding how it is used,” he said.
Nondestructive testing (NDT), per se, is the testing of materials, production parts and assemblies at the appropriate stages of the manufacturing cycle, affirms Engelbart.
“Nondestructive inspection (NDI) is the inspection of the aircraft during its in-service lifetime. The inspection is performed by the customer/aircraft operator, but development and verification of the inspection procedure is done by the aircraft manufacturer,” he said. “Nondestructive evaluation (NDE) is the testing of materials and parts in research and development to acquire engineering information without being bound by specifications or acceptance criteria. Nondestructive characterization (NDC) is the determination of material properties, often in a research environment.”
NDT is employed in the aerospace industry beginning with the processing of raw materials and extending through the lifecycle of the aircraft, affirms Engelbart.
“NDT has evolved largely through improvements in digital technology. In the transition from analog to digital, instruments have become more compact, rugged and reliable. Advances in digital imaging and associated software have allowed improvements in the quality of the acquired data and the ability to extract more quantitative information,” he said. “For example, digital radiography has overtaken film radiography in many organizations; thereby eliminating the need for chemical processing and providing technicians with the ability to adjust and optimize image parameters without reshooting has resulted in significant cost savings.”
Newest NDT Technologies
According to Engelbart, in the aircraft and aerospace industries, it is vital to detect damage to materials and components at any point in their operational life.
“Radiography is one such way to do so. This technology is not new, but significant advancements have been made in recent years to improve the timeliness and quality of the finished product,” he said.
Digital radiography is an advanced form of x-ray technology where radiation is emitted from the source strikes a detector in place of the film, creating an electronic image sent directly to a computer, explains Engelbart.
“This can be adjusted for brightness, contrast and other parameters, eliminating the need for expensive and time-consuming re-shots. As an example of the use of this technology, ASTM International has developed standardized digital reference radiographs for aluminum and magnesium castings,” he said.
Computed radiography provides the advantage of electronic imaging but with a flexible phosphor imaging plate, highlights Engelbart.
“The plate is flexible and can be cut, bent and placed similar to film. The plate is placed inside a scanning unit where a laser picks up the image and stores it, then wipes the plate for reuse,” he said.
Considerable innovations have also been made in automated defect recognition, sometimes termed assisted defect recognition, according to Engelbart.
“Using neural network learning, software has been trained to make decisions on whether to accept or reject inspected materials or components. The program is not given authority to make final decisions but makes the evaluator aware of data or anomalies that can lead to a more informed decision,” he said.
NDT Certification for MROs
The certification of an aviation MRO facility involves a series of intensive audits of all phases of its NDT operations, points out Engelbart.
“There are numerous ISO documents and ASTM standards, guides, and recommended practices that may serve as guidelines to audits; an example of such a document is ASTM E543, Standard Specification for Agencies Performing Nondestructive Testing. This specification in turn references several other documents that cover a broad range of NDT methods and applications,” he said
Items that might be targeted in an audit of an NDT operation include the fitness of equipment, personnel, or a facility to perform each NDT method for which certification is desired, equipment calibration and traceability, and reference standard traceability, according to Engelbart. Personnel training and certification is also important, and specifically formal training, the process of documenting on-the-job training hours for method and applications, training oversight, and the process of advancing personnel through certification levels. Other audit areas include the process for developing, documenting, and approving NDT procedures, and record keeping and retention, he says.
Each potential customer of an MRO – be it an aircraft manufacturer, an engine manufacturer or aircraft operator – may have its own specific requirements and is entitled to perform its own audit on the NDT operations, emphasizes Engelbert.
“One approach to satisfying numerous customer requirements is to obtain the National Aerospace and Defense Contractors Accreditation Program (NADCAP) certification. This is a government-industry cooperative that has developed a standardized and rigorous audit process; becoming a certified supplier allows customers to select the MRO without the added expense of their own audit process,” he concluded.
About the Author
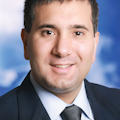
Mario Pierobon
Dr. Mario Pierobon provides solutions in the areas of documentation, training and consulting to organizations operating in safety-sensitive industries. He has conducted a doctoral research project investigating aircraft ground handling safety. He may be reached at [email protected].