HYPSTAIR: Most Powerful Hybrid Electric Powertrain Powers Up
The world around us is getting more and more electric. Electric-powered air travel was stuff from sci-fi movies just few years ago - now we are much closer to it as this is perceptible. On Feb. 9, 2016 first power-up of the world’s most powerful hybrid electric powertrain for aviation took place in Europe, in Slovenia, on board the hybrid-powered Pipistrel Panthera and as a part of the European HYPSTAIR project.
A major step toward electric-powered flight was achieved with the power-up of the hybrid electric powertrain in a project led by Slovenian aircraft manufacturer Pipistrel. The aircraft that was tied down to the ground, was missing the wings but for a first power-up this was enough, much easier and … safer. The Pipistrel Panthera, a modern four-seater aircraft – itself presented just two years ago - was chosen for this project because from the beginning it was designed for use not only with conventional piston engines but even for hybrid powerplants/systems. Pipistrel Panthera is a modern, sleek, four-seat aircraft designed to fit in the EASA CS23 regulations framework with an MTOW of 1,315 kg or approximately 2,900 pounds.
Hybrid-electric powertrains are the newest breed of propulsion in the aviation world. Similar to the development in the automotive world, here an internal combustion engine (ICE) extends the range of all-electric aircraft with a bonus of being environmental friendly and quiet. The 200-kw (268-hp) propulsor developed during the project HYPSTAIR and now installed in the Panthera, delivers the power equivalent to a typical general aviation piston engine and can run in three modes: only electric on batteries, generator-only, or hybrid mode combining both power sources. This means in simple words: 200-kw electric motor is spinning a propeller, 100-kw (134-hp) energy is either coming from the batteries or from ICE/generator or from both sources together. Possibly it's time to get used to the term “propulsor” as hybrid systems are coming to the market.
Pipistrel CEO, Ivo Boscarol, says: “We are proud of what HYPSTAIR represents for the development of electric flight. It demonstrates the possibility for general aviation class aircraft to be electrically powered and it confirms the vision of Pipistrel – we were the first to design a four seat aircraft, the Panthera, than can be alternatively equipped with three different propulsion types: piston engine, electric motor or hybrid powertrain. Project HYPSTAIR represents a major step in the direction of a hybrid aircraft and an opportunity for Pipistrel and other general aviation aircraft manufacturers.”
The Design
There are basically two possible hybrid architectures: the serial and parallel. In a parallel one - which is very similar to a “classic” combustion engine installation, there is only an addition of the electric motor which is closely coupled to the gas engine. HYPSTAIR is using the serial-hybrid solution where two independent energy sources are used (gasoline engine with generator and batteries) to drive the propeller. In this solution the propeller speed is not directly linked to the ICE (combustion engine) with resulting optimized propeller efficiency and lower noise in all electric flight phases. This solution allows new aircraft configurations, e.g. distributed propulsion; meaning that the electric motor can be mounted (far) away from the engine/generator/batteries location.
All electric powertrain components, developed by Siemens and used for the project represent the state of the art of electric flight propulsion at this moment. The complete system of HYPSTAIR serial-hybrid-drive consists of: 200-kw electric motor, high-power battery system, four inverters, 100-kw generator, and internal combustion engine (ICE) as range extender, Rotax 914 turbo engine.
The high-power battery system - developed by Pipistrel - consists of two identical packages, and will be located in the wings, in a protected area behind the main spars. Battery weight is according to Pipistrel's Igor Perkon, approximately 110 kg with 13 kwh of usable capacity. It is capable of 200-kw continuous discharge, is fitted with proprietary BMS (Battery Management System), and is air cooled.
In this feasibility study, an adapted Rotax 914 turbocharged engine was used as ICE on which the generator was attached.
The installed electric-drive motor – showcased last year at AERO in Germany - spins a specially designed, low rpm propeller delivering 200-kw take-off and 150-kw continuous power while the generator used for charging the batteries and driving the electric motor delivers 100 kw. This means a power density of more than 5 kw/kg. Unprecedented reliability is provided by use of dual windings of the electric-drive motor and by four power controllers/inverters.
In March 2015 Siemens presented a new type of electric motor that has been specially designed for use in aircraft and with a weight of just 50 kilograms (110 pounds). It delivers a continuous output of about 260 kilowatts – five times more than comparable drive systems. To achieve its record-setting power-to-weight ratio, Siemens' experts scrutinized all the components of previous motors and optimized them up to their technical limits. They achieved a unique weight-to-performance ratio of 5 kilowatts (kw) per kilogram (kg). The electric motors of comparable strength that are used in industrial applications deliver less than 1 kw per kg; the performance of the drive systems used in electric vehicles is about 2 kw per kg.
Frank Anton, head of eAircraft and the initiator of electric aircraft development at Siemens AG, says, “Siemens is developing electric drive systems with highest power-to-weight ratio for aircraft propulsion. Only with innovation can we solve the problems of rising fuel costs, rising passenger demand, and rising environmental regulation. Innovations developed for the HYPSTAIR hybrid-electric powertrain will be instrumental in making aviation more sustainable in the long run. As electric drives are scalable, we can expect, that in the future also larger aircraft will use electric propulsion. The world is becoming electric, whether in the air, on land, or at sea.”
