Great ground crews know that a speedy turnaround takes more than an eye on the clock and a can-do attitude. Safely and accurately fueling aircraft within a given window takes good planning and the right tools. But the most important element is the crew that handles both.
Let’s look at four best practices that keep operations on target and on time.
Talent: Attract and Retain the Best
If time is money, that can’t only be true of labor costs. It’s also true of the results. Aircraft fuelers are in a unique position to understand the cost of delay.
According to Airlines for America (A4A), the average cost of a minute of aircraft block time is $74.40 per minute. Fuel is a large part of that calculation, at $27.01, but not all of it. From that perspective, the time is worth more than the fuel. An engaged employee that will anticipate and prepare for the aircraft’s arrival in order to minimize the turn time (while remaining focused on safety) is a worthy investment.
Attracting and retaining the best talent also takes great management. An informed staffing model is a key best practice. In this case, “informed” means tracking all the variables that will impact refueling. That includes set up and break down time, as well as the actual flow rates for each aircraft. Without all those details, quickly developing staff schedules to meet flight schedules as they update is impossible. That can lead to frustration on the job and pressure to make up time, and that’s when mistakes can happen.
Considering the average cost of aircraft incident cited in an Alliance Group report is more than $50,000, avoiding mistakes is key, and retaining experienced supervising employees helps you do that. Look at the difference between a ground crew member with one year of experience, and one with less than one year. For ground crew members with less than a year of experience, there are 5.6 more safety violations per 1,000, according to Airport Workers United. That means keeping experienced employees around helps avoid safety issues.
Informed staffing also helps eliminate unnecessary labor hours, keeping the operation efficient while keeping your team engaged.
Training: Set your Crew up for Success
We’ve already seen that a good employee is worth investing in. A training program should be comprehensive and continuous. Compliance and safety needs are paramount, and continuous training is key to a safety-first culture. Fuelers need to be well-versed in specific technology, specific aircraft types and the airline’s standard fueling process and procedures. Additionally, having a top-tier aviation role to grow into within an organization provides a career path for high-caliber employees to pursue, thus reducing turnover.
There are two important benefits to keep in mind for training best practices. One is that employee training records show due diligence on the company’s part in the unfortunate case of an incident. Another is that training and opportunity (career progression, employee development) improves employee retention, by keeping employees engaged with learning new skills.
One way to balance the labor costs of training is to use computer-based training. Another way to avoid the start-up costs of a quality training program is to consider a specialized partner with established online training. An experienced solutions provider can help you start with a strong foundation of compliance and safety from the very beginning, protecting both employees and customers.
Technology: Stay on the Cutting Edge
Don’t hamper your team with technology that’s behind the times. The wrong tools could be slowing your team down, bloating your labor costs and risking delay.
Density hydrometers give your crew the actual fuel density at planeside. Since fuel density varies by temperature, calculating gallons per flight depends on an accurate measure of fuel density at the time and location of fueling. That keeps your team on target and reduces the danger of fuel venting on the tarmac. Fuel venting incidents occur mostly when the fueler attempts to load more fuel than the aircraft tank can physically hold. Providing the fueler with the current fuel density is another tool the fueler can use to ensure aircraft tanks are loaded properly without venting.
Upgrading to handheld fueling data technology also has numerous benefits. It eliminates the need to fetch paper fueling slips from the gate or dispatch, and speeds communications with automatic notices to fuelers. Handheld technology centralizes information for your team, providing required fuel loads and calculating gallons for them, based on density measurements they input at the point of need. The same technology speeds reports to the cockpit, and everyone from accounting to the tank farm, with one push of a button, sending gate changes, aircraft swaps and fuel load modifications directly to the refueler.
Real-time notifications of operational changes and assistance calculating volumes keeps everyone better informed, and that translates to improved safety.
Tools: Uniformity Fosters Excellence
Stationary fuel carts improve reliability by simplifying processes and improving safety. A stationary refueling cart already has a home on the apron, eliminating the need to compete with other ground support equipment trying to service the same aircraft. That reduces or eliminates potential damage to the aircraft, lowering your maintenance costs. Less equipment in motion around the aircraft also improves safety by reducing traffic on the tarmac.
Fuel stands set to preset heights allow teams to quickly and safely reach fueling panels. Some models incorporate a cradle that holds the fueling coupler safely during connection and disconnection. Bright orange paint keeps stands highly visible, and the wide platforms keep fuelers comfortable and safe while on the stand. Multiple locking mechanisms ensure the stand does not move during refueling, and the cradle automatically raises the refueling couple to the fueling panel, eliminating the need for fuelers to carry couples up the stairs.
The Right Team Has All Four T’s
Fueling teams face the same challenges across the industry, but how they overcome those challenges makes all the difference. A team that embraces best practices in attracting and retaining talent, establishes a great training program, and employs superior tools and technology fuels more than aircraft. That team fuels operational excellence.
Stan Livingston, Vice President of Aviation for ABM, specializes in providing into-plane fueling services and ground support equipment (GSE) refueling services as well as the maintenance and operation of on and off airport fuel storage and distribution systems at commercial airports globally. For more information, visit www.abm.com/aviation.
About the Author
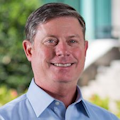
Stan Livingston
Vice President
Stan Livingston, vice president of aviation for ABM, specializes in providing into-plane fueling services and ground support equipment (GSE) refueling services as well as the maintenance and operation of on- and off-airport fuel storage and distribution systems at commercial airports globally.