When inspecting, installing or repairing windows on an aircraft, there are many aspects to consider. One of these is the type of window and how that defines a technician’s approach. Newer window types include tinted, UV-protected and dimmable windows. For this article, we reached out to industry experts to assess the characteristics defining the upkeep of newer window types in comparison with the more traditional windows with the pull-down shade.
Materials and Combinations
Aircraft windows are manufactured from glass and plastic, and sometimes combinations thereof, affirms Brent Wright, global director of transparencies for the aerospace business at PPG. “For example, flight deck windows for aircraft ranging from piston twins and larger are typically comprised of two or three plies of transparent substrate material (glass, acrylic, polycarbonate, or PPG Opticor) laminated together with a clear interlayer, typically PVB or urethane,” he says. “These substantial cockpit windows are typically electrically heated. Windows with outer plies of plastic, as opposed to glass, might have some type of organic clear coating for abrasion and environmental protection.”
Passenger cabin windows and helicopter windows are typically less complex, according to Wright. “In fact, cabin windows are usually produced from acrylic or PPG Opticor material. They may or may not have clear scratch coatings or other types of films, depending on the aircraft,” he says. “Dimmable windows, instead, may or may not be an integrated part of the structural cabin window. In the case of the 787, the dimmable window resides inboard of the actual cabin window and is integrated into the aircraft’s interior wall panel.”
Most aircraft window openings have two different types of transparencies, observes Research Frontiers. “The outbound transparency is the structural window, which is typically two stretched acrylic panels. The most outboard panel is flush with the fuselage and contacts the outside”, according to Research Frontiers. “The next transparency in a ‘traditional’ aircraft window opening is the panel that the passenger can touch. This goes by various names including ‘scratch pane,’ ‘scratch lens,’ or ‘dust cover.' This is not a structural window and is typically polycarbonate.”
Suspended particle device (SPD) technology can be used in what the industry calls an electronically dimmable window (EDW), observes Research Frontiers. “An SPD EDW uses chemically strengthened glass, and it replaces the polycarbonate scratch lens. An SPD EDW offers the advantages of electronically controlling light, glare and heat being transmitted through the window opening,” says Research Frontiers.
Maintenance Approach
All maintenance performed on an aircraft window is to be performed in accordance with the applicable aircraft maintenance manual (AMM) or component maintenance manual (CMM), points out Wright with PPG’s aerospace division. “Coated windows cannot normally be polished as this will degrade or damage the coating. Dimmable elements may be comprised of very thin glass with a gel inside,” he says. “These elements are often held in place with clips so the removal and installation of the panels must be done with care. Breaking an element is an expensive error.”
Removing and installing dimmable windows requires a certain degree of care with respect to the elements themselves, affirms Wright. “The associated controller, electrical connections and switches require checks beyond a pull-down shade”, he says. “Trouble shooting methods such as voltage checks might be employed. All such methods are covered in the applicable AMM/CMM”.
According to Research Frontiers, an SPD EDW is more robust and durable than a typical scratch lens. “A polycarbonate lens scratches very easily from many sources such as a ring on a finger or a zipper on a coat. Its optical properties also degrade quickly. The result is that a typical scratch lens requires a great deal of maintenance and needs to be replaced often,” says Research Frontiers. “In contrast, an SPD EDW uses thin/lightweight, scratch/impact resistant chemically strengthened glass. It is scratch resistant, and its optical quality does not degrade over time”.
The use of an SPD EDW can eliminate the need for any other type of window shading system, according to Research Frontiers. “A typical commercial aircraft utilizes a thin pull-down shade referred to as a ‘knife-blade’ shade, located inboard of the scratch lens and manually operated by the passenger. The knife-blade shade assembly consists of many parts within the window opening plus the fuselage. Some of these parts move”, says Research Frontiers. “Typical aircraft shades are well known to be highly maintenance-intensive in many areas – cleaning, part replacement, complete assembly replacement, etc.”
SPD EDWs have few components, no moving parts, and a durable substrate, they therefore require less repairs, observes Mike LaPointe, Vice President - Aerospace Products at Research Frontiers. “Every time a shade is moved up-to-down-to-up, takes the name of ‘cycle’. For each of these cycles, the shade moves in a plastic sleeve which is then connected to other window assembly components in the window opening and in the sidewall. In contrast, SPD EDWs have no moving parts and the only manual intervention is the push of a button,” he says.
Upkeep Level
A defining feature of dimmable windows is that they are designed to be nearly maintenance-free. According to PPG, dimmable windows occasionally fail for various reasons such as oxidized gel or an electrical anomaly, in which case the element must be replaced with caution. Electrically dimmable elements are naturally more expensive than manual pull-down shades. “Dimmable windows are certified to work in concert with all other aircraft systems. Electromagnetic interference is considered, and physical fit is by design. While dimmable windows increase the complexity of the window system and interface, it is a different type of maintenance task but not necessarily harder for a trained mechanic or technician,” explains Wright.
According to LaPointe, SPD EDWs are substantially more durable and robust than any traditional shading solution. “The upkeep on pull-down shades, mechanical pleated shades, and electromechanical pleated shades is extensive compared to SPD EDWs. Traditional shades and the many components required to house the shade and move them require frequent cleaning, repairs and replacement, resulting in higher costs,” he says. “SPD EDWs, with very few components, no moving parts and a durable substrate (acrylic or chemically strengthened glass as opposed to plastic or cloth) require a fraction of the upkeep.”
Reduced Carbon Footprint
For an aircraft shading system, SPD EDWs are advantageous in comparison to any other type of EDW, and any type of traditional shade, in addressing the aviation industry’s goal of decreasing the carbon footprint, according to Research Frontiers. “The use of SPD EDWs results in substantially less CO2 emissions by reducing on-ground cooling requirements,” says Research Frontiers. “When an aircraft is parked on the ramp or at the gate, significant solar heat enters through windows, which are known to be a primary culprit of heat in the cabin”.
To provide the necessary cabin cooling, substantial use of on-ground power systems (GPU or APU) is required, with the resultant CO2 emissions, observes Research Frontiers. “Whenever the aircraft is parked, SPD EDWs switch to their darkest, maximum heat-rejecting state. They switch to this state automatically - no manual intervention is required,” says Research Frontiers. “SPD EDWs provide maximum thermal insulation during on-ground conditions (when it is needed most). They provide not only IR (direct heat) radiation blockage, but also block 99.5% of visible light (the light we can see), and this type of light is a major contributor to the cabin becoming uncomfortably warm. Visible light enters the cabin through windows, is absorbed by the cabin interior components, and then is re-radiated into the cabin as IR heat.”
About the Author
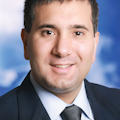
Mario Pierobon
Dr. Mario Pierobon provides solutions in the areas of documentation, training and consulting to organizations operating in safety-sensitive industries. He has conducted a doctoral research project investigating aircraft ground handling safety. He may be reached at [email protected].