In last two decades we haven’t seen many new certified aviation engines in the gasoline engines world; in a diesel cycle field it was quite different. Only 10 years ago, the available combustion ignition engines around were not many, but in the last decade their number has steadily and radically grown. New diesel-cycle engines mean not only a different engine ignition principle and engine concept/layout but from the maintenance point of view this means even different changes in the engine maintenance style.
Continental Motors has become a market leader in the diesel engine field offering the highest number of diesel-cycle engines types in the power range from 130 to 300 hp on the market. Altogether, 6,000 plus Continental Diesel engines delivered to date have logged more than 7 million flight hours. Many of these engines and parts CMG manufactures in Germany, so this turned out to be the best place to attend one of CMG Diesel maintenance classes.
The CMG Germany plant is located in St. Egidien, province of Saxony, on the East German border. Today the plant is a leading manufacturer of certified diesel (jet-fuel) piston aircraft engines for general aviation, and is part of the Continental Motors Group (CMG) since July 2013.
The Roots of Continental Diesel Engines
In year 2002 Thielert started marketing diesel engines named “Centurion.” In times of the economic crisis which peaked in 2008, the company was forced to file for insolvency. In the following five years the company was restructured and made lean, continuing the production and improvement of the diesel engines. In July 2013 the purchase of all assets of Thielert Aircraft Engines GmbH was announced by the Chinese-based AVIC International Holding Corporation, the same company that bought Continental Motors Inc. in 2011 from Teledyne and then integrated the general aviation business under the wings of the Continental Motors Group (CMG).
CMG Diesel Cycle Engines
Continental rebranded its diesel engine range in 2014. All the diesel engines were renamed Continental Diesel, abbreviated as CD.
• CD-100 series: The former Centurion 2.0/2.0s engines, in-line four-cylinder, liquid-cooled, and geared engines have become CD-100 series engines with 135 and 155 hp, today’s designation CD-135/155
• CD-200 series: The former TD-300 engine was renamed to CD-230 and CD-245, four-cylinder, opposite, air-oil cooled, turbocharged, and direct-drive engine, with 230 to 245 hp. During AirVenture 2017, the CD-265 was introduced boosting the output to 265 hp and in the CDR (Rotorcraft) version 264 to 287 hp.
• CD-300 series: The newest diesel engine, the V-6, is liquid-cooled, twin turbocharged, and geared 3.0-liter engine with 300-hp output. It gained already EASA certification and production certification. The FAA certification should arrive momentarily.
Continental® Motors has developed the Aviation Technician Advanced Training Program for certified aviation technicians which can be followed for avgas as well as for diesel engines.
The CMG avgas program is held in Mobile, AL, (US) and the diesel program is held in both Mobile, AL, (US) and St. Egidien, Germany.
The main purpose of the CMG seminars is to familiarize and train inspectors, certifying staff and mechanics to perform regular maintenance and diagnoses on Continental Motors Diesel engines. Additionally, special skills can be gained for efficient fault isolation procedures as well as quick and safe diagnosis. This is required to become an authorized Continental Motors Diesel TMG maintenance organization according to the Service Bulletin "TM TAE 000-0003".
Tuition for the course at the Mobile, AL, facility is $950 and for the course at the German facility is €981,75. Training materials and lunches are included in fees. The same courses could be (and are) held in different locations and on different continents, all depending on demand. This year, eight classes are offered from February 4 to December 3 in those two locations. For more information on classes, consult the Continental website: www.continentalmotors.aero/services.
The weekly course (five days) is designed as an initial or refresher course for certified technicians on Continental Motors current production piston engines and covers the following subject areas: engine performance; engine construction; engine fuel systems; fuel injection systems; engine controls; FADEC; starting and ignition systems; induction, exhaust and cooling systems; supercharging/turbocharging; lubricants and fuels; lubrication systems; engine indication systems; powerplant installation; engine monitoring and ground operation; and engine storage and preservation.
CMG Diesel Training
Diesel Training is concentrated on hands on and scenario-based training. Continental wanted, and succeeded, to bring to its trainees a real-life situation training. I went through the course and can testify to this.
The Jet-A training is conducted in an interactive mode, where the trainer encourages or gently pushes, all the students to develop their thought process after absorbing the course material. Interaction between students is important to trainers. The trainer is always challenging his students, making sure that all study subjects are assimilated and memorized while moving along the syllabus.
A part of the training is devoted to hands-on training too, each student goes through the various engine systems and components removal and re-install. This ensures that mechanics are familiar with every aspect of the maintenance. Most participants in the beginning are first faced with theoretical "stuff" and only later, comes the hands-on part. This is the essence of the different approach to maintenance of modern diesel cycle engines which can communicate with the mechanic thanks to their digital heart, the full authority digital engine control (FADEC).
