“Airsides are very busy environments where lots of various ground support equipment is operating often under time pressure to service aircrafts on time,” says Altay Fellah, INFORM GmbH’s, vice president of business development for its aviation division. “In such a busy and time critical operational environment, there is always a safety risk.”
He recognizes ground support equipment (GSE) pieces are high-value assets, and together form one of the most important parts of ground service operations.
“Incidents can be very costly to any service provider and other parties impacted by them,” Fellah adds.
He says safety concerns range from operating over the speed limit, to breach of safety from entering prohibited areas, unqualified equipment operators and malfunctioning equipment.
Kurt Ladd, Estex Manufacturing Company’s national sales manager – aviation products, agrees about the high-value of equipment assets, and says his company’s story is a bit different. Estex’s textile products are built to withstand weather and prevent foreign objects from landing on the airfield.
“Anything left out on the ramp at an unintentional spot can become FOD (foreign object debris),” he says. “A lot of people have some really creative ideas on ways to help improve safety while saving their company money.”
Justin Akinley, director of business development for NMC-Wollard, adds another level to the safety story and explains that the person in the cargo hold is very “out of sight, out of mind” but this is also a place a human body can’t express itself naturally.
“You often have to be either on your knees, or bent over, moving back and forth,” he says.
The airlines want to minimize damage to bags, but he adds they also must look to prevent injuries due to improper ergonomics for workers.
“This is a hustle job, long hours, and you run down on energy, run down on focus, and people get injured,” Akinley notes.
German manufacturer Mototok International focuses solely on the development and production of purely electrical, wireless remote-controlled aircraft tugs.
“With our machines, many MROs and also nearly all aircraft manufacturers move aircrafts of all sizes precisely or automatically guide them in and out of hangars and production lines,” says Thilo Wiers-Keiser, head of sales and marketing for Mototok.
Regardless of their product angle, these GSE experts agree safety comes first and are proud to offer innovative tools to keep ground service providers out of harm’s way.
Safely Position Equipment
INFORM’s GroundStar flagship software solution helps service providers optimize equipment fleet utilization, as well as prevent/minimize equipment incidents, says Fellah.
He explains that ground support operators are able to locate the position of both motorized and non-motorized equipment, which is visualized on an electronic airport map. The software generates warnings and alerts when the equipment is being operated over the speed limit or entering prohibited geographical areas around the airport.
“At large airports, locating where the required equipment is can be a challenge,” Fellah adds.
Because of this software solution, fleets are reducing in size, he says, and showing substantial savings in operational costs. The equipment is also being utilized more efficiently and safely.
“Immediate transparency on the location of the equipment helps to find out if it is close to where it’s needed, and suitable for the task,” Fellah explains.
The software implements incident prevention measures through access control, as well as monitoring the operative state of the equipment. Fellah says INFORM’s software watches oil level, water temperature and battery level of GSE, preventing defect incidents and reducing maintenance costs.
“Thanks to accurate telematics data, GS GroundFleet is a way of the fleet’s maintenance schedule,” he says. “Operators can plan ahead and keep operations running smoothly as equipment is taken care of.”
Safely Handle Cargo
Akinley says NMC-Wollard provides a variety of solutions for helping those working in the cargo hold like a mobile belt loader with a roller conveyor extender.
“This is a really efficient way to get a bag from the ground to the belt loader and then to the point of loading,” he says. “That takes a tremendous amount of stress off human bodies.”
The variables which can create a challenging situation are numerous, Akinley says. It depends on the airline and their cargo hold areas, but he says a 50-pound suitcase is pretty large to move repeatedly and solely by twisting the body and lifting into the designated spot.
“Nobody sees that,” he continues. “They only see the baggage cart while looking out the window.”
The belt loaders also minimize scratches and potential damage to the aircraft, though he says the greatest benefits are the stress minimization and increased safety to the baggage loaders.
“I’m a strength and conditioning coach, but they don’t have a coach in there telling them to not round their shoulders or that they lost their lumbar spine and to lift with their legs,” he adds.
