Optimizing Ground Handling with Advanced Container and Dolly Tracking Solutions
Ground handlers have long been challenged by how best to track their containers, unit load devices (ULDs) and dollies. Specifically, they have had difficulty staying informed as to where a dolly is situated on the airport apron; its status; maintenance requirements; and how the total dolly fleet is being utilized.
Without being able to gain the real-time status of a dolly and know if it is empty or loaded, or which ULD is loaded, leaves ground handlers with little control over this equipment. Consequently, ground support equipment, manpower allocations and productivity, as well as related costs and profit margins, are also negatively affected.
To help address this problem, INFORM GmbH and Blumenbecker Technik GmbH joined forces, each lending their unique technical expertise and ingenuity. Together, they created the industry’s first solution for optimizing the management and maintenance of dolly fleets by providing real-time answers to the key questions of: Where is a dolly located? Is it empty or loaded? And where is the container/ULD?
Through the combined information regarding both the dolly and ULD locations, ground handlers can readily identify the location of every ULD on the apron. Additionally, they gain full control over the capacity utilization of each dolly thereby facilitating the more efficient use of their fleets and, when possible, the ability to reduce the number of dollies and associated costs.
Replacing Manual Processes
By merging telematics with data drawn from ground handling processes, the solution is able to eliminate the blind spots regarding equipment located on the apron.
Each company’s technology has a specific role. INFORM’s real-time allocation solution’s role is to manage an optimized allocation and assignment of ULDs and dollies to a specific loading or unloading task. Through the solution, a complete view of the process regarding a ULD’s warehouse position and its destination location is provided. Ground handlers can access, in real-time, all of this pertinent information about a specific ULD.
Where the Blumenbecker Technik technology comes in is on determining the dolly’s status. Specifically, its technology complements the INFORM solution by adding a next-generation tracking system that both tracks a dolly’s location, and also identifies whether or not a dolly’s status relating to whether it is loaded, intact or defective. Knowing this information is critical to achieving fast and efficient feeding of dollies to the loading process. This involves sensors on the dolly detecting how many containers are loaded on the dolly.
Several airports have beta-tested the solution which has proven to successfully determine dolly location and status without requiring direct transmission.
Here Comes the Sun
Another significant feature of the tracking module is its protective plate. In addition to providing a shield against damage from containers, luggage and inclement weather, this protective plate gets its energy from the sun.
The solar-powered module requires no routine battery replacements and is completely maintenance free, reducing labor and equipment costs, while supporting sustainability objectives.
The tracking module operates with the system transmitting data via an energy-saving low power wide area network (LPWAN) or through 4G Cat M1 (GSM). An added advantage is provided through its reduced data transmission and use of the more cost-effective Bluetooth low energy (BLE) tags for the majority of dollies.
Further, this network technology can operate even when direct transmission fails. It can reliably detect any location even if a dolly is located in a building.
Delivering Other Significant Benefits
Another advantage the combined INFORM and Blumenbecker technologies provide over manual processes is the quick determination of a dolly’s loaded/unloaded and defective/intact status which eliminates unnecessary “empty runs” or arduous searches.
When the tracking module is supplemented by a loading sensor, there is yet another benefit. The sensor detects containers on the cargo trailers and transmits the loading status on a continuous basis to the airport’s monitoring system. With a push of a button on the module, a fault message can be sent for prompt detection and management of defective equipment.
Precise data as to a ULD’s status (i.e., the time it was loaded in the warehouse; where the dolly and respective ULD are parked; and when the ULD is ready for pick-up) is made possible with the INFORM real-time allocation solution and Blumenbecker technology used in combination. This gives ground handlers complete control over both the dolly’s status and their ULDs.
At the moment a ULD is placed on a dolly, the system, drawing on the pick-up information conveyed by the INFORM software, knows which ULD was loaded. Thus, at any time, a full and accurate update can be accessed as to which ULD is loaded on which dolly and where their precise location is on the apron.
Maintenance processes are improved, too. The system’s tracking module or RFID uniquely identifies each dolly and object data based on its object number or maintenance history. Using this transmitted data, an operating profile can be generated for each dolly. The system can assess mileage and create load profiles enabling optimized maintenance schedules to be created rather than maintenance by a predetermined calendar date that does not take into account these factors.
By customizing the maintenance schedule accordingly, higher levels of safety and functionality can be achieved, as well as more cost-efficient allocation of resources.
Raising the Bar on Asset Optimization
There is also a clear benefit derived from these technologies in helping ground handlers reduce their dolly fleet sizes. By having accurate data as to their dollies’ status, ground handlers can get a better understanding of what percent of their fleet is typically empty, sitting in parked positions. This information can then be applied to initiate fleet reduction measures as warranted. Being able to also identify defective dollies and react to contingent needs for an empty dolly are other capabilities derived from these applied technologies.
Ground handlers have a high bar to meet with pressure coming at them from airlines and airports alike. Having the ability to streamline and optimize their processes to generate greater efficiencies and economies is imperative. When time-consuming and error-prone manual processes can be replaced by leading-edge technologies, ground handlers not only raise the bar on their operations, but also maximize their asset utilization and fiscal performance.
Alexander Wendorff is a solution manager at INFORM GmbH, where he has served for 25 years. His role in assisting the company’s aviation clients encompasses a wide range of skills from project management and process improvement to business strategy and logistics.
Ralf Herzog is managing director at Blumenbecker Technik GmbH since 2013. Before that, he held the position of international sales manager.
About the Author
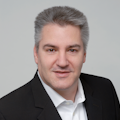
Alexander Wendorff
Alexander Wendorff is a Solution Manager at INFORM GmbH, where he has served for almost 24 years. His role in assisting the company’s aviation clients encompasses a wide range of skills from project management and process improvement to business strategy and logistics. He has been instrumental in numerous successful optimization software solution roll-outs.
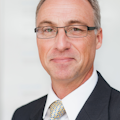
Ralf Herzog
Ralf Herzog is Managing Director at Blumenbecker Technik GmbH since 2013. Before that, he held the position of International Sales Manager.