GE Aviation Has a Strong (Turboprop) Footprint in Europe
AMT visited GE Aviation in Prague, Czech Republic this March. During the trip, the announcement of the name change of the ATP into the GE Catalyst was made. For us all, AMT readers and specially for aviators and maintenance personnel this visit was an excellent insight in GE Aviation activities in this entry engine (turboprop) field.
Life can be unpredictable and surprising, like this GE Aviation tour. The tour gave AMT the chance to transmit the news of re-naming the high-tech Advanced TurboProp (ATP) which is now called GE Catalyst. Second, even more important, this tour gave me a chance to (finally) understand the GE Aviation activities in Europe, their work in this engine field, and to tell you this story.
10 Years of GE's Turboprop Innovation in Europe
The activities of GE Aviation in Europe are much wider, deeper, and more important than I previously thought. I learned this from the best possible teacher, Bradley D. Mottier, vice president and general manager, Business & General Aviation & Integrated Systems Manager at GE Aviation. He narrated this fact in a passionate and proud way; he is a former entrepreneur, today’s GE Team leader, a pilot, and aircraft owner - what a blessing for a listener.
From today’s perspective it's easy to say that GE Aviation has done all things along this path right, but the path wasn't looking so straight a decade ago. It was mastered by the capable individuals which formed a great team. Thanks to Mottier, himself a catalyst in this GE structure, there was always a leader with a strong commitment and a clear final target. According to him, the beginning of the GE activities in Czech Republic was not an easy one.
Walter Engines As a Smart Purchase
It began with the acquisition of the Czech turbine manufacturer Walter Engines in 2008. The gem of the former Eastern turbines world was located in Prague and had an EASA certified turboprop powerplant in its portfolio. The mission from the beginning was to build a team, to build a business from virtually nothing requiring self-belief and perseverance. "Better be frugal" was a motto in those days. Acquiring Walter Engines allowed GE to learn the marketplace, gain domain expertise, and learn how those engines are being operated.
The initial problems were not the turbine properties but the location of the plant. As the former production terrain was sold by Walter owners, GE had to move the production to today’s site. This period was according to Mottier an "unbelievable six months" as they had to relocate each working bench and the overhaul of Walter Engines to a new location and re-building, actually mirroring it on a new location to retain the EASA certification.
Strong Help by the Authorities
In this process. Mottier highlights it, (GE) "was tremendously helped" by a Czech government/Czech invest program which strongly believes in aviation, by EASA and the Czech Technical University in Prague (CVUT). The Prague University is partnering with GE in development of the new powerplant and shares its acquired data with GE which in turn further develops all their products testing them in its own (certified) test cell.
CVUT is today conveniently located, adjacent to the GE Aviation plant; with a new test bench where the first fired Catalyst is now installed. It will stay there for CVUT and GE research activities; a CVUT test bench has already created unexpected benefits "a huge boost in student numbers which actually exceeds by 500 percent previous year's inscriptions" as per CVUT Professor Michael Valasek.
GE Improves the Efficiency of Existing Turbines
In 2009 GE launched the H80 engine improving the efficiency of the existing powerplant by implementing technological achievements from big commercial engines. GE added new compressor, new blisks, and stators. Doing so and adding in year 2010, the GT blade, the H80 has become 20 percent more powerful and 10 percent more fuel efficient.
In Prague at GE Aviation site we could see the new "H" series turbine on the swiveling and tilting test stand which was fitted with a modified oil and lubrication system which will allow aerobatic and inverted flight. This "H aerobatic" engine will power the Austrian Dart 550 military-basic pilot trainer aircraft manufactured by Diamond.
The Catalyst of a New Era
In 2014 the Advanced Turboprop (the ATP) clean-sheet-design was conceived based on experience made by existing engines, grown customers feedback, and customer insights and from that moment a new era had begun for GE Aviation.
The new 1,300 SHP-rated Catalyst is the first entry in GE’s new family of turboprop engines aimed at business and general aviation aircraft in the 1,000-1,600 SHP range; thermodynamically it is rated at 2,000 hp.
Catalyst work is predominantly being done in the Czech Republic, Poland, Italy, and Germany. The GE present position was reached through Europe-wide acquisitions (see below).
Now, this first engine has been transferred to the brand new test chamber of the Czech Technical University in Prague located on the same site. Fitted with hundreds of sensors "which required technicians to use watchmaker skills for positioning them properly" it will be used by CVUT and GE to generate more data and engine insights in field use.
The ATP features an industry-best 16:1 overall pressure ratio (OPR), enabling the engine to achieve as much as 15 percent lower fuel burn and 10 percent higher cruise power compared to competitor offerings in the same size class with better time between overhaul (TBO) and class-leading performance retention. Some of the ATP’s advantages are credited to the industry-first technology designed into the engine.
The use of additive manufacturing has simplified the engine's design, with fewer parts and solutions not feasible with conventional technologies, and also produced a lighter, more compact unit. The engine includes parts originally developed for supersonic jet engines. Its designers used 3-D printing/ALD to combine 855 separate parts into just 12, and deployed digital controls that allow pilots to fly commercial turboprop planes like jets. The use of the ALD technology allows e.g., a hollow design of the air intake screen to the compressor, through the hollow mesh oil generated heat to prevent ice crystals to be ingested by the engine.
More GE Catalyst engines are being assembled (the parts of the fifth Catalyst were in the final assembly room fine balanced during our visit) with up to 10 this year, which will be tested in the GE Prague test facility in coming months.
The first aircraft equipped with the clean-sheet Catalyst engine will be another clean-sheet design for the Cessna Denali scheduled to enter service in 2020.
