Safety Support for Australia’s Aviation Industry
Quality and compliance monitoring systems are established ways of supporting safety performance management in the aircraft ground handling industry.
An important aspect to highlight regarding the quality and compliance systems implemented in ground handling companies is its overall level of sophistication. Indeed, such systems have been established in the industry for a long time and they have been tested and continuously improved more thoroughly than more recent safety management practices.
Sophisticated Systems
Ben Ryan, manager QHSSE (quality, health, safety, security and environment) at Swissport Australia believes there is significant sophistication of quality and compliance systems, because at a minimum they need to meet or exceed the client requirements, which are regulated by aviation bodies.
“These systems must also meet or exceed the workplace health and safety regulations in the areas operated and we know that the most effective way to achieve this is to meet or exceed the most stringent requirements,” he says.
The quality and compliance system at Swissport is benchmarked against legislative and regulatory compliance, including the Civil Aviation Safety Authority (CASA) in Australia and the Civil Aviation Authority (CAA) in New Zealand, along with also being mapped to International Air Transport Association (IATA) standards.
“Where other international regulatory bodies, such as the FAA in the United States or CAA in the United Kingdom have more detailed recommendations or requirements, we consider or implement those recommendations in our own system,” says Ryan.
“At dnata we continually improve our processes to provide the best possible services to our customers. We focus on the standardization of processes together with effective assurance. Evidence of our standardized global processes can be seen via the dnata Corporate Governance Manual (dCGM), the dnata Integrated Management System (IMS) and also the dnata Ground Operations Manual (dGOM),” adds Lee Hogan, manager of global risk and assurance at dnata. “Together with our standardized processes, we have also aligned our assurance programs to demonstrate that ‘we do what we say we do,’ and to ensure that we have effective risk management. This approach is consistent with other high risk or safety critical industries.”
Requirements
There are specific requirements of aircraft ground handling companies when implementing quality and compliance systems. In Australia and New Zealand, ground handling companies are not directly legislated by the aviation regulators. However, over many years of collaboration, CASA has introduced Ground Operations Safety Advisory Forum (GO-SAFE) meetings where all stakeholders work together to improve safety in aviation, observes Ryan.
“As a contractor to an airline, we must meet the requirements of the airline and be able to demonstrate implementation, which is completed by audits on the operation and business,” he explains. “The specific features of such systems in aircraft ground handling companies are planning, policies, procedures and processes, training, leadership or supervision, reporting and just culture, monitoring and quality assurance and continual improvement.”
At dnata, as part of its standardization process, the dnata Global Standards and the dnata Ground Operations Manual provide all of its global operations with a common framework and approach.
“The aim is to ensure consistent quality delivery of our products and services. These global standards also meet the requirements of applicable regulatory and industry standards,” says Hogan. “Our assurance framework enables us to demonstrate that our processes are performed effectively and systematically, and that we can test the effectiveness of our risk controls and present dynamic risk profiles to management.”
Audit Outstations
A distinctive issue when auditing aircraft ground handling companies is the need to audit locations away from headquarters to ensure that even remote outstations operate to a common standard.
dnata has aligned its assurance programs so to ensure its assurance activities are focussing on the systematic issues.
“In order to improve audit effectiveness and reduce overall audit burden, we ensure our audits are risk- and time-based across our operations at each station,” says Hogan.
At dnata the assurance levels consist of three lines of defence.
The first line is that of business verifications and it includes task, activity and workplace verifications. The second line is that of dnata corporate audits to verify compliance with dnata global policies and standards, i.e. the dnata Corporate Governance Manual (dCGM) and the dnata Integrated Management System (IMS). The third line is that of group or independent assurance activities to demonstrate its systems and processes are functioning effectively.
“All of these assurance activities allow us to demonstrate our levels of operational discipline, i.e.: ‘we do what we say we do.’ Our assurance activities are also now transitioning to the utilization of mobile technology, with assurance activities being performed with mobile technology, e.g. tablets,” says Hogan.
Swissport’s quality assurance program ensures all operations are audited in line with a plan, through internal self-checks, independent internal checks and external stakeholder audits.
“It is critical that there is management engagement and the desire to continually improve. A quality assurance program is only as effective as the genuine desire to learn and improve, which is something we work extremely hard to foster at Swissport,” says Ryan.
Audit Redundancy
Audit redundancy is also a common feature of quality and compliance systems at aircraft ground handling companies.
Under current legislation and oversight of contractor requirements, many checks are completed on the implementation and effectiveness of systems.
“This means that a single station with five clients would receive audits from each of those clients and each of the client’s regulators every year,” notes Ryan. “The best way to remove this duplication would be to regulate ground handlers to ensure their systems meet a defined set of standards, therefore removing much of the duplication of audits.”
VTS Extends Services to Ground Handling
Vanuatu Terminal Services (VTS) is a subsidiary of Airports Vanuatu Limited, operator of airports in Vanuatu – an archipelago in the South Pacific Ocean.
While VTS’ core responsibility has been to manage a cargo warehouse, it has expanded its arms and is now providing ramp services. So far, VTS handles only Virgin Australia flights, some itinerant flights and military aircraft on request.
Other aircraft are handled by Air Vanuatu Limited, which has its own ground handling department.
“Our scale of operations is small but this year one of VTS’ objectives is to work on achieving the ISAGO standard. We have two ground handling agencies providing services at Bauerfield airport: Air Vanuatu Limited and VTS,” affirms Alex Henry of VTS.
“VTS ground handling personnel ensure to comply with all rules applicable to ground handling operations,” Henry continues. “Our ground handling department is audited annually by auditors from Virgin Australia and Air New Zealand. Currently, only Bauerfield airport is servicing international flights.”
About the Author
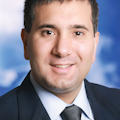
Mario Pierobon
Dr. Mario Pierobon provides solutions in the areas of documentation, training and consulting to organizations operating in safety-sensitive industries. He has conducted a doctoral research project investigating aircraft ground handling safety. He may be reached at [email protected].