Not the Sound of Silence
Up to now, mechanics have been trained to start maintenance activities by first doing a visual inspection of the engine. This is an excellent way to treat an engine that doesn’t talk. The Continental CD-100 and the CD-300 engine families are different, they "talk" to their caregiver. They not only talk a bit, they constantly communicate with you, or rather with the dual redundant engine control unit or FADEC. Therefore, the first thing that happens in the technical training is to convince the mechanics, which have a long experience with legacy piston engines, that they need to connect their computers with the engine to allow the engine to deliver its report. This is the reason why every trainee attending the course should bring his or her computer/laptop to the course. Once the connection with the engine is established, the mechanic will know quickly and precisely in which troubleshooting should start. This saves time for the mechanic and time and money to the aircraft operator.
I was told that the most difficult thing for trainers is "to convince the trainee/mechanic to leave, not even take out the toolbox or any tool when they initially approach the engine.".
You Are Not Alone
During the weeklong course (CMG called it "seminar" in my case) the process emphasized how much Continental believes in cooperation between the aircraft mechanic and the technical support. This explains why digital downloads from the FADEC system are systemically transferred to Continental. This helps to build a full performance archive of the engine. CMD technical support team members have years of experience and cano share this experience with mechanics when needed.
When in doubt, and this is (not only) in the beginning a frequent case, the mechanic can get immediately in touch with a support engineer and review the logged data together. This eliminates situations where a doubt could exist. This is such an important topic that Continental dedicates two full days to this somehow "digital" topic.
Predictive Maintenance
The FADEC system, which is a dual, redundant, and includes its own battery backup, transmits a full bill of health of the engine. This part of the training was for me a highlight of the course because one of the first readouts of the FADEC storage files gives you the engine health report. Each of two independent FADEC channels delivers its health report, side by side, making it clear to the mechanic what is the real status of the engine in an easy and clear way (color coded and in different alphanumerical levels of engine health). This points immediately to a potential system failure and allows the mechanic to trace down an existing problem. If a component is not operating at its peak performance, but functions within tolerances, the mechanic will know about it, allowing time to order a replacement part, account for shipping lead time, and making sure the part will be available at the next scheduled maintenance interval. Transforming unscheduled maintenance operations into scheduled maintenance is the game changer.
Final Comment
Each class takes five days and ends with an exam. The exam was more difficult than expected and is not a formal joke. Not the easiest, but doable specially if the student actively participates in the training. On the last day, the trainee receives a "Certificate of Recognition" and the "Confirmation" of the practical assessment and the result of examination. Training materials were in my opinion excellent and every student had the opportunity to put his or her hands on the engine. Every question was extensively answered by the trainer, this lasted even hours after the official end of a class.
Was it worth? Yes, it was! The value for me as a pilot is now, I can better understand this engine and I trust it more than prior to the course as I exactly know that this maintenance is light years ahead of the conventional engine maintenance. In the past there was plenty of guessing in troubleshooting an engine, now you know exactly what the problem is and when it may occur - this is predictive maintenance par excellence.
For more information please visit www.continentalmotors.aero.
CMG Diesel Engine Range
- CD-100 Family, CD-135/155
CD-135/155 is a CMG jet-fuel piston engine for general aviation with a takeoff power of 135 and 155 hp. The CD-135/155 is a turbocharged, four-cylinder, in-line, liquid-cooled and geared engine which is EASA certified since August 2006 and FAA certified since October 2006. The predecessor Centurion 1.7 liter is certified by the European Aviation Authorities since May 2002 and FAA certified since October 2003. The weight of all Centurion engines 1.7 and CD-135 is identical so that each 1.7 engine can be replaced by a CD-135. The CD-155 engine is basically the same engine and same weight, 294 pounds (134 kg), but with 155-hp output.
- CD-200 Series
The 230-hp engine was developed in 2009. The engine is air-cooled, direct drive, flat, four-cylinder fitted with an engine-driven mechanical piston fuel injection pump. That engine was certified in 2012 and Continental pursued both OEM and STC conversion markets. This engine was installed in a Cessna 182. A more powerful, modernized version called CD-265 with 265 hp was debuted at AirVenture 2017 in Oshkosh. The rotorcraft version is called CDR-265 and develops 265 hp continous with an allowance for higher power output for a limited period of time. Although being more powerful and more refined, the CD-262 is approximately 8 pounds lighter.
