Make Your Airport Part of an Exciting Trend in AST Corrosion Protection
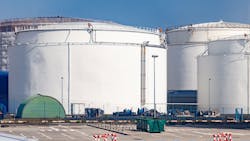
Airports go through hundreds of thousands of gallons of jet fuel each day, requiring tank farms to store plenty of reserve fuel onsite. These aboveground storage tanks (ASTs) are under strict regulations to ensure physical and environmental safety, including the protection of tank floors from corrosion. While cathodic protection (CP) has long been a go-to for corrosion inhibition, the last two decades of tank protection have seen Volatile Corrosion Inhibitors (VCIs) become a new industry standard that offer a smart solution for protecting storage tanks at airports and beyond.
Why Use VCIs to Protect Airport ASTs from Corrosion?
Corrosion protection of storage tank bottoms has many incentives. Corrosion eats away at the metal floor, ultimately leading to hazardous leaks if left unchecked and unrepaired. Any measures that prevent corrosion and reduce repairs can therefore save time, money, and hassle in the long run. CP is often used to inhibit corrosion by sending an electrical current through the tank pad that offsets the normal electrochemical reaction of a corrosion cell. If the tank floor stays in contact with the electrical current, corrosion is mitigated. However, because tank floors are uneven and can bend and create air pockets as the tank is filled and refilled, some areas of the tank floor will not be in constant contact with the treated sand pad, allowing for patches of corrosion.
In contrast, VCIs injected under the tank floor diffuse throughout the void space, forming a protective molecular layer on all metal surfaces they reach. This technology works on its own or in conjunction with CP, which has been the main standard for AST bottom corrosion protection for years. Interestingly, the two technologies show signs of being mutually beneficial, according to Eric Uutala (Technical Sales Manager at Cortec® Corporation), an expert in VCIs and AST protection who is involved in a major VCI/CP research project. Uutala explained, “Over time, it seems that the VCI actually increases the efficiency of cathodic protection.” He also noted that, based on evidence from field and lab testing, it may even reduce the amount of power needed for CP.
Two other key advantages of using VCI technology for ASTs are that (1) VCIs do not require electricity, and (2) they can be applied at any stage of a tank’s life cycle. As far as the first point is concerned, VCIs will continue to work if there is a power outage or if the CP current must be temporarily turned off, making them an important backup to CP. However, Uutala believes the second point regarding the flexibility and versatility of VCIs is the most important for airport leadership to know. Since VCIs can be applied not only before new tanks are built, but also after they are filled and in service, VCI technology minimizes the loss of time and money that might otherwise be required to drain high volumes of fuel to install a new corrosion protection system. It also means that it is never too late to apply VCIs to existing tanks.
Although the trend toward using VCIs for ASTs has been several decades in the making, the fact that it takes so much time to see long-term effects, gather data, and shift industry mentality means that many in the world of storage tank management are still becoming familiar with the idea of VCIs for ASTs. It is also significant that despite this relative “novelty,” VCI technology has already been codified in industry standards API Technical Report 655 and AMPP SP21474-2023, opening the door for widespread acceptance as awareness grows. While the majority of tanks now protected with VCIs are in the Middle East and North America, Uutala noted that application has started to take off in Asia. Understandably, oil and gas facilities are the main clients, but the use and storage of large amounts of jet fuel at airports also makes these critical transportation hubs natural candidates to benefit from VCI technology.
What Should Airport Leadership Be Aware of When Considering VCIs?
Uutala shared several important considerations for airport leadership looking at possibly using VCIs to protect their tank farms. One of these is timing. While an inherent advantage of VCIs is that they can be applied at any stage of the tank service life, the best time to consider implementing them is when constructing new tanks. According to Uutala, this “gives you the best scenario because you can set up a dispensing system that allows for the best . . . spread of product.” It also makes future reapplication easier whenever it is needed one, two, or three decades in the future. “Everything’s already there,” Uutala explained. “You only have to hook [VCIs] up into one spot generally and then everything will . . . fill and spread.”
Another preferrable time to consider applying VCIs is when the tank is emptied for a routine 10-year API inspection. Uutala noted that if one part of the tank has corrosion and needs to be replaced, workers can inject VCI into the tank bottom through the temporary opening. Even without floor replacement, inspection time gives workers the option of drilling tiny holes less than one inch (2.54 cm) in diameter through the tank floor to allow for VCI injection wherever needed. Uutala explained that these holes can easily be welded over to complete a less invasive process than drilling through the tank ring wall.
No matter what stage of life the tank is in, Uutala notes that it is imperative to work with a qualified, experienced applicator familiar with the specialized VCI application process. On projects with which Uutala is involved, the first step is to send the client a two-page questionnaire to identify characteristics such as tank size, age, contents, inspection records (to give a better idea of areas more vulnerable to corrosion), and information on any parts of the floor that may already have been replaced. The answers to these questions allow the applicator to “qualify,” or understand, the project before starting, helping them calculate how much VCI to apply, in what form to apply it, and where/how to apply it.
As mentioned above, the best times to apply VCIs are during construction and tank inspection, and these scenarios will dictate where and how to apply the chemistry. However, the beauty of VCIs is that they can also be applied while the tank is in service, without having to drain the jet fuel. In this case, workers can drill through the concrete ring wall at evenly spaced points (number of injection sites depends on the size of the tank) and insert specially designed pipes through which the product can be injected and dispersed.
For all tanks, no matter their life cycle stage, a chime seal system should be applied (or replaced) at the time of VCI injection to prevent the ingress of moisture and the escape of VCIs. It is also a best practice to insert electrical resistance probes beneath the tank for corrosion monitoring. These probes should be placed as far away from VCI injection points as possible for the most accurate readings. Although not a perfect representation of what is happening beneath the tank floor, these data points provide a baseline of information on the amount or location of any corrosion activity that may be taking place between inspections, allowing tank owners to keep a closer eye on areas of concern and get a general idea of how the VCIs may be performing.
A Prime Time to Adopt VCIs
As with any industry that involves ASTs, the aviation sector needs solutions to corrosion that make sense practically and economically. VCI measures up to that standard as a minimally invasive technology with vapor-phase action that complements CP and even works when the power is off. Given its new place in industry standards and its accumulating history of field use, now is an excellent time for airports to consider adopting VCI technology to enhance corrosion protection on their own tank farms.
About the Author
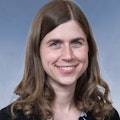
Julie Holmquist
Marketing Content Writer
Julie Holmquist has been a Marketing Content Writer at Cortec® Corporation (https://www.cortecvci.com/) for more than nine years and enjoys learning about the many areas of industry technology where VCIs can be applied. Contact her at [email protected] or email [email protected] for more information.