How Today’s Tech Can Prevent Collisions
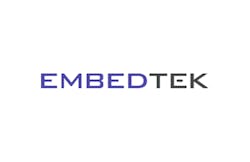
Picture this scenario – a business traveler is used to whipping around the airport parking structure in his SUV. He knows how to to park, go through security, stop for coffee, and grab a seat at the gate with as little waiting as possible. One morning the traveler is heading to his go-to parking area when the SUV suddenly slams into a clearance bar, wedging the vehicle in place. Shocked, the driver gets out of the SUV only to remember that he had installed a roof rack over the weekend, increasing the height of the SUV by 3 inches.
This scenario can – and does – happen in a similar fashion on the airport apron. Experienced and highly trained ground support personnel grow accustomed to working in sync with coworkers and standard operating procedures. But, the apron is a fast-paced working environment with many moving pieces. One slight change – taking over for someone out sick, working with a new plane, driving a different vehicle, even just a generally off day – and our mental auto-pilot fails us. Collisions occur that can cause serious injury and costly damage.
Technology is being used today that help personnel better sense what is around them. It’s common to be able to detect what’s in front of them, behind them, and even to the sides of them. It’s less common to also detect objects above them, but the technology exists to do that. Sensors can be installed on equipment and vehicles, similar to the back-up cameras and lane detection in cars that many consumers have quickly grown to rely on. Ground support personnel would work the way they always do with this technology, but would have the added confidence that their vehicle can alert them if they are in danger of a collision.
EmbedTek designs and manufacturers embedded sensor technology, including cameras, custom vision systems, computers, industrial display and supporting application software. The engineering and manufacturing facility headquarters are in Waukesha, Wisconsin. EmbedTek specializes in inventing new ways to enhance equipment safety, improve performance, and provide a level of consistency the human operator cannot achieve on their own. Following are a few technologies ground support equipment manufacturers can implement today to achieve this.
Obstruction Detection
Object Detection and Ranging (LIDAR) is a method using lasers to accurately measure distance by a technology called time-of-flight. LIDAR can be used on the vehicle or equipment to provide the operator with a real-time 3D map of the things around them as they drive. When the laser light detects an obstruction within a certain distance including height clearance – an alarm can warn the driver to stop and change course. This also can be accomplished with structured light camera systems or time-of-flight cameras, where instead of a laser, pulses of light are used to determine distance. Obstruction detection is particularly important for personnel operating a vehicle with blind spots and high clearance heights. Ultrasonic distance measuring systems and radar are also options but lack the ability to provide a detailed point cloud. As with autonomous vehicles, sensor fusion of a combination of these technologies usually proves useful.
Dynamic 3D Facility Mapping and Collaborative Detection
Beyond sensors and detection, a system that allows individual equipment and vehicles to communicate with each other is very powerful. This concept would use 3D attributes of the facility and all moving (or movable) objects on the ramp. 3D mapping software would be used to track all objects real-time throughout the entire apron with everything that is there – 3D models of each type of airplane, cargo equipment, maintenance vehicles, jet bridges, structures, and more. By using 3D dimensions of each object, the 3D mapping program will indicate where and when interference can occur before it happens. This software can provide peripheral knowledge of any vehicle an operator is driving. The absolute position known of every vehicle with GPS (and if needed, Ultra Wideband or UWB) and vector locations can also be detected with compass/gyro sensors which provides an apron manager the ability to determine where every vehicle – and every potential collision – is at all times.
Artificial Intelligence
Artificial intelligence allows apron management and personnel to create better rules for understanding where obstructions and interferences lie as software like 3D mapping is used. Artificial intelligence is a self-learning feature added to a software program that helps the program analyze, understand, and help improve the complex interconnection of all vehicles as they move around the apron on a daily basis.
The Flight Safety Foundation estimates that ramp accidents and incidents occur once per every 1,000 departures worldwide every year. Many organizations and airlines are working to reduce this number in an effort to protect the safety of personnel, aircraft, facilities, and equipment. Today’s software and sensors can easily be adapted into ground support equipment and vehicles to confirm when objects are getting close to one another, resulting in a drastic reduction in collisions, injuries, costs, and lost time.