Support for Line Maintenance
When aircraft is at the gate or parked elsewhere on the ramp waiting for daily inspections or tire changes, line maintenance can be a very challenging job in the most ideal weather. But add snow, ice and wind, and it becomes almost impossible.
The trucks and stores support vehicles that were previously used were just that – a pickup truck with no covered storage. Everything would just get tossed in the back, and off the crew would go.
But today, in 2019, with security gates and airside inspection booths, time is everything.
In Canada, for example, airports are constructing airside security inspection booths as per Transport Canada. This keeps us all safe, but the downside is the extra time it can take maintenance personnel to get to an aircraft. In fact, it can take up to 45 minutes just to get the Line Office on the ramp from a non-secured parking location.
Delays can cause a trickle-down effect if an aircraft is not ready. The ground handler must wait to tow the plane to the gate or delay loading. This, in turn, leads to baggage sitting at the gate in carts, possibly in bad weather, resulting in damage to the baggage. It slows down cargo processes and can cause back ups for other aircraft as well.
If a head start does not leave on time, every flight that aircraft is doing throughout the day is also delayed. The list is long, and in the end costs money as on-time performance (OTP) suffers.
So once a crew is on the ramp, using their time efficiently is key. Crews don’t want to travel back and forth to the hangar, so they limit those runs as much as possible.
This is why Wilcox Ground Services took an interest in creating custom design line maintenance vehicles and related equipment. Maintenance personnel are seeking solutions to help AME/AMTs work safely. As a result, their ideas have evolved regarding what a line maintenance truck or van should be.
Nothing can replace a great team, but excellent equipment sure helps. The interesting thing that the airline industry is slowly realizing is that GSE is a vital part of the equation when it comes to line maintenance.
When you supply quality equipment that meets maintenance requirements, the stress surrounding the work is reduced.
To assist with this, Wilcox Ground Services has put a new spin on numerous outdated truck designs. With the addition of platforms with fall restraints, sealed tool storage for chemicals and tools, storage boxes for ladders, nitrogen bottle holders, tire racks and lift gates as well as proper work lighting for night maintenance, crews have all the tools needed within reach to complete a variety of work.
This might sound normal or mundane, but everything has a reason. Something as straight-forward as a sealed storage box for a ladder is invaluable to an AME/AMT. The ladder stays out of the elements, keeping it clean and dry. If it’s snowing or freezing rain is falling and a ladder has been sitting in the back of a truck exposed to the elements, no one wants to risk injury by climbing it. So, the sealed storage box can significantly lower the chance of slipping just by protecting the equipment.
The other features have come from AME/AMT input as well, and additional designs are being developed to provide additional solutions.
Wilcox has also designed support units, such as supervisor trucks and stores trucks. These vehicles can allow a runner to assist with line maintenance. With tire racks and lift gates, they can supply tires along with sealed storage areas for oxygen bottles for crew and cabin. Supervisor trucks with lift gates and ample exterior lighting can also help in night time inspections and with tire changes, if needed. They come with two 360-degree remote-control inspection lights to look at the aircraft at night, as well as a 20-inch LED bar to light up a large area for tire changes.
When trucks are equipped with the necessary gear and lighting, support for AME/AMTs improves, which then leads to more efficient and more cost-effective labor. When selecting a maintenance vehicle, give consideration to specific needs for an operation, so it can be determined if tire/brake carts, lighting, generators or other features are required to make an operation run smoothly.
Having too many vehicles can cost both time and money. Driving four units to an aircraft to support one task takes several AME/AMTs away from what they were doing. But having a unit properly up-fitted allows work days to be scheduled efficiently and keeps crews better prepared.
We all know the right tool for the job is important. But choosing the right vehicle to bring the required tools to the job can be equally valuable.
Chris Jenny is product development manager of ground service equipment at Milton, Ontario-based Wilcox Ground Services. He has more than 10 years of GSE experience, having previously held positions at WestJet and Swissport in technical and advisory roles.
About the Author
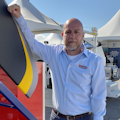
Chris Jenny
Chris Jenny is product development manager of ground service equipment at Milton, Ontario-based Wilcox Ground Services. He has more than 10 years of GSE experience, having previously held positions at WestJet and Swissport in technical and advisory roles.