Runway Grooving: A Good Solution Takes Off
Grooving airport runways is common practice in the United States. The U.S. Federal Aviation Administration (FAA) recommends grooving for all airport projects funded with federal grants, which represents most projects. Similarly, U.S. Department of Defense facilities are increasingly specifying new, reconstructed or resurfaced runways to be grooved. In Canada, however, there has been limited use of runway grooving. In recent years this situation has been changing, due to the overwhelming evidence that grooving is a proven strategy for reducing the risk of hydroplaning and improving runway safety.
There are three basic types of airplane hydroplaning and their underlying physical conditions as follows:
- Dynamic hydroplaning occurs at relatively high speeds when there is a film of water on the runway that is at least 1/10-inch deep. The water layer resists displacement when the water pressure equals the weight of the airplane; the tire lifts off the runway surface and stops rotating. The airplane loses braking and directional control.
- Reverted rubber (steam) hydroplaning occurs during heavy braking that results in a prolonged locked-wheel skid. This can happen even if there is only a thin film of water on the runway. The skidding tire generates enough heat to cause the contact patch of rubber to revert to its original uncured state. This reverted rubber acts as a seal between the tire and the runway, trapping water. The water then heats and is converted to steam, exerting force and lifting the tire off the runway. When the airplane eventually slows and tires reconnect with the runway surface, the airplane skids. Dynamic hydroplaning, which often causes the pilot to lock brakes, can lead to reverted rubber hydroplaning.
- Viscous hydroplaning is caused by the viscosity of water and it can happen when there is only a thin film (no more than one thousandth of an inch) on the runway. In viscous hydroplaning, the tire cannot penetrate the fluid and the tire rolls on top of the film. This can occur at a much lower speed than dynamic hydroplaning, and is a problem on smooth surfaces such as a touchdown area coated with the accumulated rubber of past landings.
In any of these situations, the friction coefficient becomes almost negligible, and wheel braking and steering are ineffective. Therefore, it is desirable to prevent the problem before it begins by managing the surface texture of the runway. Grooving the runway provides channels for water to escape, helping eliminate standing water and restoring tire friction coefficients on wet pavement. The grooves are cut transversely to the direction of airplane landing and are usually continuous to dry pavement lines for the entire length of the runway. Most specifications call for grooves that are 6 millimeters deep and 6 millimeters wide, spaced 38 millimeters center-to-center, although different grooving configurations have been explored by the FAA in the past.
Grooving Increases in Canada
Although runway grooving is not required in Canada, a 2013 Transport Canada Advisory Circular publicized the safety benefits of grooving and disseminated technical information on the process. Within the same timeframe, several airports conducted grooving as a result of aircraft overruns due to wet pavement.
Port Hardy, British Columbia, was initially grooved in 1970 and again in 2012, making it the first airport in Canada to be entirely grooved. Norman Wells airport in the Northwest Territories was grooved in 2011. The grooved area at Norman Wells measured 67,633 square yards and was performed by Safety Grooving & Grinding of Napoleon, Ohio, now a part of The Penhall Company of Irving, Texas.
Ottawa International airport grooved its first runway – measuring 157,000 square yards – in 2013 and its second – measuring 192,000 square yards – in 2015.
“In Ottawa, because it was the first time a large Canadian International airport had grooved its runways, there was skepticism and a concern that snow and sand would settle into the grooves,” said Philip Zuzelo, president, Cardinal/International Grooving and Grinding LLC. “But this fear proved unfounded. Maintenance crews report that clearing the runways is just as easy on grooved runways as it is on ungrooved ones.”
Following on the success of the Ottawa grooving, in 2017 the Billy Bishop Toronto City Airport chose to groove 57,000 square yards of runway.
More recently, a runway grooving project was completed at 14 Wing Greenwood, Canada’s largest Royal Canadian Air Force (RCAF) base on the East Coast, in response to an incident in which an aircraft slid from a runway at 80 knots during a high-speed abort procedure on takeoff. Investigators noted evidence of both dynamic and reverted rubber hydroplaning: the aircraft tire showed a clear patch of reverted rubber and the runway itself showed a strip of pavement where dirt had been "cleaned" off the pavement due to steam. They determined that hydroplaning was one of several factors that contributed to the incident.
