The End of the Runway for SAP Filters
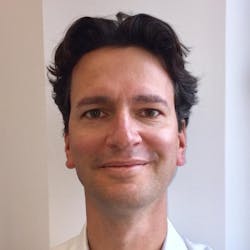
The aviation industry has faced many challenges this year – the global shutdown to contain the COVID-19 pandemic grounded planes, suspended routes and limited the free travel of people and goods that we have become so used to. Despite this, its critical role in helping to keep the world connected and transport vital supplies has been more important than ever.
But as the industry begins to look ahead to recovery and resuming operations, another challenge must be met: from Dec. 31, 2020, the industry standard controlling filtration systems containing SAP will be withdrawn, due to concerns about its suitability for use. In rare cases, SAP can leak from water filters into engines during refueling, causing operational issues.1
This follows a ruling by the IATA Special Interest Group in 2017 that Filter Monitor Elements are not fit for use in aircraft refueling due to concerns about SAP migration. While water is rarely present in aviation fuel, when this does occur, SAP has been used to prevent it from getting into the aircraft. However, when SAP – which is similar to the absorbent material used in diapers – reaches saturation point with water, it can leak particles of crystal-like gel. In rare cases, these particles can move into the aircraft during fueling and cause significant operational issues in engines.
As a result, the Energy Institute (EI) announced the withdrawal of the use of SAP by the end of 2020. This announcement has posed three challenges to the industry: finding a solution that can be certified in time, retrofitting this in the timeframe and at an affordable cost. But, when it comes to flying, safety has to be the ultimate priority – so this challenge must be met.
A Challenging Risk
Many aircraft refuelers have been fitted with SAP-based filter monitors that prevent water and dirt particles from getting into the fuel and engine. While the chances of SAP leaking are low, mitigating risks should always be one of aviation’s key priorities.
It was after Shell had been engaged as an independent, third-party expert by a major international airline that the potential, associated risks of SAP were discovered. We investigated why one of their flights had lost thrust control of both engines, resulting in a forced landing at twice the normal speed.
Seven further incidents were documented after this2, prompting a turning point in the industry. IATA convened a Special Interest Group in May 2014 to investigate the incidents, which found that the use of these SAP-based systems in aviation fuel handling is incapable of reliably meeting the aircraft and engine operating requirements3. As a result of these findings, the aviation industry committed to phasing out SAP-based water filters used in the refueling process.
A Solution from Innovation
While the EI has announced the withdrawal of SAP by the end of 2020, it is not a formal regulation. Despite this, it’s important that end users like airlines satisfy themselves that the risks have been properly mitigated when fuels enter their planes.
As well as being up to date on these developments, to ensure they are prepared for this change, aircraft refueling operators need to be aware of the alternative technology available to them. Since 2015, Shell has been working closely with filtration specialist FAUDI Aviation to find options to replace SAP. Over the course of these years, Shell has gained industry leading experience, understanding and operational knowledge of the operation of Electronic Water Sensors (EWS) and Dirt Defence Filters (DDF). By combining a new EWS and DDF, the result is Shell Jet Protection – a new system that guarantees a safe and secure flow of fuel every time.
By replacing physical water filters with an electronic water sensor extensively tested by Shell and qualified to EI1598, it can continuously monitor the refueling process and safely turn off the flow to the tank, on the rare occasions when water is detected. Another benefit is less waste. Its new filters are estimated to last up to five years compared to SAP-based filters, which need changing annually.
Tested, Available and Adopted into Standards
At a time where aircraft operators do not need anything else to worry about, Shell Jet Protection can also be easily retrofitted into existing vessels and vehicles at relatively low cost. After a full course of testing, the solution is currently the only SAP-free refueling system capable of utilizing existing filter monitor vessels available – and we immediately began the process of implementing Shell’s Jet Protection at all Shell operated locations across the globe to become SAP-free by the end of 2020.
Beyond the robust testing carried out by Shell, the FAUDI Aviation DDF and AFGUARD EWS technology used in Shell Jet Protection has now also become the first SAP-free system capable of utilizing existing filter monitor vessels to be adopted into standards by the Joint Inspection Group (JIG), a global organization for the development of aviation fuel supply standards4.
While there may be other companies working on alternative systems, such as Filter Water Separator systems, Shell Jet Protection is the only SAP-free refueling system currently available. By engaging on this issue as early as 2010 and dedicating our industry experience, understanding and operational know-how to finding a solution, we are committed to supporting the industry in this transition away from the risk posed by SAP.
Prioritizing Safety
Shell Aviation has taken significant steps to help prepare our industry for this period of transition. International airlines, including Lufthansa, and leading engine OEMs, such as GE and Rolls-Royce, have already publicly committed to no longer using SAP-based filtration systems after the deadline. We hope the rest of the industry will follow suit.
Thomas de Boer is head of operations at Shell Aviation. He joined Shell in 2001 and has held his current role since June 2018, following several management positions across Europe and United States. De Boer holds a M.Sc. in Industrial Engineering and Management from Twente University, Netherlands.
[1] In 2017, the International Air Transport Association (IATA) SAP Special Interest Group declared that SAP should be phased out of all aviation fuel handling systems, following investigations into eight recorded incidents where SAP had caused aircraft operability issues. This finding was upheld by the Energy Institute, which will withdraw its standard on SAP by December 31st 2020.
[2] IATA: IATA Super-absorbent Polymer (SAP) Special Interest Group – Data summary and proposed roadmap
[3] IATA: SAP Special Interest Group communication to all users of filter monitor filtration systems, 2017
[4] In August 2020, the Joint Inspection Group (JIG) issued Bulletin 130 which introduces Dirt Defence Filtration (DDF) in conjunction with Electronic Water Sensor (EWS) technology into JIG Standards. Bulletin 130 specifically relates to the FAUDI Aviation DDF and AFGUARD EWS used in Shell Jet Protection.
About the Author
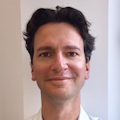
Thomas de Boer
Thomas de Boer is head of operations at Shell Aviation. He joined Shell in 2001 and has held his current role since June 2018, following several management positions across Europe and United States. De Boer holds a M.Sc. in Industrial Engineering and Management from Twente University, Netherlands.