Preventative Maintenance for GPU Cables
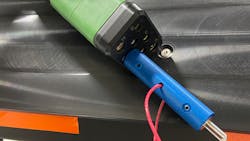
Preventative maintenance (PM) programs are crucial for proper ground support equipment (GSE) care. This applies to GSE of all types, from belt loaders and tractors to ground power units (GPUs) and pre-conditioned air (PCA) units.
But PM programs are important for GSE parts and components, too. When it comes to GPU cables, regular preventative maintenance is key to avoid serious injuries to ground personnel that use equipment with high electrical capacities.
The Importance of PM Programs
To extend cable life and improve the safety of your team, a basic visual inspection of the GPU cable should be done every time the cable is going to be used. Look for kinks, cracking, cuts, drag abrasion or a scrunched jacket. For example, after years of service, it’s not uncommon for a cable that is often used on 737s to have a banana-like bend sloping down the cable head. If a potential issue is spotted, it is recommended to perform a load bank test with a thermal imager to check for any hot spots.
Regardless of whether a visual issue is spotted during the inspection, load bank tests should be scheduled quarterly to make sure that the cable maintains satisfactory condition. Many facilities and GSE maintenance teams already have a regular GPU PM schedule, so be sure to check the GPU cable while testing the GPU.
Socket Retention in the GPU Cable Head
Using a proper cable test kit, the socket retention in the cable head should also be inspected regularly to ensure a proper aircraft connection. According to SAE document AIR4365A, loose cable contacts or worn aircraft phase pins can cause “hot plug” issues that can result in loss of the E & F control voltage leading to the aircraft rejecting the external power. Many times, when an aircraft rejects ground power, the GPU is the first thing that we troubleshoot. Often, the issue lies within the cable assembly, specifically at this connection point itself.
The cable head sockets should always have enough tension to hold the cable in place and support the weight of the cable held off the ground. You should never need to rely on a cable strap to hold that tension to the aircraft receptacles. Guidance for the acceptable tension can be found in Military Standard MIL-C-7974, which specifies an insertion force of 80 lbs. +/- 20 lbs. and a maximum extraction force of 100 lbs.
It is recommended that each phase socket (A-D) be tested with a pin gauge tool and a tension meter. Each of these four phases should test anywhere in between 15 lbs. and 25 lbs. The E & F control sockets will have a much lower tension requirement with a minimum of 1-3 lbs. If any phase falls short of the minimum requirement, it is time to replace the contact section of the GPU cable head.
Don’t Pair Contact Sections from Different Cable Providers
The very end of the GPU cable head, known as the contact section, sees more wear than any other part of the cable assembly. This is why several GPU cable manufacturers have developed replaceable contact sections, so that the end-user can replace just the worn-down end, saving a lot of money on lifecycle costs.
Do not, under any circumstance, swap a different contact section onto a different manufacturer’s cable. Each manufacturer has their own specially made contact sections, which only truly fit their cable. Many make the mistake of forcing a contact section onto another manufacturer’s cable; thus, creating a massive safety hazard that could easily lead to water intrusion, which in turn could lead to arc flashes or fires at the aircraft plug.
Adding this to your visual inspection before use any time you’re getting ready to power up would prove beneficial. If duct tape is being used to keep a contact section connected to the cable or to patch an exposed conductor, chances are this is a safety hazard and should be replaced immediately.
Cable Longevity
One of the most common questions we field from our customers pertaining to GPU cables is, “How long do they last?”
Although that’s a good question, there really isn’t a specific answer to it. There are many variables that contribute to the longevity of these cables.
Independent testing recommends that cables should be replaced after 4,800 insertions. In a hub environment with eight turns a day, that comes out to roughly two years. A high quality 400 Hz GPU cable is made to last several years in a very harsh environment. It’s not uncommon to find a cable still in use after 5-10+ years of service. Although we don’t like to put a set amount of time on how long a cable should last, a general rule of thumb is that if it’s been in use for longer than 10 years, we would recommend retiring it.
The older the cable, the more problems we tend to find. This is why implementing a preventative maintenance program to regularly check GPU cables is so important. Load bank testing with a thermal imager will be able to identify hot spots within the cable so that it can be replaced before the issue occurs.
This is especially important with older cables, which should be tested more frequently than newer ones. After a few years of service, if your cable is still performing at a high level, we would recommend scheduling load bank tests monthly for the remainder of the cable’s life.
Conclusion
Basic regular preventative maintenance is key. There are extremely high amounts of electricity passing through these cables every day and the ramp can be a brutal environment for all GSE.
Serious employee injuries can be avoided and expensive aircraft damage can be prevented by taking the time to effectively inspect the equipment before use.
With proper care and maintenance, a high quality 400Hz GPU cable will provide years of reliable service.
Bill Stahl is area sales manager at ITW GSE. He has been with the company's cables and hoses team since 2019. Since coming on board with ITW GSE, he has focused on being a consultant to his customers to ensure that they make the best connections to get the most out of their GPUs and PCAs. He’s always willing to assist with training and troubleshooting.
About the Author
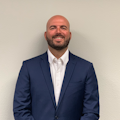
Bill Stahl
Bill Stahl is area sales manager at ITW GSE. He has been with the company's cables and hoses team since 2019. Since coming on board with ITW GSE, he has focused on being a consultant to his customers to ensure that they make the best connections to get the most out of their GPUs and PCAs. He’s always willing to assist with training and troubleshooting.