DAES Aerodrome Engineering then examined several potential factors to identify the cause of the hydroplane. They conducted a topographic survey of the runway surface, but determined the slopes were correct and there were no areas of obvious ponding, which suggested that surface grading was not an issue. This enabled them to rule out the need for new overlay to correct for grade. Recent runway friction testing results confirmed that there was an adequate coefficient of friction and recent pavement condition surveys had indicated that runway pavements were in good condition. Knowing that runway grooving was frequently practiced outside of Canada, grooving was investigated as a potential solution for 14 Wing Greenwood.
“We reviewed FAA research from the United States, talked to officials at the Ottawa airport and looked at work performed at U.S. air bases, where grooving is mandated,” said Wayne Watson, chief aerodrome engineer, architecture and engineering services Department of National Defence/Government of Canada.
“Although there are a number of different construction techniques that improve skid resistance and reduce the risk of hydroplaning, it was determined that grooving was the best option,” said Myron Thiessen, airfield pavements and standards officer, architecture and engineering services, Department of National Defence/Government of Canada.
John Roberts, executive director of the International Grooving & Grinding Association, emphasizes the safety advantages of runway grooving projects. “When a pilot is landing on a wet runway and steps on the brakes, there is much more even breaking with a grooved runway,” Roberts explained. “Grooving minimizes the potential for hydroplaning and delivers the best possible overall ground handling and stopping characteristics that today’s state-of-the-art technology can provide.”
“One challenge presented by the runway at 14 Wing Greenwood was that the asphalt pavement was 17 years old. Typically, grooving is performed on runways within one year after they are completed or resurfaced,” said Thiessen.
To evaluate the durability of the older pavement, a series of borehole samples were collected. Prior to being tested with an Asphalt Pavement Analyzer (APA), 6- x 6-millimeter grooves were cut into the core samples. The APA results showed that the cores with grooves performed the same as the ones without grooves, confirming that that the existing pavement was structurally sound and would not only withstand grooving, but would provide continued service life.
So far, the performance of the grooved pavement has been encouraging: runway friction measurements taken during winter operations were generally higher than in previous winters. Summer friction testing will be performed in 2019 to determine an annual baseline. Initial feedback from users has been very positive and it’s been observed that the runway now dries more quickly after rain or snow. Furthermore, maintenance and snow clearing has been comparable to that of the previously un-grooved runway.
Grooving of 134,000 square meters of runway began on Oct. 30, 2017 and was completed Nov. 8, 2017. The total project cost was 862,000 Canadian dollars. The general contractor for the work was Mid Valley Construction and the grooving subcontractor was Penhall Company of Abingdon, Md. At the project’s outset, a trial section of the pavement was grooved. The trial confirmed the equipment could construct the grooves to specification without damaging the runway surface. The work was conducted with two crews and two machines working 24 hours a day, seven days a week on a closed runway.
The runway is the first in the RCAF to be completely grooved, but if the performance of the 14 Wing Greenwood runway continues to be favorable, additional runways across the RCAF will be considered as candidates for grooving, according to Watson. Taken together with the successes reported at commercial Canadian airports, the trend for airport grooving is likely to continue across the country.
Kristin Dispenza is an Account Manager with Advancing Organizational Excellence and develops trends articles, case studies and other PR materials. She received a Bachelor of Science degree from The Ohio State University College of Engineering/School of Architecture and has more than 20 years of writing and editorial experience. She can be reached at [email protected].
About the Author
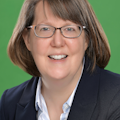
Kristin Dispenza
Account Manager
Kristin Dispenza has been a member of the AOE team since 2013, developing trends articles, case studies and other PR materials. She received a Bachelor of Science degree from The Ohio State University College of Engineering/School of Architecture and has more than 25 years of writing and editorial experience.