The Importance of Pit Valve Integrity
At a commercial airport, hundreds of flights take off and land every day, with each aircraft coming into contact with the airport apron multiple times in a 24-hour period. Most passengers board and disembark the aircraft on the apron, cargo and luggage are typically exchanged on the apron and most crucially to an airline’s continued activity, the apron is where aircraft refueling takes place.
As yearly air traffic continues to increase, it’s become a necessity to refuel aircraft as quickly as possible, so many airports now operate a hydrant fueling system, which requires pipelines to be positioned under the apron. Fuel is transferred from a storage facility to the hydrant system where a hydrant dispensing vehicle connects to the hydrant pit valve in the ground and refuels the aircraft, typically via a refueling point in the wing.
As with other operations within the global energy industry, airports operating hydrant points are responsible for ensuring safe operations. Part of this involves supporting industry standards set by the Joint Inspection Group (JIG) and the Energy Institute (EI), which recommend hydrant operators perform monthly integrity checks on a fuel hydrant’s pit valve to determine if they have a “hot valve.”
The pit valve connects the fuel hydrant to the refueling vehicle, so it’s critical in the delivery of jet fuel to the aircraft. Failure to routinely perform pit valve integrity checks in line with international aviation standards from (EI) EI 1584, EI 1560 and requirements from JIG2 can have consequences on the operations of a commercial or military airport, resulting in safety implications on the refueling of aircrafts and significant financial costs.
For this reason, airports typically have an embedded process for pit valve integrity checks. However, some are more effective than others.
Current Process for Pit Valve Integrity Checking
One or two fuel hydrant operators manually check an airport’s pit valves by driving to each hydrant pit valve’s location. A large airport can have as many as 1,000 pit valves and each one requires hydrant operators to lift the pit valve lid and perform the test using either a heavy hydrant coupler fitted with a pressure gauge, pressure bleed valve and stainless steel bucket to contain discharged fuel or a pole fitted with a shield to contain the leaked jet fuel within the pit box.
Both these methods present the following challenges:
- Each valve only takes a few minutes to test but the number of pit valves paired with the size of an airport turns pit valve integrity checks into a significant time and resource expense
- Increased risk of jet fuel being released into the environment when connecting the coupler to the pit valve, which presents health and safety risks to staff, especially if the hot valve seals have failed and are already hot before an attempted inspection
- Costs incurred as part of maintaining the hydrant refueling operation
- Refueling staff are still at risk of connecting to a hot valve because pit valve integrity checks are only performed once a month and not before every refueling activity
- Results are logged on pen and paper and are subject to an individual’s interpretation or even risk becoming lost or damaged in inclement weather
New Technology for Pit Valve Integrity Checking
In response to the currently long and arduous process for performing pit valve integrity tests, technology has emerged which can digitize the process while saving time and streamlining operations.
Removing the Heavy Lifting
Hardware solutions like Atmos Pit Sentry are fixed directly to the pit valve and detects hot valves without hydrant operators needing to obtain a heavy coupler or pole from their vehicle.
Digital Logging
Hardware solutions have capacity for digital logging. Instead of manually recording the status of each pit valve with pen and paper, hydrant operators can utilize app connectivity via Bluetooth when they arrive at a hydrant point that contains a pit valve with the hardware installed. Atmos Pit Sentry creates its own audit trail of data logs.
Robust Communications Protocol
While manual processes rely entirely on the human element, hardware solutions fitted with a communications function can raise alarms directly to paired devices in the event of a pit valve issue, while communicating with hydrant operators in the form of go/no-go LED indicators when they lift the pit valve lid.
Intrinsically Safe
Hardware solutions like Atmos Pit Sentry are made from a dual construction of plastic and stainless steel so they can be fully submerged in fuel without damaging their integrity or ability to digitize the pit valve integrity testing process.
Supports Industry Standards
It’s vital that any hardware solution in the aviation industry works within the frameworks of JIG and EI, because JIG is in place to ensure aviation compliance and the safe transportation and storage of fuel to some of the world’s largest airports while EI have set standards to encourage safe operations with the global energy industry.
Atmos Pit Sentry works in support of international aviation standards from (EI) EI 1584, EI 1560 and requirements from JIG2.
To ensure a safer, time saving and cost effective routine of monthly pit valve integrity checks, hardware solutions are a vital part of the process.
Dean Golba is head of aviation for Atmos International (Atmos) and is responsible for developing the market strategy for the range of Atmos aviation products for fuel hydrant leak detection. Golba has been with Atmos for more than 10 years and has played a pivotal role in developing the Atmos Tightness Monitoring systems, including the Atmos Portable Tightness Monitor with its industry leading 15-minute test times.
About the Author
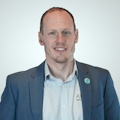
Dean Golba
Head of Aviation at Atmos International
Dean Golba is head of aviation for Atmos International and is responsible for developing the market strategy for the range of Atmos aviation products for fuel hydrant leak detection. He has been with the company for more than 10 years and has played a pivotal role in developing the Atmos Tightness Monitoring systems, including the Atmos Portable Tightness Monitor with its 15 minute test times.