Akinley says other items NMC-Wollard provides are passenger stairs and tractors. Regardless of the model, size or abilities, he wants ground handling companies to know what they need and why. This is Safety 101 for Akinley. The company builds special safety and protection points into the equipment as a standard, and then he says each purchase quote is line-itemed to suggest others.
“It’s not the most exciting thing to talk about,” he acknowledges. “It’s just having the conscious thought of what it’s like for the person on the ramp.”
He offers the simple example of gapping the gas pedal to make room for winter boots, so drivers don’t slip off the brake.
“I think if you boil everything down to a simple element, it’s that there can be a breakdown in communication from the person saying they need a tool to the person buying it and the company building it,” he says. “We’re all interpreting that request very differently and people don’t necessarily know what they should be selecting.”
To solve that, he says working with safety professionals is key, and learning what the various options are in equipment safety features.
Safety in Textiles
Estex provides loading bridge and baggage cart curtains, ramp bags and various FOD-related supplies for the ramp, including cargo container doors, PCA hoses and more.
Ladd says the Estex product line is all durable cloth-based and sewn together, and many times, bought in a reactionary moment of a ground service provider’s career.
“If an incident on the ramp caused aircraft damage or injured ramp personnel, then the thought turns to, ‘What can we do for corrective action to prevent this from happening in the future?’” he explains.
That’s where Estex excels, Ladd says, and can customize safety products for the customer’s need, even to a certain color, pockets and dimensions. The company’s original ramp bag was simple with pockets used to house headsets, wands and documents. Then, Ladd explains, a customer wanted it slightly different with magnets on the bottom to affix to a pushback, eliminating the chance of it blowing over.
He has seen more of this customization in recent years and says Estex is happy it can provide these unique safety solutions. A ground power unit (GPU) towbar sock reminds individuals before they move the GPU to disengage any wiring from the aircraft. Reflective products have also been increasing on the ramp to prevent incidents, increasing safety.
Ladd says there may not be a lot of technology in what Estex does, apart from the advancements in durable and weather-withstanding material, but the impact on safety is just as vital and important.
“The joy is taking an idea from somebody and bringing it to life, working with them, and coming up with something that works well for the individual, but also the airlines and service providers,” he concludes.
Safely Move Aircraft
Mototok’s Wiers-Keiser says automated movement of aircrafts is helping avoid human error and keeping the ground handling community safer at London’s Heathrow Airport (LHR), but also at many MRO and FBO hangars and military aircraft carriers.
He says pushback operations are safe and easy for single-man operation thanks to the remote-control feature of the Mototok products.
“For example, at London Heathrow, there are 25 machines and they perform more than 1,000 pushbacks per week,” Wiers-Keiser says.
He notes the tugs are emission free and they can be operated with a zero-degree turn inside the hangar and docked in a matter or seconds. Mototok units also optimize limited space up to 40 percent and are not weather dependent to operate effectively.
Wiers-Keiser says that the Mototok machines are like robots, that acceleration and deceleration isn’t depending on the feel of the operators.
“It’s programmed according to the needs of the pushed/moved aircraft type,” he says. “They drive very, very slow (max 6 km/hour) and precisely if needed.”
Another safety aspect is that the operator does not need to stay near the aircraft’s nosegear for operation.
“He can walk and stay where he wants to get the best overview,” Wiers-Keiser adds, and says that the remote control works at a distance of up to 30 meters.
He and his safety-conscious peers in the ground support industry agree that this is an important topic to continue refreshing for all providers, and a goal for their companies to continue meeting.
NMC-Wollard’s Akinley says this mindset mitigates unwanted litigation, and erring on the side of caution saves a ton of money in the long run.
“A company that embraces safety, has a culture of embracing safety from the top down, builds a safer product,” says Akinley.
About the Author
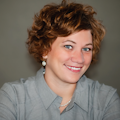
Jen Bradley
Jen Bradley, owner of Bradley Bylines, is an aviation writer based in East Troy, WI. She may be reached via her website at www.bradleybylines.com.