In a deal that closed in August, Worldwide Flight Services has leased two buildings at Phoenix-Mesa Gateway Airport — one dedicated solely to the rebuilding of the company’s GSE.
The new facilities total about 40,000 square feet and will be utilized to “zero time” units, a process of essentially shedding the vehicle of everything but its frame and replacing materials.
“The goal is to renew specific areas of our fleet while incorporating new technology, emissions reductions and cost savings in the process,” says Scott Whitfill, director of maintenance at WFS.
Among the types of units that will undergo the refurbishment include bag tractors, belt loaders, pushbacks and pallet loaders. Additional types of equipment will be considered in the future, though it is dependant upon the economic return and the potential life extension of each unit, according to Whitfill.
The company has decided that the investment in labor and materials to do the projects in-house is a good one. “Based on our own knowledge of rebuilding equipment, we know that it is possible to run an in-house program more economically than outsourcing the work,” he says.
The Mesa location will initially have a manager, staff assistant and three to five mechanics to run the projects.
The company views a blend of acquisition and rebuilding of GSE as bringing the most economic benefit. “Naturally, WFS would like to simply go out and buy or lease all new equipment however, to reach our goals we must also be financially responsible,” he says. “Therefore, by having a blend of rebuild and acquisition we get the most benefit for the company.”
WFS anticipates that each unit selected to be rebuilt will be at least 10 years old, and that a zero-time refurbishment will add about 8 or more years to the unit life.
In addition to zero-timing units, the company also expects to convert certain units to electric, Whitfill says.
The facility will also provide guidance for other stations in need of assistance with equipment. “A side benefit to having a centralized facility like this is that we will have a concentrated resource of GSE knowledge available to all other WFS stations,” says Bob Maier, director of planning and control GSE. “Therefore, if a station has a problem with a piece of equipment, one call to the Mesa Rebuild Shop provides them with years of knowledge to assist in quickly resolving the problem at hand, as a team.”
In addition to renewing its own fleet of GSE, the company has planned to launch refurbishment services as a line of business for its airline customers at a later date. “We want to first have an impact on our own fleet as well as developing a solid program before going outside,” Whitfill says.
The Southwest Program
Many refurbishing and repowering projects have been ongoing for years throughout the industry, with some airlines completing the work in-house.
Southwest Airlines has served as an example. The carrier has established two shops dedicated to GSE renewal, one in Phoenix and one in Dallas.
The shop in Dallas is devoted to rebuilding and upgrading fossil fuel equipment. It has various ongoing projects in place with units being upgraded on an as-needed basis. The work has been ongoing for more than 15 years.
The shop in Phoenix currently has undergone a repowering project of converting gas and diesel engines to electric. “Right now we’re focused on belt loaders and pushback tractors and no other products at this time, and we’re doing this to meet emission goals for the state of California and beyond,” says Larry Laney, director of GSE at Southwest. “It is our goal to refurbish a piece of equipment for 50 percent of the cost of new or less. If we can accomplish our goal, we know it makes economical sense and we will save money. We plan on continuing our combination of buying new bag tugs, beltloaders, and pushbacks as well as refurbishing and converting equipment to electric as a way to keep our fleet fresh and meet our emission and environmental stewardship goals.”
Southwest’s additional shop locations may also complete projects. “Although our 21 other GSE shops around the system do not have dedicated staff to perform major refurbishment programs, they occasionally overhaul equipment for their city or region,” he says.
When it comes to making the decision to rebuild or buy new, Laney says several items should be considered. “You need to factor in the total cost of labor, material, shipping, can you get parts moving forward to support the equipment or is it so flat out obsolete that it needs to be replaced, lack of warranty, etc.”
He adds, “Taking these things into consideration and if you can refurbish equipment for around 50 percent of new, then it makes sense to strategically select some fleet types to rebuild. Our outstanding GSE mechanics at Southwest Airlines have done a great job controlling our cost on these projects and have made it possible for this program to be a strategic option for us.”