Thanks to Catalyst's dual FADEC system (digital turbine control) this turbine will be much more fuel efficient than exiting designs and will give the turboprop pilots jet feel thanks to its single lever control. Thanks to its fully digital architecture - from the birth to resale - this engine will be run much more precise, burning less fuel, keeping the power to higher altitude because it has - first time in this turboprop class - variable stator vanes. The Catalyst will react faster to pilot input because the FADEC digitally controls not only the power but even the propeller pitch what according to Mottier means that full power means full power, or that any selected power will deliver exactly the selected value of available power. Simone Castellani, one of the lead development engineers of the GE Catalyst’s digital controls, said that the full authority digital engine and propeller control (FADEPC) will make flying turboprops so easy “my mom could do it. In a way, it is just like flying a scooter.”
This translates to a simplified cockpit, with a true single-lever operation, and ultimately less pilot workload. According to GE, the Catalyst family of powerplants will have on-condition maintenance - without any hot section inspection - and will have the ability to track exact flying conditions sending the engine flight data after landing to the manufacturer.
Digital Twin
Digital twin technology eliminates guesswork from determining the best course of action to service critical physical assets, from engines to power turbines. GE technology digs into any data, following the digital thread that defines its life-cycle. The thread starts with the development of a new jet engine/part, from the design through the build phase. This thread continues into the operation of the asset and its service history - all to predict what will come next, and suggest improvements and optimization throughout the cycle.
The digital twin is built on Predix, GE’s platform for the Industrial Internet, which enables it to unravel that data and discern what may happen next with an asset, while continuously learning and improving the models. This technology is a natural fit for the aviation industry, where unexpected equipment failure is not an option. In aviation, Mottier told us, for example, GE collects operational parameters of turbines installed on GE's two Honda Jets to predict maintenance and to prevent failures.
18 Years of European Activity
Born in Europe, GE Aviation's journey in Europe has gone a long way till it arrived at the current level. Many things happened on this path which can be condensed to this time line.
2000 - the GE Engineering Design Center (EDC) in Warsaw, Poland, was created under an agreement between GE Aviation and the Polish Institute of Aviation. EDC cooperates with GE businesses in aviation, but also in energy, oil and gas, and rail fields. The advanced hot section cooling technology was developed by EDC to meet the GE Catalyst’s high power and performance requirements. EDC design responsibility includes all development phases from the conceptual phase through engine certification, and key disciplines including systems integration, mechanical design, thermal, secondary flows, lubrication, and pressurization systems.
2007 - GE Aviation acquired Smiths Aerospace in England enabling GE to grow its presence in Europe producing aircraft systems technologies. This includes Dowty Propeller in Gloucester, composite factory (aero-structures) in Hamble, and an electrical power R&D center in Cheltenham.
2008 - GE BGA team was set up to take proven technology developed in GE’s commercial engine business and apply it into small engines in the business and general aviation (BGA) market space. The Czech Walter M601 was an engine which to GE confirmed that it could do while building domain expertise in the turboprop space. This led to the development of a clean-sheet design, now known as the GE Catalyst.
2013 - GE acquired the Avio Aero in Italy which extended GE's participation and expertise in the areas of mechanical transmission systems, additive processes, low-pressure turbines, combustion technology, and automation systems. Avio Aero sites are located in Turin, Pomigliano d'Arco (Naples), and Brindisi. In this plant, later this year the additive-manufactured components of the GE Catalyst engine will be produced. Avio is also testing the Catalyst FADEC system. www.avioaero.com
2016 - GE finalized the agreement with the Czech government to build its new turboprop headquarters for development, test, engine-production and overhaul in the Czech Republic.
2016 - GE opened a global digital hub in Hungary as a strategic partner of the Hungarian government, continues to invest and develop its industrial footprint in Hungary. With an investment of approximately $30 million US, GE opened one of its six global digital hubs in Budapest. It will be responsible for software development, business processes and application resiliency, building and running infrastructure, and offering access to big data solutions. This includes GE’s Predix software, which the CVUT team (Czech University) was given access to build a turboprop engine health monitoring system. Delivering: Software and data solutions.
2016 - GE purchased controlling shares of the Swedisch Arcam AB. The company is the inventor of electron beam melting machines for metal-based additive manufacturing and is the manufacturer and a producer of advanced metal powders with customers in the aerospace and orthopedic industries. It delivers additive machines as part of GE Additive.
2016 - GE acquired 75 percent stake of the German Concept Laser, an additive machines manufacturer which is collaborating with the GE Additive Technology Center (ATC) in Cincinnati. There, GE engineers are identifying where additive manufacturing can be used to mass-produce sophisticated components for industrial products, including components for jet engines produced by GE Aviation. Today, GE owns around a 95 percent stake in the German company and plans to buy out the remaining shares. Delivering: Additive machines as part of GE Additive.
2017 - GE Additive opened a 2,700-square-foot Customer Experience Center in Munich, Germany which is co-located with GE’s European Technology Center, and allows GE customers to experience every aspect of the additive manufacturing process from design, prototyping to operations. Here engineers have performed the test of the GE Catalyst Axial-Centrifugal Compressor Vehicle (ACCV). Delivering: Additive designs and prototypes.
About the Author
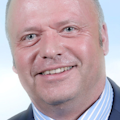
Marino Boric
Marino Boric graduated with a university degree as an aeronautic engineer, and acquired degrees in business development/trade and commerce and in journalism. He is a civil and military pilot and has built experimental aircraft. As a journalist, he specializes in aviation and propulsion and travels worldwide, flight-testing UL, LSA, Experimental, and certified aircraft. He is writing for U.S., European, and Chinese media companies.