Additional innovative element of HYPSTAIR is the human-machine-interface (HMI) designed to simplify the operation of a complex powertrain. This elements, designed and realized by the Italian mbvision, consist of a single “power lever” and a new integrated cockpit display to monitor the powertrain status and performance. The single power lever is an interesting solution that was displayed during the E² symposium in Stuttgart, Germany and attendees could test and feel it. It is fitted with haptic feedback that adjusts to the hand of the pilot on the single power-lever by means of different movement resistance and produced “bumps” for different power settings in a transition from pure electric to combined flight (ICE plus battery power) mode.
Tine Tomazic of Pipistrel and Frank Anton of Siemens will attend the Sustainable Aviation Symposium in San Francisco on May 6 and 7, a great opportunity for new information on the project. For more information visit sasymposium.com.
The Testing
Following the extensive laboratory testing of components and the integration on a representative airframe at the Pipistrel aviation factory in Slovenia, the successful power up trialed all propulsion modes at low and high power settings, driving a specially developed five-blade, low-rpm, low-noise propeller. Tests of take-off power were performed using combined output of the generator driven by a Rotax 914 turbocharged combustion engine - which is commonly used in aviation - and the high-performance battery system, which was custom developed to support high discharge rates. During the first tests all components were installed into the aircraft beside the battery pack that was located in a trolley. The batteries were not on board because the aircraft in this initial test phase was first tested indoors and lack of space dictated this solution.
In the upcoming months, extensive testing will continue to simulate typical mission profiles covered in the performance study and to validate the hybrid drive concept and performance. Besides this, the final installation of the remaining and now missing components will be performed: batteries installation in the wings, HMI - single throttle lever will be built-in (for static testing an external unit was used as the aircraft was unmanned), and the cowling will be adapted to the new powerplant with installation of intake ducts.
“In technical progress, there have always been small steps that demonstrated how reality can be even more creative than imagination," says Max Pinucci, CEO of MBVision. "This success opens the way not only to the future hybrid/electric flight, but to endless opportunities of research in technology and design, representing the true patrimony in which we must invest."
For more information visit www.hypstair.eu, www.siemens.com, www.um.si, www.unipi.it, www.mbvision.it, or www.youtube.com/watch?v=x1Xrr82Hbkc.
HYPSTAIR Project
The HYPSTAIR project has received funding from the European Union’s Seventh Framework Program for research, technological development, and demonstration under grant agreement No. 605305. Project partners are Pipistrel d.o.o. Ajdovščina (as project coordinator and Igor Perkon as project manager), Siemens AG, MBVision, University of Pisa, and University of Maribor.
The HYPSTAIR project concerns the design of components of a serial hybrid propulsion system for small aircraft. A serial hybrid propulsion system uses an electric motor to drive the propeller. The electrical power can be sourced either from a battery pack, that can be recharged during the flight, or from an on-board fuel-powered generator. This propulsion system will enable future small aircraft to operate with lower emissions and lower fuel consumption, thus reducing the environmental impact and travel costs of aviation. The project deals with the conceptual design of the hybrid propulsion system components. The components will be sized and designed considering the performance and energy efficiency of the complete airframe-propulsion system, and will be tested in a laboratory environment. A dedicated human-machine interface will be designed allowing simple operation of a complex hybrid system.
Together with the reliability of electric motors and use of dual energy sources, the system built upon these components will improve the safety of flying. The design of all components will comply with safety and certification standards. As currently no regulations for aviation hybrid drive systems exist, defining these standards, in collaboration with the authorities, will be an important contribution of the project paving the way for introduction of hybrid and electric technologies to the market. These efforts will help to create a competitive supply chain for the hybrid drive components and to reduce the time to market of such innovations.
HYPSTAIR at E² Flying Symposium, Stuttgart, Feb. 18 – 19, 2016
Hypstair project in cooperation with the German DLR (Deutsches Zentrum fuer Luft- und Raumfahrt e. V. (DLR), German Aerospace Center (DLR), and the University of Stuttgart organized the Symposium E2 Flying. The symposium addressed the challenges related to implementation of aircraft with electric drive. Participants focused on details of the feasibility as well as scientific aspects. The progress of project HYPSTAIR and especially the results of the first power up of the world’s most powerful hybrid electric powertrain for aviation were presented for the first time. The hybrid electric powertrain represents a major step toward electric-powered air travel and sustainable mobility. The symposium, with around 150 representatives from universities, research institutes, and companies participated, was visited and addressed by Winfried Hermann, Minister of Transport and Infrastructure, Baden-Württemberg.
About the Author
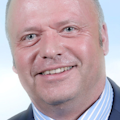
Marino Boric
Marino Boric graduated with a university degree as an aeronautic engineer, and acquired degrees in business development/trade and commerce and in journalism. He is a civil and military pilot and has built experimental aircraft. As a journalist, he specializes in aviation and propulsion and travels worldwide, flight-testing UL, LSA, Experimental, and certified aircraft. He is writing for U.S., European, and Chinese media companies.