Swinerton’s National Aviation Lead Carrie Shaeffer Looks to the Future of Aviation
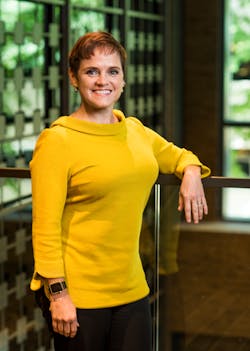
As Swinerton’s National Aviation Lead, Carrie Shaeffer is one of the leaders in modernizing North America's aviation infrastructure. The company is involved with more than $400 million in airport improvement projects and modernization programs annually at airports of all sizes.
Shaeffer sat for an interview with Airport Business to share some of the latest trends in the market and how she sees airports tackling some of their biggest needs while wading through the outside challenges impacting completion of improvement programs.
Airport Business: What are the essential elements of a major modernization project for a commercial airport outside of the passenger experience?
Carrie Shaeffer: Baggage handling system modernization is an issue in many of our airports today. We’re seeing all our clients working to increase their capacity and their efficiency in provisioning flights, which requires facilities and utilities. They want to turn their planes quickly. They want people to have on time flight departures and arrivals and they want to have their snacks while they're on the plane as well.
AB: What is the major trend you’re seeing for airports updating their baggage handling systems?
CS: Baggage handling is so interesting because it's such a maze at so many airports. They started as a small airport and then they added on and added on and added on and on. What we see airports doing is attempting to install as much new flow as they can. They can't just gut everything and start over.
For example, they’re taking sections such as the check baggage inspection stations for the TSA, looking for a place in their airport to install a new CIBS, which are faster, more ergonomically designed for the TSA agents and have better technology for scanning the bags. Everything is improved in that flow. We just finished one last year at Palm Springs Airport.
AB: What is an area of airport improvement that needs to be addressed more widely?
CS: Something I learned early in my aviation construction career is that it's all about the bathrooms. A smart person once told me it's the last thing you do before you get on a plane is the first thing you do when you get off a plane. It's the whole impression of an airport. Pre-pandemic, there were lots of airports looking to increase and really modernize restrooms. They were trying to go touchless with everything and put modern systems inside the restrooms. That fell by the wayside when some bigger, more critical issues needed to be addressed as we started coming back from the pandemic. But we’re near 2019 passenger enplanements, so look for bathroom refreshes to start again soon.
AB: Airport improvement projects often get looked at as solving one or two issues at an airport. How can we address these updates in a more holistic way regarding all operations within the airport campus?
CS: From the builder's point of view is it's not just the project, it's how we solve the project. Swinerton has worked at 45 commercial airports, five government ones. We’ve learned in our own process how we solve these things that could be intrusive to airport operations. We plan and phase and communicate what we're going to do in a manner that minimizes impact. We look at minimizing impact to airport operations first, to security issues second. Then we look at how we’re phasing in our temporary measures while being as invisible as possible to the passenger.
At Long Beach Airport, we carefully planned pre-pandemic to make sure we didn’t impact those operations. We were adding on, we were renovating the historic building, we were adding a new ticketing building, adding a whole new baggage handling system, and expanding the baggage pickup on the back end.
We had this phasing plan that everybody was happy with and then when the passengers left, we completely re-phased the project to address the priorities of the airport. We completely changed the phasing to address a careful cashflow management the airport had in mind. And in the end, we kept people at work all the way through the pandemic. We delivered it.
AB: Do we have to build our way out of the security checkpoint struggles we see or is it a technology solution?
CS: It’s both technology and actual physical expansion and modernization. I'm a frequent traveler. I was already very comfortable with all the expediting measures that are possible and all the technology. I think that more passengers are more comfortable with the technology, therefore those options are going to expand.
We see facial recognition being plugged into the conventional TSA checkpoint. As we move forward, those areas are going to be redesigned to be primarily touchless and self-service so that most people can just flow right through. I think technology is going to help improve that process. My personal dream is to be able to not stop stop moving from when I get to the airport to when I sit in my seat. But in the meantime, there’s a capacity issue. Funding is being routed toward increasing the number of security lines that are available for people to go through.
AB: What were some of the crucial steps Swinerton needed to take to ensure the new CIBUS station at Long Beach was creating a more efficient space for the airport and security officials?
