The prevention and repair of airframe corrosion is an important maintenance activity with implications in terms of structural integrity and safety. In this feature, we reach out to industry experts to assess best practices for corrosion prevention and corrosion-related repairs, and we look at the impact of newer designs on corrosion prevention and repair.
Preventing Corrosion
According to Juan Vega, director of facilities at StandardAero’s Van Nuys facility, a constant cycle of cleaning, inspection, storage and lubrication must be followed to prevent corrosion. “In addition, having maintenance personnel well-trained on corrosion control programs and inspection techniques will improve corrosion prevention,” he said.
With regard to corrosion prevention, it is necessary to follow the original equipment manufacturer's (OEM's) corrosion prevention and control program. “Completing corrosion inspections regularly, filling out service bulletins that improve durability to corrosion, and regularly cleaning the aircraft from external pollutants help prevent corrosion,” said Ray Sharp, director of operations at the StandardAero plant in Springfield, Illinois.
Corrosion prevention involves treating the surface in a way that prevents the metal from starting to self-destruct and returning to its natural state, observes Jerel Bristol, president of SEAL Aviation.
“Sometimes corrosion begins within the metal, typically due to a manufacturing defect when the material was produced. Corrosion prevention typically begins with applying a chemical film to the metal, i.e., a good epoxy primer. Sometimes the metal is heat-treated to strengthen it but also to prevent corrosion,” he says. “When a corrosion preventative compound (CPC) is applied, there should be no corrosion present otherwise, if CPC is applied to the corrosion, corrosion will continue. CPC will also not allow visual inspection of the surface, but by the time one sees the corrosion covered by the CPC, the damage will be extreme.”
A valuable prevention tool is to perform a good visual and non-destructive testing (NDT) inspection, treat bare surfaces so as not to allow exposed metal to initiate corrosion, and have the exterior of the aircraft properly painted while subjecting the internal structure to proper treatment, according to Bristol.
“The best tool to prevent corrosion is visual inspections and NDT by experienced technicians. NDT is used to find corrosion where one typically cannot see visually. Rotor peening/shot peening are used to prevent corrosion. Peening the metal compresses the material which makes it more difficult for the environmental elements to start the corrosion process,” he said. “Depending on the location, the material to be inspected depends on the NDT inspection method. Each NDT method can be different, for example X-rays can see corrosion in layers of material, eddy current is used to find small pits and subsurface corrosion, and ultrasound can see material loss within a part. It would be good practice, near the ocean or in an area with high saltiness, to frequently rinse the aircraft with fresh water.”
Corrosion-Related Repairs
Once corrosion is found, it needs to be reported and documented to determine its allowable limits and applicable repair process, affirmed Vega.
It is necessary to follow the reporting process as outlined by the OEM manuals, explained Sharp. “This process will provide what next steps to take to remove the corrosion and what protections to apply or repairs required to restore the area back to a serviceable condition. Corrosion-related repairs are typically provided by the OEM structural repair manual or released by the structural engineering teams for that specific aircraft,” he says.
The allowable limits indicate the amount of corrosion that can be removed or cleaned, without compromising the structural integrity of the component, according to Vega.
“A component exhibiting corrosion within its ‘allowable limits’ is repaired by cleaning, disassembling, and removing the corroded area, subsequently inspected to confirm complete removal of the corrosion. Subsequently, protective surface films and protective coatings, primer and/or paint are applied,” he says. “If, on the other hand, the determined corrosion is beyond its ‘allowable limits’, it is necessary to carry out a structural repair. If a structural member, for example a floor beam, is found to have corrosion beyond its allowable limits, it must be repaired by removing or cutting the affected area or section and replacing it with the same material and additional reinforcement splice pieces of the same material are installed to bring it back to its original structural integrity.”
Typically, to remove corrosion, a surface conditioning disc grinder is used for medium to light surface corrosion, observes Bristol. “If, however, the corrosion is intense, it will be necessary to use more aggressive mechanical means such as rotary files and then smooth the surface according to the instruction manuals or technical order; in fact, leaving the surface not adequately smooth can result in the material being exposed to corrosion,” he says.
The correct way to check the smoothness is to use a smoothness gauge and typically the smoothness of aluminum is 65 μin, according to Bristol.
“The corrosion should first be removed, typically an NDT inspection is carried out to ensure all corrosion is removed. One needs to be familiar with the manuals to determine the location of the damage on the wing or component. Typically, an aircraft maintenance manual, component maintenance manual, or structural repair manual would give limitations,” he says. “It is not possible to measure a pit to determine how severe the corrosion is, as the pit could be the entry point to allow environmental elements into the metal, so the small pit turns into a channel within the metal, a corrosion cavern.”
Development of the Designs
Over the years aircraft OEMs have engineered and implemented the use of non-metallic material and corrosion-resistant metals to minimize corrosion damage, affirms Vega. “Carbon fiber is one of the materials that slowly taking over and replacing aluminum alloy components,” he says. With the implementation of new materials on newer aircraft is born the responsibility to train personnel to use proper tools to not affect the factory coatings so not to allow the corrosion to start, according to Bristol.
Today’s built aircraft are assembled using better developed materials which include identifying the removal of some products that were found to trap moisture and improving aircraft draining in key areas, highlights Sharp. “Aircraft inspection programs are continually being revised which may include adjusting frequency of corrosion inspections, release of improved corrosion inhibitors, and OEM’s sharing of recent discoveries using electronic media via released news flashes, advisories, or alerts,” he concludes.
About the Author
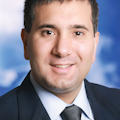
Mario Pierobon
Dr. Mario Pierobon provides solutions in the areas of documentation, training and consulting to organizations operating in safety-sensitive industries. He has conducted a doctoral research project investigating aircraft ground handling safety. He may be reached at [email protected].