Best Practices for Winter Weather Gravel Runway Maintenance
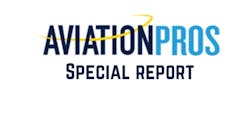
Q. How are gravel runways susceptible to the freeze/thaw cycle? What conditions make it more susceptible?
Water is the primary culprit. Water creates multiple adverse effects for gravel runways and is a main factor behind gravel runway deterioration and unsafe conditions. Improper surface drainage, moisture infiltration, and freeze/thaw cycles result in numerous issues for gravel runways.
These issues can include a reduction of shear and bearing strength, expansion and contraction damage, stripping of stabilizers, and erosion and deterioration of the surface. Removal of unbound fines, reduction in surface life, destabilization of the designed base course, increased maintenance activities, seasonal soft spots, deformation, rutting, potholes, and water pooling also can occur.
Q. What kinds of stabilization products are available on the market for runway usage? How are they different than other applications? What are the key differences between them?
In the world of approved design and construction of unpaved gravel runways, the only criterion that is defined and approved is a structure that consists of a sub-base, a base, and a workhorse of gravel, all to varied specified depths and configurations. There is no reference in any design criteria issued by governmental agencies for using a stabilization agent in constructing unpaved gravel runways. Therein lies the challenge, because without a stabilization agent, the surface, base, and sub-base will all deteriorate after initial construction.
The only comparison in the Norwegian study was against reduced sugar, but it is only a dust palliative, not a stabilization product. Results from the study show that reduced sugar worked initially as a stabilization product until extreme conditions (freeze/thaw cycle and exposure to high amounts of water) show it deteriorated back to the same properties as the untreated aggregate. In other words, the freeze/thaw cycle and presence of moisture made the reduced sugar product useless because it broke down and washed away. Other dust palliatives include base oils, synthetic oils, and even Midwest has several products that are dust palliatives, but they would NOT recommend for use in a gravel runway installation since stabilization is the key construction point in the discussion.
Midwest’s EK 35 is specifically designed for the freeze/thaw cycle and the harsh winter conditions. According to the study, SECUR 35/EK35 was the only gravel runway product that worked as a stabilization product and became stronger with time. A quote from the study indicated SECUR 35/EK35 was the only one in which “a significant stabilization effect is found both before and after the exposure to the freezing-thawing actions.”
Q. How can runway conditions differ when using different stabilization products? What gains/issues can be addressed with the proper product in place? Or what issue can occur with the improper product usage?
The main enhancement of a stabilization product is the efficacy, performance, and strength of the runway surface. A dust palliative only provides a temporary improvement in the surface, but with the first freeze/thaw or harsh weather conditions, the surface begins to deteriorate. The moment the surface deteriorates, FOD is created. It only takes one piece of gravel to damage an engine, costing potentially upwards of millions of dollars to repair. And when the conditions are dry, dust and debris can cause takeoff and landing visibility issues, engine performance problems, airplane surface/window damage, and more. When the proper product is in place and a proper stabilization system has been used and properly maintained, the surface will not deteriorate, thereby preventing dust, debris, and FOD from developing into a problem.
Q. When should an airport consider treating a runway with stabilization product to ensure the highest return on usage? Should a regular schedule be set or only as needed?
All unpaved runways (gravel or dirt) need to be treated with a stabilization product because of the risk of damage to an aircraft resulting from foreign object debris (FOD). FOD can damage tires; strike the fuselage, propellors or other components; or be ingested into the engine. There are also safety issues when landing or taking off if the surface of the unpaved runway becomes unstable or dust/debris is significant.
FOD in the form of loose gravel on the runway surface is part and parcel of untreated gravel runways. One of the most common reasons for FOD is the breakdown of the runway surface, often caused by the freeze/thaw cycle.
When the SECUR Stabilization System is used, maintenance is reduced and maintenance applications reduce the interruption of the runway schedule.
Q. What are the different application methods and when should you consider each of them?
This is the challenge at hand. None of the other methods indicated above stand up to the freeze/thaw cycle because water is required with every other product, as indicated by the Norwegian study. Unless the runway is created using a permanent method such as concrete, unpaved runways only have one option if they want to avoid the above problems related to surface degradation and ultimately, instability. When installed, SECUR 35/EK35 creates a bound runway surface that results in improved performance, longevity, safety, and stabilization. A SECUR 35/EK35-stabilized runway provides year-round consistent accessibility by eliminating seasonal soft spots, harmful moisture infiltration, and freeze/thaw damage.
A blended (SECUR Stabilization System) installation can permanently result in light maintenance applications and a decrease in runway lifecycle costs up to 27 percent — that’s more than $1.5 million in savings over 20 years.
Q. When purchasing stabilization products, what questions should an airport be asking to ensure they’re picking the right product for their runway? Is the product a dust palliative or stabilization product? To further this point, is the product applied to the sub-base, base, and surface, or only the surface (the latter indicates it’s only a dust palliative)?
Does the product contain water or require water to be applied (when in the form a concentrate)?
Will this product withstand the freeze/thaw cycle (if it contains water, it can’t)?
Is this product environmentally safe?
Will the product leach into the surrounding vegetation and water sources after application?
What are the maintenance costs and frequency of post-installation maintenance (which interrupts scheduled air traffic)?
What’s is the burden of the maintenance when it must be completed (# of days of interruption to the runway(s))?
Are there any studies that prove the effectiveness of the product as a stabilization installation versus simply a dust palliative?