CS: The virtual planning beforehand, even before fabrication was important to make sure all systems are going to be constructed pre-everything. Prefab as much as possible so when the project is delivered, there’s going to be as few conflicts as possible. It also included having some backup plans ready just in case. That included having potential porter at standby just in case you need it.
It takes a few layers of insurance. The airport itself was interested in what those contingency plans were before we started taking things offline and then making sure that they could contribute to the contingency plans if needed.
In the end, it’s still mostly about communication. Signage and written communication and graphic communication with people is very effective in helping them understand where to go next when they're in an airport and when the blocks are moving around in the middle of the night, and they come back to the airport one week to the next.
AB: With more material options available on the market, how can airports think about building an overall better environment for travelers and staff while also finding efficiencies in facility maintenance?
CS: We’re looking at hold room and gate modernization for several airports, including Denver and United as combined clients. We’re Americans. We want to be right by our gate, but travelers want more personal space.
It’s all about providing options for passengers, not just the same rows and rows of seats. I think we as builders can contribute to that by encouraging the use of and giving them examples of prefabrication. There are a lot of spaces that are repetitive in an airport and proposing solutions such as large modular pieces and do component construction so that bigger pieces, more preassembled, show up at the airport before you even start to impact operations. At the Portland airport’s TCORE project, we’re providing the cross laminated timber and mass timber component of some massive prefab cassettes.
AB: What has the stress test from the travel crush in 2022 taught us about the weaknesses we have in airport infrastructure in North America?
CS: The first thing I would point to is in the modernization. When we say modernization in our industry, we often think about getting a bigger building and adding more gates. But the special systems within the airport, which provide passengers with information is even more important. Having more gate information system, such as FIDS and GIDS and flight information was already improving. I see our airports even more focused on that piece of it.
Another trend is more operational readiness training where airports and airlines are going to an even deeper effort to make sure everything works 100 percent. I'm not talking about just the air conditioning coming on, I'm talking about these communication systems and emergency systems are fully working so people can be confident in an airport.
AB: We’re almost a year into the Bipartisan Infrastructure Law becoming law. How have you seen this impacting the industry as a builder?
CS: Now that we see BIL money is starting to flow, I've noticed airports are looking at their needs lists and now taking a look at an additional funding source and reprioritizing some projects because they meet the criteria that was put forth in the BIL. I see airports prioritizing security and safety functions and components of their airports.
It runs from fire and life safety systems and egress all the way up to aircraft rescue and firefighting facilities and more specialty items they need. I'm hearing them report out to us on how they're timing their projects. Some of those things are floating higher in priority based on available funding.
AB: As a builder, what does the industry need to do to meet the challenges of hitting BIL timelines with issues related to supply shortages?
CS: If I could request one thing as the builder, I would want our airport clients to be as upfront, open as possible from day one on what the funding source and structure is for any project. We want to be in compliance and there's no discovery along the way that we need to backtrack or add on additional information. We just want to make sure we’re, organized and in complete compliance to make sure that there's no questions.
AB: We’re no longer talking about reopening air travel but building for the future. What are you most excited about for the industry looking ahead into 2023?
CS: I geek out on baggage systems. I know it's going to continue as a major trend and that provides a great challenge for us to apply our skills. We’re looking at doing things like we did at Palm Springs where we built a brand-new bag channeling tunnel and utility tunnel under historic existing building in order to access a brand-new facility.
Also, the improvements of the hold rooms and making them more comfortable for passengers. I know there's a lot of demand for a quiet space. The airline lounges and other retail lounges and spaces are packed every time I go into one. There will continue to be more work in that area of amenities as well.
About the Author
Joe Petrie
Editor & Chief
Joe Petrie is the Editorial Director for the Endeavor Aviation Group.
Joe has spent the past 20 years writing about the most cutting-edge topics related to transportation and policy in a variety of sectors with an emphasis on transportation issues for the past 15 years.
Contact: Joe Petrie
Editor & Chief | Airport Business
+1-920-568-8399
>> To download the AviationPros media kits, visit: Marketing Resource Center
>>Check out our aviation magazines: Ground Support Worldwide | Airport Business | Aircraft Maintenance Technology