* CD-300 Series
The CD-300 is the newest and most powerful engine in the CMG portfolio. The CD-300 is a 3.0-liter, V-6 style four stroke, liquid-cooled, diesel cycle piston engine with high pressure common rail direct fuel injection, four valves per cylinder, and is twin turbocharged. There is a propeller speed reduction unit (gearbox) with 1:1.66 reduction ratio and electronic/FADEC engine control unit. The engine weighs 547 pounds (265 kg) dry, and is compact thanks to the "V" layout. Power output is stated to be 300 hp for five minutes and 272 hp maximum continuous power at 3,880 rpm (2,340 prop rpm). This engine was recently certified CS-E by the EASA in Europe on (June 20, 2017) and FAA (FAR-33) validation is expected shortly.
The engine was in-flight tested on a modified Cirrus SR-22, and the first customer is the Reiner Stemme Q01 surveillance aircraft. There are many potential aircraft in the market which are suitable for the firewall-forward retrofit kit like: Cessna 206, Beechcraft Bonanza, and Cirrus SR to name a few. By the way, the testbed SR serial cowling was only slightly modified to accommodate this powerplant.
Common characteristics of CD-100 and 300 engines
All CD-100 and CD-300 engines use a full electronic engine control and an integrated propeller management system (FADEC), a true single lever control, and a reduction gearbox. They are liquid cooled, turbocharged (the CD-300 twin turbocharged), and fitted with the inter-cooler(s) for the induction air. Those engines are based on German automotive engines but heavily modified and adapted for aviation use.
The CD-100 engines are FAA, EASA, and CAAC certified and can be used with Jet-A, Jet A-1, diesel, JP-8, and other kerosene based fuels. Compared to conventional aviation gasoline powerplants, and according to CMG, the CD engines reduce the specific fuel consumption by an average of 40 percent. Certified installations are available for the most common general aviation training aircraft like Cessna 172, Piper PA28, Robin DR400, and Diamond DA40, as well as Diamond DA42. The engines are in serial production for general aviation and defense applications.
The FADEC system used in the CD-100 and CD-300 series is a fully redundant 32-bit motor management system for the Continental Diesels. The hard- and the software of the FADEC was completely developed in house respecting the international aviation standards (EASA, FAA). The certified FADEC passed difficult test criteria of the EMV. The ECU regulates the high-pressure valves, the common rail pressure, the turbocharger, and the constant speed propeller's pitch. Furthermore, the FADEC contains some more special functions like the electronic event logging which saves diagnostic data, sensor monitoring, diagnostic interface, the integrated run-up check, or the continuous surveillance of more than 30 internal and external engine parameters.
Conclusion
Over time the Continental Diesel products have grown mature and are seen today as the undisputed leader in the diesel engine market. The TBR (time before replacement) has meanwhile dramatically grown for the CD-100 series to 2,100 hours for the engine, with only a gearbox inspection needed at 1,200 hours. The service intervals have radically increased after the removal of the clutch and with the introduction of second generation gearbox that includes a dual mass flywheel. This has also allowed Continental to announce a 170-hp version of its engine, with an optional specific gearbox allowing for counter rotating installations on light twins. Piper Aircraft has announced a new version of the Seminole using this configuration.
Continental Diesel's CD-100 range has overcome their teething problems with the switch from 1.7- to 2.0-liter displacement in 2006. According to what I have seen and heard in the factory, the CD-300 startup should benefit from the lessons learned. These engines, as with other Continental diesels, are for some fleet operators and owners increasingly interesting engines. They are not only viable alternatives to existing gasoline engines, but are sometimes the only practicable choice, as in many remote areas of the world avgas is not available at all and jet fuel is widely available at a lower cost. In the diesel engine field, Continental Motors has become a diesel giant: a manufacturer with the widest portfolio in the market.
Continental Motors Group in Germany
The German plant also produces engine components and engine applications for defense and automotive industry. Continental Motors Germany manufactures compression ignition piston engines for unmanned and general aviation aircraft. The company possesses aviation certifications as design, production, maintenance, and training organization (JAR 21-J, JAR 21-G, Part-145).
Continental’s German-produced CD-100 and new CD-300 engine families are lightweight, heavy fuel engines in the power-classes from 135 to 350 hp. The engines have proven to be highly suitable powerplants for all aviation applications. Continental Motors Germany also offers tailor-made development services and the manufacturing of engine components for aircraft and automotive industries. Most engine parts are manufactured in-house with most advanced machinery, and all processes and products are subject to strict quality assurance. A data recording and specification system facilitates seamless electronic traceability of all manufactured products. Internally, the best possible measurement techniques and quality management systems (e.g., Six Sigma) are employed.
About the Author
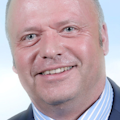
Marino Boric
Marino Boric graduated with a university degree as an aeronautic engineer, and acquired degrees in business development/trade and commerce and in journalism. He is a civil and military pilot and has built experimental aircraft. As a journalist, he specializes in aviation and propulsion and travels worldwide, flight-testing UL, LSA, Experimental, and certified aircraft. He is writing for U.S., European, and Chinese media companies.