Ensuring Smooth Delivery of Passenger Boarding Bridges
Passenger Boarding Bridges (PBBs) are a persistent topic in the industry. Whether new ones need to be built to satisfy growing demands for additional gates, or old ones need to be replaced due to age and maintenance issues, these structures are forcing owners to make important decisions.
If a passenger boarding bridge needs to be replaced, there are usually two solutions: demolish and rebuild, or refurbish. In either case, the airport will need the assistance of a designer with a specialized and diverse set of skills, including expertise in aircraft gate planning as well as civil, structural, architectural, electrical, communication and mechanical design capabilities.
Whether the PBBs are for new gates or for replacing existing bridges, it is essential to work with the airport/client to develop a comprehensive design package that defines the features, operations, equipment and finishes to meets the needs of the owner, operator, and users. Designing a truly successful and operational efficient aircraft gate requires a holistic approach.
Keys to the smooth replacement of a PBB include:
Phasing. Because it is important to keep airport activity fully operational and as unaffected as possible, PBB construction should be phased. It is critical to coordinate with seasonal flight schedules limiting disruptions while maximizing the available gates for construction.
Cost Benefit: Performing a cost-benefit analysis is an excellent way to determine whether it is more beneficial to refurbish PBB components or replace the entire unit. This means having clear documentation of the infrastructure and condition that is existing, and assessing any existing deficiencies and verifying with client the scope of the project
Flexibility. Being flexible with the changing needs of an airport and its aging infrastructure is crucial. For example, if a designer is in the planning process on one PBB and then all of a sudden another one breaks down, they have to be able to seamlessly shift their design focus to address the critical issue. Working with the diverse set of stakeholders also requires flexibility in working with evolving design criteria.
Standardization. Most airports will keep the PBB procurement open-ended allowing the two main providers, Thyssen and JBT, to bid on the project. Having a standardized bridge and equipment agreed upon is cost efficient and easier to maintain. There are advantages to maintaining PBBs from one manufacturer as there are efficiencies in maintenance, spare parts, training and operation. Airports have recognized this and started to sole source when looking to replace existing PBBs.
Foundations. Can the existing bridge foundation be saved to avoid the cost of building a new one? Preserving as much of the existing foundation as possible saves money and reduces construction and gate closure duration.
- When replacing a bridge, the engineer must ensure the existing foundation meets new code criteria or retrofit it.
· Construction varies, but typically an existing PBB can be swapped out in about 7-10 days of gate closures with foundation modifications typically being able to occur independently. This time frame increases to about four weeks if new foundations are required
Typically, it is in the airport’s interest to try and modify the foundations to limit gate closures. But there are certain instances where there is no way around shutting down the gate. Sometimes there are utilities in the ground all around the bridges precluding amendments to the existing foundation, so it is important to try and identify these issues as early as possible to ensure they are considered during programming and design.
When planning a new PBB foundation or modifying an existing one, even if you have great as-built and utility base maps, it’s still highly advisable to do utility locates and strategically pothole when needed to verify there are no conflicts. With gate time at a premium, making sure you don’t encounter unexpected obstructions that could delay construction and gate re-opening is well worth the upfront survey cost.
Challenges: One of the biggest challenges in deciding what to do with a PBB is making sure it has the necessary infrastructure to meet current and future technology needs. Many times, there are future planned projects to bring new technologies to the aircraft and ramp, but those projects are still in planning phases.
It’s important to work closely with those projects to understand the infrastructure needs, so adequate cabling or conduit can be provided. It’s a lot harder to run cabling to the end of the PBB once it’s built and installed.
Sustainability. If refurbishing the PBB, then owners can “recycle” it and extend its useful life by 15 years or more. This may be appealing to airports that include sustainability among their core principles.
Aesthetics and passenger experience. Will a refurbished passenger loading bridge fit with new buildings or will it detract from the architecture? Will new or refurbished passenger loading bridges match existing ones, so customers have a similar experience each time they fly, regardless of airline? Sometimes, simply installing new flooring, wall boards, and lighting to coordinate aesthetics between the terminal and the bridge is enough to drastically improve customer experience.
In conclusion, both installing new bridges or undertaking refurbishment will create a more pleasant, uniform passenger experience, increased efficiencies and reliability, as well as allow for greater flexibility in the future.
Ryan Carson, PE, is a senior project engineer in HNTB’s Seattle office. He has ten years of experience in civil engineering design, including landside and airfield pavement marking and signage, development of taxiway and taxilane geometry, vehicle and aircraft maneuvering, and jet blast analysis. Carson’s project experience includes the replacement of nearly 30 passenger loading bridges at Seattle-Tacoma International Airport as well as gate layout and aircraft movement planning work at Los Angeles International Airport, Portland International Airport, Salt Lake City International Airport, San Diego International Airport, and Van Nuys Airport.
James Long, PE, is an aviation project manager and associate vice president at HNTB. For 10 years, he has been providing professional civil engineering services for general, commercial, and military airports throughout the west. In his career, he has served as the primary design engineer for gate layouts and passenger loading bridges on multiple projects, including the Tom Bradley International Terminal and the United Airlines LAX Terminal Redevelopment programs. His expertise includes complex construction phasing plans, aircraft gating layouts, and extensive stakeholder coordination.
About the Author
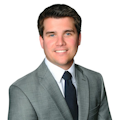
James Long
Project Manager, Aviation Infrastructure
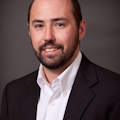
Ryan Carson
Senior Project Engineer
Ryan Carson, PE, ([email protected]) is a senior project engineer in HNTB’s Seattle office. He has 15 years of experience in civil engineering design, including landside and airfield pavement marking and signage, development of taxiway and taxi lane geometry, vehicle and aircraft maneuvering, and jet blast analysis. Carson’s project experience includes the replacement of nearly 30 passenger loading bridges at Seattle-Tacoma International Airport as well as gate layout and aircraft movement planning work at Los Angeles International Airport, Portland International Airport, Salt Lake City International Airport, San Diego International Airport, and Van Nuys Airport.