Proper Training Resources Lead to Best Practices
Michael France says the real success story in FBO training is the entire industry coming together and saying, “let’s make sure we’re doing things the right way.”
France is the managing director of safety and training at the National Air Transportation Association (NATA), which has approximately 2,300 members across the United States, as well a growing international reach. The organization’s Safety 1st program and the 2014 launch of the International Standard for Business Aircraft Handling (IS-BAH) by NATA and the International Business Aviation Council (IBAC) have continued to strengthen and widen the industry’s training options.
“General aviation ground handling is not directly regulated,” explains France of the FBO community. “The success of Safety 1st is about aviation businesses, both large and small, participating through NATA committees to first build and then maintain and now improve the NATA Safety 1st program.”
The FBO industry is very self-governed, concurs Douglas Wilson, president and senior partner at FBO Partners, an advisory firm which consults with FBOs in a wide range of business areas. He explains that while obvious government regulations exist for pilots, mechanics, etc., when it comes to the day-to-day operations, FBOs are able to freely determine what works or doesn’t, even when it comes to training.
“One needs to consider what an FBO does as its core business, and then follow that trail in terms of training,” he adds. “FBOs voluntarily adhere to a set of best practices that are put together by industry organizations, such as NATA.”
This is good news, believes France, who says that independence leads to the flexibility FBOs need, and a mission by industry leaders to develop training resources they know are needed and why.
The Industry Standard in Training
To summarize an FBO’s overview on training programs, Wilson offers the analogy of a marina.
“You can get gas, park your boat, and have maintenance done. As a result, most of the training takes place around fuel quality control/handling and fire safety. And fuel suppliers provide, typically as part of their agreement with the FBO, training for employees on fuel-related programs, such as quality control (QC) and misfueling prevention.”
He says that while fuel companies do provide fuel-related training programs for FBOs they supply, there is often little available beyond that until you look at the national aviation organizations which have taken it upon themselves to develop these professional training standards and programs for FBO providers.
France believes that NATA has been a huge driver in evolving safety training for FBOs, ever since launching the Safety 1st program in the 1990s on VHS tapes.
Today, the program offers online courses in customer service, aircraft towing and handling and under-wing services, among others. Wilson says these training modules meet the industry standards/best practices and many FBOs use NATA’s online services for their training programs. Users can either buy a subscription or individual classes as needed.
France explains that since the program went online in 2008, it has continued to expand in class offerings to include the initial Professional Line Service Training program (PLST), as well as OSHA training, human factors, deicing, hazmat, general pilot, etc.
He explains that NATA is currently rebuilding the program from the ground up based upon member input. In addition to all new content, the program will change the way employees are certified. Instead of earning a certificate, as was the case in the past with the original PLST, the new system is set up to offer a ratings-based approach to training, focusing on specific functional topics such as towing, marshaling or refueling.
“The ratings-based approach provides immediate feedback to learners and they progress through training, allowing greater flexibility to companies in structuring their training program,” France summarizes.
NATA also offers a certified trainer program, to help FBO trainers learn effective instruction methods and how to design their program to meet their organization’s unique requirements.
“You know the old saying: You’ve seen one airport, you’ve seen one airport,” France says with a chuckle. “The same thing applies to FBOs. Our program is designed to be flexible, allowing businesses to focus on their training needs.”
Hurdles to Jump?
There are hurdles in the FBO training world, though. As flexible as training can be, the varying sizes of FBOs and the assortment of aircraft each FBO can see in the course of a year is definitely a challenge when it comes to training employees.
“At a smaller FBO, to spend $350 on training for a new employee that you just hired is a big decision,” acknowledges Wilson. “For the larger market FBO, cost is also a factor, but turnover is a bigger one.”
France adds that turnover increases the cost of training and is part of the reason NATA has moved toward a subscription model for Safety 1st.
“Under a subscription approach to training, a company can fix their annual cost, and if in the next month, half the staff has moved on, and they need to hire more people, it doesn’t cost anything more,” he explains.
Wilson says an FBO can combat these issues by establishing a hierarchy of training, starting with what tasks are most pertinent to an individual position.
“One of the first things an FBO employee learns is how to put fuel in an airplane,” Wilson explains. “By contrast, the person pushing the airplane back with a tug and towbar is probably one of the more senior people.”
He also says recruiting good people is an industry-wide challenge.
“This is an industry not a lot of kids know about. They’re not exposed to aviation and don’t even think to go to the local airport as a high-schooler and start looking at a job. It’s just not on their radar.”
Those that do look for a FBO job, he says, are often the same people who really want to be a pilot or aircraft mechanic down the road. This matters because Wilson explains the FBO employees then have a vested interest in doing well, as the airplanes on the ramp at the FBO represent a future employer to those would-be pilots or mechanics.
How Much is Enough?
When it comes to deciding what training is enough, Wilson says each individual FBO needs to decide what a “fully” trained employee looks like.
“What various tasks do line service employees need to have to be considered fully trained?” he asks. “It can be very complex when you consider how many aircraft types are out there.”
France says the same, and that an FBO needs to make internal decisions about how they value training, what they value in training and where to put resources, both financially and in manpower. Members call the NATA office often and ask for advice, and France says the staff is happy to help as much as possible.
Six months to a year is the typical length of time for an employee to reach the level of towing a plane, but that all depends on how much exposure he or she has had to the various airplanes and tasks ranging from fueling to deicing to towing, Wilson explains.
“It’s a shorter timeframe for an airline employee because they’re not operating 50 different aircraft types,” he adds. “They’re operating one or two, whereas the line service employee of an FBO needs to be able to know from memory how to tow, where the nose gear steering disconnects are, and the turn limitations of many different aircraft types.”
France says that having a trade association provide these training options is a huge benefit in this area.
“Our training is designed and overseen by the industry,” he notes. “Our mission is to assist our members in being safe and successful aviation businesses.”
To reach that goal, he explains NATA also has launched a Safety 1st on-site program, which is supplementary to the online options and provides FBO members a variety of industry trainers for in-person sessions. France says this is a way for FBO training staff to get help assessing training needs and developing an in-house educational program.
Resources are Available
“It’s really hard to sit in a dark room with pen and paper, and say, ‘what policies do I need to write? What guidance do I need to give my employees?’” notes Wilson. “IBAC has done that by creating the IS-BAH program. A lot of mid- and larger-market FBOs are starting to pursue IS-BAH because it marries recommendations on policies and procedures to a true safety management system program.”
FBOs are seeing and, more importantly, understanding, the value of becoming IS-BAH registered. The designation also translates into benefits in terms of less accidents, and by extension, insurance rates, he adds.
Through the IS-BAH standards – the first single standard for the global aviation industry – France explains that FBOs can refer to the section on training and find guidance in establishing their internal program.
“We don’t just look to our industry organizations to defend us on Capitol Hill, we look to them as the keepers of best practices,” Wilson concludes. “And, the industry doesn’t question those best practices because all of us within the industry contribute to the development of them.”
About the Author
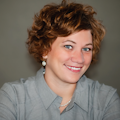
Jen Bradley
Jen Bradley, owner of Bradley Bylines, is an aviation writer based in East Troy, WI. She may be reached via her website at www.bradleybylines.com.