Comparing Two Pressure-Step Method Tightness Monitoring Solutions: Fixed vs Portable
Aviation hydrant systems are the most efficient way to refuel aircraft. An underground network of pipelines takes the jet fuel from tanks straight to the aircraft, while data from the hydrant system is fed back into a supervisory control and data acquisition (SCADA) system.
Implementation of a hydrant system is dependent on a cost vs benefit analysis, largely based on the volume of fuel flow. Jet fuel management is simplified and you can easily keep track of inventory. But, just like any pipeline, it is crucial to have a compliant leak detection (tightness monitoring) system in place.
Leaks and ruptures can cause serious damage and even loss of life. Not to mention the financial damages associated with jet fuel loss, fines and grounded aircraft.
There are several technologies for jet fuel leak detection on the market, divided into two strategies:
- Internal methods that monitor fluid properties (i.e. pressure or volume)
- External methods that monitor for fluid release
Here we compare two leak detection technologies from Atmos International that monitor and analyze pressure using the pressure-step method. A fixed tightness monitoring system that integrates with SCADA and a portable tightness monitoring hardware solution with communications and the ability to display data locally, both use the same algorithm. This comparison will help aviation experts understand which type of tightness monitoring is best to implement based on the needs and requirements of their airport.
Leak Detection Sensitivity and Temperature Effects
Aviation fuels expand when warmed and contract when cooled. This means a small temperature change leads to a large change in pressure. For this reason, the pressure-step method accounts for pressure change due to temperature, making it highly sensitive.
Both the fixed and the portable solution from Atmos can differentiate between pressure changes due to temperature and pressure changes due to product leakage from the hydrant system.
Compliant Tightness Monitoring
It’s important to check the compliance of the system and that it is correct for the region it will be used in.
Both fixed and portable solutions must be compliant to a high standard. For the European Union (EU) the applicable standards are set out in EI 1540, EI 1560 and JIG 2, for North America they are set out by the United States Environmental Protection Agency (EPA). Often, aviation hydrant systems are divided into segments, the standards specify a minimum leak rate per volume of segment or leak rate depending on the volume range of each segment.
Hardware tightness monitoring solutions are connected to the hydrant and involve the transfer of jet fuel, for this reason they must comply with local regulations for explosive atmospheres. That’s why there are two versions of the Atmos Portable Tightness Monitor (APTM), one for the EU and rest of the world which is compliant with ATEX and IECEx and one for North America, which is compliant with HAZLOC.
Pressure-Step Method Implementations
Fixed hydrant testing systems that use the pressure-step method require a minimum level of instrumentation on the pipeline, so can be retrofitted if these requirements are met.
Fixed testing systems require at least:
- A single pressure transmitter per segment
- Tight isolation valves that are motorized (MOVs) and must be controlled by a SCADA system
- Double block and bleed (DBB) valves as recommended by the standards
- A methodology for depressurization (such as a bypass line)
- A SCADA system that is OPC compliant
Investments in civil and electrical works may be required if the hydrant system doesn’t already meet these requirements. However, once in place the maintenance is low and the whole hydrant network can be tested in one session, regardless of the number of segments. This makes a fixed system a high CAPEX but low OPEX solution.
Unlike the fixed system, the portable hardware solution doesn’t require any investment in the existing infrastructure, it’s an off the shelf solution. The APTM for example wheels around in two Peli cases, so hydrant operators can easily lift the hardware on and off the back of a truck. For these reasons, a portable solution like this is well suited to hydrant systems with no previous instrumentation if the budget won’t allow for further CAPEX investment in the pipeline.
Hydrant Integrity Test Process and Results Speed
Since hydrant systems cannot be in use while integrity tests are carried out, it is vital to consider the length of time the solution takes to deliver test results.
A fixed pressure-step method hydrant test starts at the touch of a button through the SCADA system, the Atmos Tightness Monitor can complete this test in 30 minutes.
As a hardware solution, the portable tightness monitoring requires more human resource. The compact APTM for example needs two people for assembly and test completion. Unlike a fixed solution however, portable tightness monitors test one segment at a time.
Cost and Impact to Airport Operations
Both systems have minimal impact on airport operations once installed and configured, with each having quick test times.
Fixed tightness monitoring solutions are a project based delivery, instrumentation is required to be implemented if it doesn’t already exist, the SCADA system needs to be configured and there may be standards like ISO to meet on the supplier’s side. While subject to configuration, the portable solutions like the APTM are ready to go out of the box and are one off purchases.
It’s also important to consider additional costs such as commissioning and shipping and whether they are included as part of the price. There’s also the cost of ownership, aspects integral to fixed systems like a replacement pressure transmitter can be sourced locally, however specialized hardware may take several months to arrive, particularly when you factor in constraints like customs checks.
What is most cost effective for the airport depends on how much budget there is to spend on upgrading the airport hydrant system to the required instrumentation versus the manpower required to test each segment during curfew time.
Data Interpretation
Data for the results of the fixed solution are pulled straight through to the SCADA system. With the Atmos Tightness Monitor there is also a separate GUI offered and remote access options, enabling a more detailed analysis of data.
Portable solutions like the APTM can use 4G communications to provide experienced Atmos aviation engineers with an instant view of the data. It also means that Atmos can support customers while they are doing the test live on site.
Both solutions also help hydrant operators troubleshoot and fill knowledge gaps into the integrity of the pipeline. For instance, they can differentiate between passing valves and a leak.
Selecting the Right Tightness Monitoring Solution
Fixed and portable pressure-step method tightness monitoring are both well equipped for providing accurate data about the integrity of aviation hydrant systems. The implementations are vastly different although the underlying physics principles are the same, but once up and running both meet the minimum compliance requirements set out in EI and JIG, provide quick test results and have little to no impact on airport operations.
Deciding between fixed and portable comes down to three core considerations:
- The play off between CAPEX and OPEX
- How much budget and downtime you can invest if existing infrastructure needs upgrading
- The human resource you have at your disposal to carry out tightness monitoring tests
It’s also important to consider the provider you select when making this decision and how they will help your engineering teams optimize the tightness monitoring solution.
Dean Golba is head of aviation for Atmos International and is responsible for developing the market strategy for the range of Atmos aviation products for fuel hydrant leak detection. He has been with the company for more than 10 years and has played a pivotal role in developing the Atmos Tightness Monitoring systems, including the Atmos Portable Tightness Monitor with its 15 minute test times.
About the Author
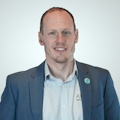
Dean Golba
Head of Aviation at Atmos International
Dean Golba is head of aviation for Atmos International and is responsible for developing the market strategy for the range of Atmos aviation products for fuel hydrant leak detection. He has been with the company for more than 10 years and has played a pivotal role in developing the Atmos Tightness Monitoring systems, including the Atmos Portable Tightness Monitor with its 15 minute test times.