“I can still remember the very first airplane I ever fueled, back in 1975,” says John Lindner, risk operations manager for EPIC Fuels. “My training consisted of: ‘See that airplane over at the pumps? Fill it with fuel.’”
After a long career which has spanned positions such as a line manager, tank farm manager, fuel buyer, ground support, contract maintenance, and more, Lindner came to work at EPIC and brought years of on-the-airfield experience and industry know-how with him.
He is one of five inspectors who help FBO customers nationwide control their risk factors when it comes to fuel. A large focus of this risk assessment is on training. He says he and his team review training policies, and make sure those policies are current and tasks are being completed properly.
“Training is weighted quite heavily on our checklist,” Lindner says. “You could be fueling out of maybe some of the worst conditions, but if you’re trained and know how to do it safely and properly, it can be done. Training is the core of everything that happens in my mind.”
As a 45-year industry veteran, Swissport Fueling Inc.’s operations and safety manager Joseph Kastelitz concurs. He says the difference between fueling and other ground support tasks is that fueling is a one-man job.
“The fueler has to be very well trained and then we have to have a lot of supervision to make sure they are doing it correctly,” Kastelitz adds.
Hire the Right Person
When it comes to fuel training, the professionals agree a quality employee is essential to a successful equation.
“You have to be geared up to train somebody that has no idea about aircraft simply because our industry is so small,” says Wallace Sublett, flight support manager at Superior Aviation Company (SACjet), which includes PATCO, Sacramento International Jet Center and Mather Jet Center. “Rarely do we come across individuals that have been in the industry very long or at all.”
For that reason, he says their training program is geared toward a new employee that is also new to aviation, and that with SACjet’s three locations, new employees have the opportunity to be trained on anything and everything that has to do with the industry.
Lindner says he’s had employees offer to work for free, simply because they want to be around airplanes in order to be a pilot someday.
“I’m not kidding,” he says with a laugh. “I told them I had to pay them – it’s the law, but some of them were the best employees I’ve ever had because they were driven.”
Woman or man, it doesn’t matter, he adds, saying: “I’ve had a number of women fuelers that were super and very detailed oriented. The start of this process is getting the right person.”
Sublett couldn’t agree more. He says that even by offering the best training in the world, difficulties will follow if an employee is not willing to learn.
It can be hard for FBOs to find people, and Lindner says flight schools are good places to look. Word of mouth helps too, as do the traditional job notification methods such as papers and online ads.
To address turnover, SACjet has based its pay structure off training accomplishments.
“The more they do, the more money we put in their pocket and it’s worked out quite well,” Sublett explains, noting that employee retention improved 90 percent after that. “Turnover is very bad. It leads to accidents, incidents, mis-fuelings and other things you don’t want. People who stick with you are trained, provide safety on the ramp and are better for customers.”
Determine a Starting Point
NATA’s Safety 1st training is the industry standard for fuel training, Sublett says, and what he uses to form the base of SACjet’s overall training, but he says standard operating procedures (SOPs) should be unique to each airport and FBO.
“You can’t just have a guy watch a couple of videos and put him on the ramp from day one,” he adds. “They need to be exposed to fueling and everything out there.”
Lindner agrees that where to start with fuel training is tricky. Other than the standard regulations for training, he agrees it’s best if ground support training professionals develop site-specific protocols.
With constantly changing protocols, Sublett says it’s difficult to manage, but it’s easier to fill in these things if a core training program is in place.
Kastelitz finds the same thing in his role, since his job is to make sure the SOPs match the actual training being done. When the airlines update their fuel manuals to changing regulations, he says his team then updates its manual, and so on.
Fire safety is a starting point for fuel training but determining nozzle pressure for a 737 isn’t.
“Just the awareness of being at an FBO, on the airport and around fueling equipment has to be first,” Lindner notes, adding the supervisor needs to make sure the new employee has a good head on his shoulders while on the ramp.
Step by Step
Classroom training comes first, says Kastelitz. Students must have a passing grade of at least 80 percent in the modules, which covers eight days. His classroom portion covers every aspect of fuel training, from reviewing equipment such as filters, meters and valves, and then goes into fire safety training. Kastelitz says this is very important training, also required by the FAA and used in Swissport’s locations worldwide.
“The fueler learns to put out a fire, what type of fire extinguishers to use and spill control,” he explains.
He then says that much of the training regarding fueling planes truly relates to safety, and that message is shared from day one. From reflective apparel to mobile equipment, Kastelitz says the fueling area of an aircraft is very congested and employees must know how to use safety devices, but also make sure the aircraft is 100 percent safe, by focusing on quality assurance checks.
This and more are covered in classroom training, and from there, fuelers must complete airline training, go through every module to learn aircraft types and each unique plane’s fueling procedures.
“We’re trying to make sure whoever is sent out to fuel an airplane is 100 percent confident and actually knows what they’re doing,” he says.
Swissport recertifies its fuelers every year, then up to three years for airline training, depending on the airline’s requirements. Sublett says it’s about the same for SACjet’s trio of locations.
After intense classroom training comes intense on-the-job learning, which lasts up to 15 to 20 days, depending on how the student is progressing, Kastelitz explains. The length of this also depends on how many airlines they are working with at a given airport. The company calls its airside trainers “coaches” and once the student becomes very confident, the classroom trainers head out to make sure that person is ready to be on their own.
Final Thoughts
These professionals saw the days of VHS tape training videos for fueling education, so online training from NATA has been a big deal. They agree it works well, and the Safety 1st program is improving every year and is very important to their fueling programs.
Sublett says the classroom, online training modules followed by practical, hands-on training has worked really well for SACjet.
“When they get out on the ramp, things resonate better with them and once they’re involved in the process, it makes more sense,” he points out.
With so many planes and fueling nuances, he explains that training will never be fully completed and that it’s an ongoing process, with serious repercussions if not taken seriously. So, he wants his employees to also be trained to ask questions and come to others when they aren’t sure.
“Training is always an explanation of why we do things,” Sublett adds. “You have your book and list of things, but you really have to help them understand why we are wearing 100 percent cotton clothes, bonding the aircraft, etc. I could tell them to attach the bonding cable to the plane every time they fuel, but has anyone told them what would happen if they don’t?”
Regardless of employees or changing regulations, Lindner says having a constant, well-defined training program and someone to oversee it is key. He believes that having the “constants” is the “best” best practice a small-town FBO or the largest operations in the business could have.
Follow Guidelines
Joseph Kastelitz, operations and safety manager at Swissport Fueling Inc., says that as new industry regulations are adapted, the airlines and service companies then add those regulations into their documents. In his fueling role, the team follows quality assurance guidelines adopted by the airlines and oil companies which supply fuel.
These documents are produced by the top experts in fueling, Kastelitz says, including:
- JIG (Joint Inspection Group) – used worldwide except in the United States and Canada
- ATA 103 (Air Transport Association) – used in the United States, Mexico and Canada
- CSA Standards (Canadian Standards Association) – used in Canada.
- NFPA 407 (National Fire Protection Agency) – used globally for fueling safety requirements
- IATA (International Air Transport Association) – fuel servicing guidelines, used globally for fueling, and quality assurance
- EI (Energy Institute) – used globally for quality assurance
About the Author
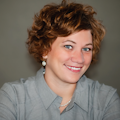
Jen Bradley
Jen Bradley, owner of Bradley Bylines, is an aviation writer based in East Troy, WI. She may be reached via her website at www.bradleybylines.com.