What's in a Continental Motors Services Overhaul?
After the press event announcing Continental Motors's investment in its Mobile facilities (see sidebar), I was invited to their nearby Fairhope overhaul facility, located on Sonny Callahan Airport (KCQF), where repairs and overhauls of existing Continental and Lycoming piston aircraft engines are performed, and where they assemble and test the Titan line of Experimental engines.
Though this facility, too, will be upgraded soon (including a new paint center and a workflow revision), I was allowed to photograph nearly everything, and followed the path of an incoming engine through its various stages of inspection, testing, and assembly.
Individuals, fleets, and other shops send engines to Fairhope, some with obvious damage, some with little documentation. After cleaning, the disassembly team performs a visual inspection and then performs nondestructive testing using a traditional array of methods: Magnaflux, Zyglo, and ultrasonic. If a part is undamaged, Tony Campbell (general manager, CMS Fairhope) says, "We'll check every dimension, looking for repairable or out-of-spec parts. We provide the customer with a quote for the repair or overhaul, and once it’s approved, we proceed with the repair or overhaul. However, if the anticipated cost of the engine repair or overhaul is beyond economic sense we will contact the customer." There are several options. "We can offer a core allowance on a new or rebuilt engine from the factory, or swap his engine to a continuing time overhauled, zero time since overhaul. These three options offer a range of value propositions for the customer, including different warranties and content of new parts."
Though owners can and do run their engines beyond recommended TBO (Time Before – or between - Overhaul), common sense should govern the decision. Obvious damage or trauma, such as a prop strike, severe overheating, or a loss of oil, are easy calls. But owners should start regular oil analysis early, always check the used oil filters, monitor oil consumption, and check for blowby or loss of compression. A change in temperature from normal, in normal operation, can also be a sign of immediate or impending trouble.
Engines arrive in Fairhope at all stages of life, from newer units whose propellers have encountered unexpected solid objects, to run-out (and beyond), to engines with low hours, but which have exceeded calendar time limit. (Continental recommends 12-year overhauls, regardless of total time.)
All rebuilds are fitted with new AN hardware (nuts, bolts, washers), as well as new fasteners in critical areas such as connecting rods and counterweight bolts. Bearings, rings – all new, as well. Yes, and new magnetos.
After valves and guides (new or re-used) are fitted up and valve seats are re-cut if necessary, every valve is lapped into its specific position. Then each is checked, typically at 80 psi, for leakage, using the classic soapy water method, effective for over 100 years.
Continental maintains a selection of rotable stock for long lead-time items like crankshafts. Cranks can be and often are reground within factory limits. "Often, since we are using better equipment and methods now, you're going to have a better crank than the one that came new with your engine 20 years ago," Campbell notes. Using rotables decreases build time, sometimes by weeks, since some items are processed only in batches.
Part of the big parent-company upgrade is a full test cell (dyno) for the Fairhope facility, to enable more efficient testing on both overhauls and new Titan engines. Today, overhauled or repaired engines get a one- to two-hour run (new Titan engines are run for three hours) on one of the two instrumented test stands, to ensure they meet all established performance parameters. After that test, which Campbell is strong to note isn't a full break-in, they drain the oil, open and inspect the oil filter, and prepare the engine, inside and out, for shipment.
All this attention and testing take a surprisingly short time. Depending somewhat on the season and particularly on the extent of repair and parts replacement necessary, turnaround – from receipt to shipping -- is typically about three weeks, for the 500 or so engines that get overhauled or repaired in Fairhope every year.
TITAN Engines
Titan Engines serves the Experimental market, affording certified quality and process, plus near-limitless choice of configuration. Thousands of models are possible, varying compression, fuel systems and pumps, propeller controls, starters, injection or carburation, turbocharger(s), ignition options, inverted oil systems, oil filters and coolers, sump design, displacement and configuration, and many minor and cosmetic options, as well.
Sales manager at Titan, James "JB" Ball said that, in the case where the customer is building an airplane and building the perfect engine for it, "It's best to lock in the order and price five to six months before you'll need your engine. Titan engines are highly customized; the parts list is generated at the time of the order." Some customers have an exact configuration already in mind. Some have just a general idea. "The best part of my job is educating customers on the various advantages and disadvantages of each decision – prop, fuel system, ignition, even color -- to match his engine to his future mission." With a current volume of about a hundred new engines a year, Ball smiled and estimated it will take "a lifetime" to build every possible model.
For more information visit continentalmotors.aero.
Continental Invests in New Facility in Mobile
International Holding Corporation has chosen the city of Mobile, AL, for the first step of a three-year global investment plan to expand its manufacturing, customer service, and engineering infrastructure. This first step will build a new manufacturing facility and corporate office located at the Mobile Aeroplex at Brookley and will replace the company’s current 11 building footprint with a single, state-of-the-art facility designed for lean manufacturing and office systems. The new facility will be nearly 225,000 square feet with the majority being dedicated to advanced engine and parts manufacturing. The facility will be populated with new manufacturing equipment and include a special area designated for evaluation of new manufacturing techniques and processes, including additive manufacturing and automation.
“The current operation being spread throughout multiple buildings, drives many challenges and inefficiencies,” said Michael Skolnik, executive vice president Global Operations. “Continental Motors has been a big part of the local Mobile community for over 50 years and is pleased with the community support that allows us to renew our commitment to the region and our great team members for many years to come. The "greenfield" facility will modernize our manufacturing processes into a world class, high productivity, vertically integrated center of manufacturing excellence in the new center of aviation in Mobile, AL,” he said.
Building a new factory is only one part of the plan to transform Continental Motors and the way the company designs, manufactures, certifies, and supports products. CMG will build a new customer and technical service infrastructure and environment that will allow assisting customers through phone, email, and app support, regardless of their location in the world, 24/7/365. Furthermore, Continental Motors will increase its capacity to develop new products and expand China market access with a new engineering and design service center based in China.
"We are pleased today to announce a renewed partnership with all to secure the company’s future for another 100 years. Further, I am pleased to announce our commitment to our global team members and customers with a firm investment to modernize our facilities, products and support.” said Rhett Ross, president and CEO of Continental Motors Group Ltd.
Continental Motors will finish building design and equipment selection in 2017 and will move into its new North American facility in 2019.
About the Author
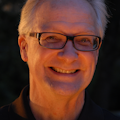
Tim Kern
Tim Kern is an aviation writer, aircraft builder, and private pilot. He is based in Anderson, IN, and can be reached at [email protected].
Tim Kern, CAM, MBA, has written for over 50 aviation publications, and is a consultant for a variety of companies; www.timkern.com.