A Phase Check of FAA Maintenance Human Factors
Like an aircraft and other heavy equipment, a research and development program needs regular light and periodic heavy maintenance. In the research environment that is accomplished with quarterly and annual program reviews. Like an aircraft inspection our program reviews check for worn parts (ideas) and often identify new situations that present a hazard to our schedules and budgets. That sounds just like aircraft maintenance. This article will help readers and this writer to look at some of the components/systems critical for an efficient and effective FAA maintenance human factors program.
Check the Records/Logbooks
If we look at the age of the FAA Maintenance Human Factors program it would classify as an aging aircraft. It started in 1988. That makes it just about 30 years old. However, the program is not “ready for the desert!” It was most influenced by the FAA Safety Act of 1988. That Act and the robust funding that flowed from Congress coincided with the front-page picture of the convertible Aloha 737. That event drew immediate attention to aging aircraft, aircraft design and maintenance, and to the humans that fly and maintain them. The Act explicitly stated, among other things, that the FAA must establish a program that addresses human performance in maintenance. Like an aircraft in design the first response to the Aviation Safety Act was a committee much like an aircraft’s Maintenance Steering Group (MSG). I was a member of that committee and helped write the The FAA National Plan for Aviation Human Factors, published in 1991.
The National Plan was followed from program inception, when congressional earmarks provided as much as $1.6 million/per for maintenance research, to the late '90s when the Safety Act funding expired. By 2000 Maintenance Human Factors funding had to revert to the normal FAA R&D budget, which was adjusted to about 25 percent of the resources available throughout the '90s. That change, while significant, is a reflection that commercial maintenance organizations, airlines, and consulting companies have assumed much of the activity formerly done by FAA. That is a success story!
Operational History
Like an aircraft historical review, it is good to consider service history. An aircraft operating many daily segments requires different maintenance than one that flies one long segment per day. The nearly 30-year service activity of FAA’s maintenance HF has about three life phases. In the first phase, from 1988 to 2000, the program was controlled by the Washington, D.C. Office of Aviation Medicine, with long-term program continuity and tenure of FAA personnel and their program contractor. The program had extensive senior management support and lots of congressional earmark funding. From 1988 to 2000 FAA, with industry and other national aviation authorities, conducted 21 international conferences on maintenance human factors. The HF conference size ranged from 70 delegates, in 1988, to nearly 1,000 in the year 2000. At the same time FAA issued multiple research grants and contracts to universities and commercial engineering companies. FAA was extremely diligent about publishing all the conference proceedings, reports, and project tools. The materials were first on paper, then on CD ROMs and DVDs, and finally transferred to the web to include all legacy and subsequent documents. The website, www.humanfactorsinfo.com, continues to be supported and is absolutely the largest and No. 1 maintenance human factors information source in the world.
Phase 2 started during the days after 911. The effects of 911 put the human factors program in a bit of “tailspin,” in the early to mid-2000s. A radical reduction in personnel and funding slowed research as well as the annual human factors conference. Industry ability to travel to conferences stopped. About that time, the international partners each embarked on their own HF efforts. Most significant in the time period was the establishment of the European Aviation Administration Agency, with their new human factors regulations.
Phase 3 started about 2005-2006. At that time the management of the program changed, FAA leadership interest increased, and FAA began working with the Civil Aerospace Medical Institute and industry partners to renew the program. A new focus on applied research and on development of tools and processes for industry has led to a prosperous 10-year period. One of the most noteworthy parts of FAA’s maintenance human factors program is the past 10 years of human factors training for all Airworthiness Inspectors. All airworthiness inspectors receive a three-day course in human factors. Many inspectors have repeated the course for recurrent training.
It is worthwhile to list some of the products, see Table 1, that were delivered in the past 10 years of the program.
Table 1: Significant Deliverable in Ten Years
Introduction to FAA Human Factors Video
Maintenance Human Factors Training System
2 Editions of Operators Manual for Human Factors in Maintenance
2nd Edition of The Human Factors Guide for Maintenance and Inspection
Return on Investment Tool Kit
Chief Scientist Workshop Reports
Fatigue Awareness CBT
Fatigue Video (Grounded)
Maintenance and Ramp Line Operations Safety Assessment
FAA MxHF Quarterly Newsletters
Current Observations and Projections
Well, we have looked at the logbooks and considered the operational history. The next step is to look at the current condition and determine the results of the phase check.
In the past couple of years, we have collected a lot of data on two of the largest challenges in maintenance. That includes worker fatigue and “failure to follow procedures.” During 2016-17 we collected fatigue data from about 175 workers across the United States. We have been actively involved in a variety of operations, large and small, from rotary wing, to large and small airplanes. In a second study we spoke to nearly 200 mechanics and managers about the challenges related to using instructions/procedures. We have a renewed understanding of these challenges and are currently working on the final reports. We are seeing that some organizations have found excellent ways to address the documentation challenge. However there is significant variance among organizations. We have also seen organizations that are operating safely, with respect to alert workers. It even appears, initially, the risk associated with worker sleep habits has improved since we conducted a similar study in the year 2000. We are doing our very best to ensure that the final deliverables include clear and actionable procedures that are ready for industry adoption to be delivered in calendar 2017.
With respect to projections, I believe that we are transitioning to a new and fourth phase of the FAA Maintenance Human Factors Program. This fourth phase must remain applied. The products must be understandable and useful for all types of industry users. We must link everything we know about maintenance human factors into evolving safety management systems. We must create tools that will provide explicit step-by-step help with risk-based decision making (RBDM). We must provide support to today’s workers, new and senior. We believe that we can do that in an environment that is rich with data, reported voluntarily, or collected automatically. We must recognize that there are a variety of new technologies at our fingertips. We must work together in a renewed a corporate and regulatory cooperative environment. Human factors challenges and solutions are evolving, not ending. We are convinced that the work related to maintenance human factors shall be an ongoing and important way to support continuing safety.
“Dr. Bill" Johnson has been associated with the FAA’s Maintenance Human Factors Program since its inception in the late '80s. He has held a Pilot certificate for over 50 years and is approaching 50 years since receiving his A&P certificate. He is the FAA Chief Scientific and Technical Advisor for Human Factors in Aircraft Maintenance Systems.
About the Author
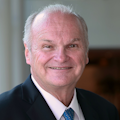
Dr. Bill Johnson
Chief Scientific and Technical Advisor Human Factors in Aviation Maintenance, FAA
““Dr. Bill” Johnson is a familiar name and face to many industry and government aviation audiences. Johnson has been an aviator for over 50 years. He is a pilot, mechanic, scientist/engineer, college professor, and senior executive during his career. That includes 16+ years as the FAA Chief Scientific and Technical Advisor for Human Factors.
Dr. Bill has delivered more than 400 Human Factors speeches and classes in over 50 countries. He has 500 + publications, videos, and other media that serve as the basis for human factors training throughout the world.
Recent significant awards include: The FAA “Charles E. Taylor Master Mechanic” (2020); The Flight Safety Foundation - Airbus “Human Factors in Aviation Safety Award” (2018), and the International Federation of Airworthiness “Sir Francis Whittle Award” (2017).
Starting in 2021 Johnson formed Drbillj.com LLC. In this new venture he continues to bring decades of human factors experience to aviators, worldwide.