The story behind a Canadian invention that’s won four technology awards and taken the aviation market by storm first began as a persistent customer request from Latin America – make a fabric bulk fuel tank that could fit inside an aircraft.
“It wasn’t an easy request,” says Paul Reichard, remote site division manager for SEI Industries Ltd., a manufacturing company located in Delta, British Columbia, Canada and the maker of the Bulk Aviation Transport Tank (BATT).
“After working with Colombian law enforcement officials for many years, we were asked to produce a collapsible tank that could fit inside the aircraft they were using for drug interdiction operations,” he explains.
“Although SEI already made collapsible fuel storage tanks that sat on the ground, this new tank would have to carry bulk fuel in an airplane and be able to withstand any aircraft maneuver thrown at it,” he adds. “At first, we said no. Then, maybe. Finally, after brainstorming and consulting with our engineers, we said, yes, we can do it.”
Today, thanks to the persistence of that customer and SEI’s willingness to overcome some significant engineering hurdles, there are now dozens of BATTs in service, spread across five continents including North and South America, Asia, Africa and Europe. BATTs are also being flown in the South Sudan, Congo and Mali under the United Nations (UN) flag to support its missions.
From single Otter aircraft to the much larger Boeing 737, the BATT has made a lasting impact on aviation and revolutionized how bulk fuel is delivered to remote locations. To date, SEI has patented the BATT in the United States, Colombia and Canada.
Building the BATT
BATTs are comprised of two main components: a heavy-duty, abrasion-resistant outer tank that also serves as secondary containment (with a built-in strapping system) and a baffled inner tank. SEI’s design is the first one in the world to incorporate a baffled inside tank – a component critical to preventing the moving and sloshing of the fuel load while in flight.
“One of the challenges was coming up with a fabric-based baffle system that can be welded inside the BATT while in a flat state. The solution is rather complex since each baffle is a set of flat panels with several holes cut into them that allow the transfer of fuel. They are welded in position on the tank body panels and, as the tank is closed into a cylinder, the baffles are tied together with a fabric strip,” says Reichard. “It takes more than 200 welds to complete this section of the tank and, once the tank is welded into a cylinder, a strip of the same fabric is used to connect the baffles together.”
Although it took a number of tries, SEI’s engineering efforts also resulted in the development of a new proprietary seaming method to ensure that no edges of the fabric “scrim” are exposed to fuel. This seam edge encapsulation prevents fuel from wicking along the nylon base fabric which provides the structural strength of the BATT – strength that is needed to withstand the high pressures used during testing.
Once these design issues were overcome, the actual building process was also long and complicated but necessary to ensure the safety of the tank and the aircraft using it. On the BATT’s inner tank, SEI welds the fabric panels that become the body of the tank together using radio-frequency welding and cross seam construction.
The BATT’s rounded end caps are welded together and both the end seams of the tank body and end caps are encapsulated. On the outer tank, the same steps are followed except that the baffles are now replaced with a series of harness straps, welded in place.
During the final assembly and after the inner tank and outer tank are leak tested separately, they are brought together by rolling up the inner tank and installing it through the open zipper on the outer tank. The BATT is secured by a handle system that attaches both ends and sides of the two tanks together. Its flanges are bolted together and then the tank is zipped up.
Once the tank is complete, it goes through a series of leak tests. If the tank is a first article model, it needs to pass an aggressive pressure test where the tank is subjected to a four times or nine times over pressurization test (depending on the version).
By overcoming a variety of engineering hurdles, the BATT was eventually launched in 2010 with the first tanks being delivered to the same Colombian client who had initially suggested the product.
Winning Awards
For many, the idea of transporting fuel in a fabric tank inside an aircraft sounded impossible and unsafe. But, thanks to engineering excellence and innovative manufacturing, the BATT not only became a reality but also a four-time award winner.
The BATT is designed in such a way that each tank can be customized to fit each specific aircraft in which it is used. This customization means more work for the engineering team as they create individual aircraft-specific BATTs but, in return, the air carrier receives a product that is purpose-built and won’t cause damage to the interior of an aircraft.
Almost immediately after its launch, the BATT began winning awards. In 2011, Canadian Manufacturers and Exporters (CME) in collaboration with the National Research Council of Canada Industrial Research Assistance Program (NRC-IRAP) recognized SEI’s development of the BATT with two awards; a regional award (BC) for new technology and a national award in the same category.
In 2012, the Industrial Fabrics Association International (IFAI) selected SEI and the BATT for its International Achievement Award (IAA) for design excellence in specialty fabrics applications. In the same year, the IFAI also recognized SEI and the BATT with an Honors Program award in the industrial applications category.
Changing a Decades-Old Practice
With so many operations located in remote areas with little infrastructure, fuel supply is a serious business for isolated communities, mining camps and other commercial and military operations.
For the past few decades, drums and metal tanks have been the most common way to fly in bulk fuel but these options are not without a number of disadvantages. Drums can leak, be difficult to move and are ill-fitting with aircraft interiors. Another option, metal tanks, are inconvenient installations that rob the aircraft of any cargo flexibility.
With these two methods, once fuel is off-loaded, the aircraft is then forced to depart with empty drums or an empty metal tank. Understandably, this doubles the actual cost of fuel delivery simply because the aircraft cannot be utilized for any other cargo on the return flight out. With the BATT, once fuel is off-loaded, the collapsible tank can be rolled up and other cargo loaded in.
In addition to its versatility, the BATT also helps remote site operators drastically reduce or even eliminate the use of fuel drums.
Since many sites don’t have year-round fuel delivery from tanker trucks or barges, now, with the development of the BATT, remote site operators have an innovative option that is both economical and efficient. Operators can fly fuel in, empty the BATT, roll it up and then head back with a full load of cargo or passengers – saving nearly 50 percent over other methods.
The BATT comes in a range of sizes to fit various aircraft. The model list includes small aircraft like the Cessna Caravan and Twin Otter right up to the much larger heavy lifters like the Hercules and Boeing 737.
About the Author
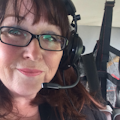
Nancy Argyle
Nancy Argyle is one of Canada’s most experienced disaster communicators. Based on Vancouver Island, she is a university lecturer, former print reporter and strategic communications consultant who writes on a variety of topics. She also holds a commercial fixed-wing pilot’s license.