Solid Answers for Successful Airports
Aviation industry professionals involved in the procurement of new buildings are exceedingly aware of tension fabric structures as a cost-effective construction option, whether for aircraft housing, maintenance hangars, cargo handling and logistics, or any other support facility needed at an airport.
They are equally aware that not every fabric building style available on the market offers the same level of quality and performance. Therefore, it’s no surprise that fabric building manufacturers must field a lot of questions about their ability to handle the particular needs of a given airport application before being considered for a project. Naturally, different suppliers are able to answer and address those concerns with widely varying degrees of confidence.
Water Mitigation
Because many airport officials are familiar with older style, web-truss fabric structures – defined by their curved sidewall or “hoop” shape appearance – there are understandable concerns about the ability to mitigate water runoff from the roof of a fabric building. Hoop structures all share the same issue of rain, snow and ice running right down to the base of the building.
With no ability to control water runoff, these traditional fabric structures are at the mercy of the surrounding grade, meaning they could potentially propel excess water onto the tarmac, damage landscape and foundations around the building, or even allow water to infiltrate the structure itself. These shortcomings are at odds with the requirements of today’s airport authorities, which almost universally demand that new building construction will include gutters and downspouts to control runoff.
Several years ago, a key advancement was introduced when Legacy Building Solutions began applying rigid-frame engineering to its fabric building designs. The concept uses structural steel I-beams instead of a web truss frame, making it almost identical to conventional construction methods, but with the added benefits afforded by tension fabric membrane cladding.
With a rigid-frame fabric building, engineers can incorporate overhangs – at a standard width of 18 inches or customized to the user’s specifications – and much more. Gutters and downspouts can be included in the planning stages and easily applied. In colder climates, icebreakers can be added to break up snow coming off the roof.
Rigid-frame design is not purely about adding bells and whistles, however. Anything and everything about the building specifications can be established at the beginning of the project. For example, the existing grade for a new building site might already be sloped to help with water mitigation. In such a case, engineers may need to adjust the sidewall height on one end of the building to match the surface grade. Such adjustments are not only possible with rigid-frame design, but common and simple to execute.
Water mitigation is also a big advantage when the internal applications taking place inside the structure call for a water supply, as controlled water can obviously be collected and stored as well. Fire suppression systems are a requirement for many airport buildings under National Fire Protection Administration (NFPA) 409, depending on the activities that will take place inside or, at times, the discretion of the local fire marshal.
Built to Handle Hanging Loads
The biggest question from project planners about fire suppression is not the water supply, nor is it about the material, since PVC fabric is non-conductive and self-extinguishing in the event of fire. Rather, the key question is whether the building is strong enough to support a fire suppression system on its frame in the first place. This again, goes back to the misperception by some that “fabric structure” somehow equates to a light-duty tent.
With rigid-frame engineering, any type of hanging load that will be suspended from the roof – including sprinklers or foam systems – is accounted for in the original design. Engineers use finite element analysis software to optimize the size of every individual steel beam for the intended application and anticipated load. This way, the needed strength is efficiently built into the frame at all appropriate locations without over-engineering the entire building, which would add unnecessary cost.
A fire suppression system, however, is just one of many possible hanging loads that a user may require for an aviation building application. Lighting and HVAC systems are other common features implemented into a fabric structure.
Overhead cranes are another hanging load typically found in MRO facilities at airports for tasks like aircraft engine repair or even just light tune-ups. Between the weight of the crane itself and the items being moved, users need to be confident that a fabric building’s frame will hold up under the strain of daily crane use.
For hangars housing large aircraft, the hangar doors alone – which can measure in the hundreds of feet wide – demand substantial load support from the building frame. Where traditional fabric structures were limited in the hangar door sizes they could handle, the major door manufacturers have stated that quality rigid-frame fabric buildings can support even their most massive door offerings.
Baggage handling is another building application where frame strength comes into focus. In this case, the structure is equipped with conveyors that are moving live loads that fluctuate throughout the course of the day. Such buildings may also require catwalks for personnel to maneuver around the conveyors and correct potential problems. Building engineers must account for all these changing load factors when working on the initial design.
Collateral loads can be applied to the exterior of a rigid-frame fabric building as well. For example, stronger architectural design can support the weight of solar panels on the roof. With the right setup, some aviation buildings have been able to add enough solar panels to operate entirely off the grid.
Light Years Ahead
A big reason that aviation professionals look toward fabric buildings in the first place in that fabric roofing is highly translucent, allowing abundant natural light to enter uninsulated structures and reducing the need for electric lighting while working during the day.
While this benefit has long been known in the industry, advanced PVC fabrics have brought even more longevity and performance to fabric membranes while still allowing sunlight to illuminate every corner of a building. The bright interior of a fabric structure consistently stands in stark contrast to the dark, shadowy corners of metal buildings.
A question that is not unique to fabric building suppliers, but rather that applies to all construction contractors in general, is how quickly the entire process can be completed. It’s a fact of life in almost any industry that by the time the decision is made to move ahead with a new building project, the need for it already exists. This is especially true in aviation where the cost of a structure often pales in comparison to high-value assets like aircraft, which need to be covered quickly and confidently.
Tension fabric buildings can be provided much more quickly than tilt-up construction or other conventional methods – up to four times faster, in fact, depending on the supplier.
Another factor in delivery time is what the supply chain looks like. While many fabric structure suppliers outsource their frame and fabric manufacturing, some industry leaders have invested in their own on-site facilities and personnel to manufacture steel frames and components, as well as produce the fabric panels. With more control over the whole process – including the engineering phase before manufacturing begins – fabric building companies can ensure both faster project delivery and a higher quality product.
Taking this a step further to become a full-service one-stop shop, some manufacturers employ their own in-house professional installation crews. Having dedicated personnel naturally makes each construction project more efficient and helps ensure the work is done right the first time, and on time.
Getting the project completed quickly isn’t the only timing factor when it comes to aviation building construction. The nature of the business and the fact that airlines are typically constructing on leased airport property, and not their own land, presents something of a conundrum: The building must be solid enough to handle all the required tasks, but its intended period of use on the original site may be only five to 10 years, or less.
To get the most long-term bang out of their investment buck, building users understandably gravitate toward portable options. Many fabric buildings – especially rigid-frame structures – are engineered to be permanent, but are designed to be portable. Should the need arise to change locations within a few years, the buildings can be disassembled and re-constructed on a new site.
Optimized Solutions
Aviation building applications come with many intended uses and requirements. A lot is at stake, so it’s natural to be thorough and question what various fabric building manufacturers can truly provide. A proper engineering solution will answer all those questions and then some, allowing users to accomplish all their goals, and to do so with complete peace of mind.
Eric Donnay has over a decade of experience in customer service and sales, in addition to 13 years of experience in industrial, commercial and residential construction. As VP of Sales at Legacy Building Solutions, Eric is responsible for managing sales staff and processes. He is dedicated to helping sales staff find unique solutions to specific customer requirements.
Sara Davis has over 15 years of experience in sales and customer relations. She acts as a liaison between the customer and Legacy Building Solutions, helping aviation clients with their building solutions and bringing all parties to the table to streamline and enhance the purchasing process.
About the Author
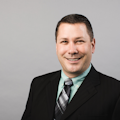
Eric Donnay
Vice President of Sales
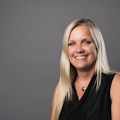