Sensor Technology: Powering Precision and Progress in GSE
Mobile machines are essential workhorses in various industries, including aviation. One of the biggest trends in mobile machines is automating more of the basic functions of equipment.
On refuse trucks, for example, a driver only needs to know how to drive a truck. The machine can locate the container and lift it, while monitoring the hopper level and weight in the back.
Ground support equipment (GSE) plays a crucial role in ensuring efficient and safe aircraft turnaround times and is therefore seeing similar trends.
In recent years, automation technology has emerged as a game-changer, bringing a plethora of benefits, including enhanced performance, simplified operation and increased reliability.
Sensors provide real-time data on equipment operation, enabling precise control and optimization. Automation also reduces complexity, making GSE easier to use and requiring less training for operators. What’s more, sensor-driven monitoring and diagnostics identify potential issues early, preventing downtime and costly repairs.
Sensor Integration in GSE
Deicers were among the first GSE machines to embrace full automation. These critical systems require precise fluid application and boom positioning to ensure efficient ice removal without damaging the aircraft.
Sensor feedback empowers intelligent systems like JBT's EZ-Jib on the Tempest-i to control the boom with a single joystick, simplifying operation while maximizing effectiveness. Sensors monitor the real-time position and can even enable automatic stowing in the correct position.
Most GSE uses sensor technology to improve performance or safety in a variety of ways.
Lavatory service trucks, for example, utilize sensors that can monitor incoming and outgoing fluid levels, ensuring complete servicing before departure. This data can be recorded for improved equipment design, or simply show the operator a red/green alert to indicate the service is complete.
On towbarless pushback tractors, pressure sensors in the equipment verify secure grip on the aircraft wheels, adhering to nose landing gear (NLG) limitations and preventing damage. In the future, we may also see the machine identify the aircraft automatically to match manufacturer lifting guidelines.
When it comes to deicing technology, advanced systems like Safeaero's Intellimix use sensors to monitor fluid temperature before spraying, optimizing performance and ensuring passenger safety. This is another simple step that takes a complex task out of the operator’s hands, so they can focus on the intricate task of spraying the aircraft.
Emerging Technologies
In today’s GSE landscape, there is currently a race to implement a number of emerging technologies on machines.
Collision Avoidance Systems
The International Air Transport Association’s (IATA) Airport Handling Manual (AHM) 913 regulations prioritize safety, and collision avoidance system (CAS) technology helps prevent costly and potentially disastrous collisions between GSE and aircraft. This might include radar or lidar sensors to detect the aircraft from longer distances and short-range sensors for final positioning.
Combining these sensors with a high-performance control system can support slowing/stopping the machine before contact.
Remote Equipment Tracking
Sensors enable real-time monitoring of GSE performance and location, enhancing efficiency and simplifying maintenance planning. This data can be stored locally on an intelligent display for later analysis, or can be automatically transmitted to the cloud to manage the whole fleet at a glance.
Beyond the "must-haves," other sensor solutions offer valuable advantages.
Seat Belt Tracking/Operator Presence Monitoring
Seat belt tracking/operator presence monitoring is a simple technology that promotes operator safety by ensuring proper seat belt use or operator alertness.
This is sometimes integrated with the vehicle’s drive to stop an operator from moving if the seat is empty or if the belt is not fastened.
Electric Machine Battery Monitoring
Real-time data on battery health identifies potential faults or charging errors before they lead to disruptions or safety hazards. Over time, this data can be analyzed to identify where to invest in new equipment or when to refurbish existing equipment.
Technology adoption is constantly advancing, and new advancements can be expected soon.
Boarding Bridge Automation
Sensor-driven systems can automate bridge movements, dramatically speeding up gate turnaround times while ensuring passenger safety. The same technologies that are being implemented on other equipment can be applied here to improve this process. Most passenger boarding bridge (PBB) systems already incorporate automation for the auto-level system. It could easily be taken another step forward with sensors to measure distance to the aircraft and the angle of approach.
New Industry Requirements
As safety standards tighten, sensor and control technologies that comply with the International Organization for Standard’s ISO 26262 specification, which is focused on functional safety, will become increasingly important.
Sensors and program logic controllers (PLCs) that are rated to ISO 26262 have feedback that can detect faults as well as provide communication redundancies to assure proper sensor status. This allows the customer to create a system that achieves ISO 26262.
Right now, equipment manufacturers and end-users are optimistic that uniform safety standards will make it easier to guarantee safety on the ramp.
Sensor Technology’s Impact on the Future of GSE
Sensor technology is revolutionizing GSE operations, driving precision, improving efficiency and enhancing safety.
From deicing automation to collision avoidance systems, automation is empowering a new era of intelligent ground support. By leveraging the power of technology, we can ensure that GSE continues to evolve alongside the aviation industry, supporting continued growth and innovation above and below the wing.
Tim Conklin works in business development – mobile vehicle perception at ifm efector inc. ifm has implemented technology to support all applications for the ground support equipment industry. He can be reached at [email protected].
About the Author
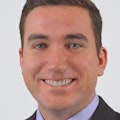
Tim Conklin
Tim Conklin works in business development – mobile vehicle perception at ifm efector inc. ifm has implemented technology to support all applications for the ground support equipment industry. He can be reached at [email protected].