American Airlines’ Strategy
American Airlines has also identified great value in rebuilding some unit types within its network. Having formulated an entire fleet renewal program for its GSE, the carrier has taken on GSE rebuilding projects in-house. To evaluate potential candidates for refurbishment, as well as incorporating new technology, it created a steering committee comprised of American’s GSE users and mechanics.
One type of vehicle that was selected was bag tractors. The 15- to 20-year old units were selected after a cost analysis showed the airline could do it at about 40 percent the cost of new equipment, according to Gary Bird, director of ground support equipment and facilities maintenance at American Airlines.
The airline has rebuilt about 400 of about 900 bag tractors since May 2009, refurbishing an average of 10 tractors per week. With the refurbishment efforts occurring in a 12,000-square-foot facility in St. Louis, the airline zero-timed the units while upgrading some parts — such as rust corrosion primer/paint, LED lighting, redesigned wiring harness, electric cooling fan, 2nd generation electronic fuel injection system, simplified dashboard gauges, standardized wheel size and more durable seating. “We didn’t really restore the tractor, we remanufactured the tractor,” he says. “While many of these changes are internal to the tractor, we changed the appearance, such as the LED lighting and a new paints scheme, which establishes a separate identity on the ramp.”
And the airline has worked to standardize many of the internal mechanisms in the tugs to streamline the work of mechanics, as well as simplify the demand for parts. “We chose the most common tractor that we had,” he says. “We have one type of engine and one type of transmission – everything in the 900 tractors will be identical.”
Another project that is underway by the carrier is the refurbishment of about 60 widebody loaders in five cities: Miami, Chicago, Dallas, New York City and Los Angeles. With two mechanics on duty at each location to complete the project, the primary focus has been on rebuilding hydraulic systems. “Hydraulics are very critical for the widebody loader,” he says. “We brought the critical parts and processes down to zero-time.”
Bird says the rebuilding projects have been very successful overall for American Airlines, so more projects are in the pipeline. “We’re already looking at the next equipment type,” he says. “We’ve identified four or five types of equipment that make much more sense to take this approach of restoration than it does to replace.”
Partnership for Renewal
US Airways has also worked on updating its fleet over the past few years, working with a third-party, Hercules Engine Components, to zero-time bag tugs and belt loaders. With that project having come to a close, US Airways is now repowering belt loaders in Charlotte with newer Tier 3 diesel engines.
The project has been partially funded through the Mecklenburg County GRADE (Grant to Replace Aging Diesel Engines) program in North Carolina. The company will be updating about 40 models that date back to the 1980s.
“It’s basically doing two things: We are helping to improve the air quality in Mecklenburg County and improving the economy and reliability of our belt loader fleet” says Greg Nist, GSE fleet manager at US Airways. “We are being reimbursed for a portion of the cost of repower on each unit. We are installing an engine kit from Hercules and repairing the chassis and systems at our CLT GSE Facility. As part of the grant requirements, we must destroy the old engine and submit documentation back to the county.”
US Airways is also looking to have portions of its existing belt loader fleet converted from diesel to electric by Hercules. “They’ve done a prototype for us, and we’re waiting to see where we are going to go with this project at this point,” Nist says.
For both conversions, the carrier expects to get around 10 more years in the life of the unit. The savings associated with updating the belt loaders are worth the effort, according to Nist. “For zero-time rebuilds, the units that are closer to half the cost of a new vehicle are obviously a good investment on the airline’s part,” he says. “There are some units that are a little more expensive to rebuild, such as tugs, which generally run a little higher than half the cost, but rebuilt belt loaders are running about half the cost of a new belt loader.”
Nist says the company’s future decisions to buy new or rebuild will likely depend upon funding that can be obtained to help subsidize the cost. “Some of the grant programs require you to buy new vehicles, some will require or allow you to rebuild older vehicles and modify them to current technology,” he says. “We will rebuild equipment if it is acceptable and provides us a substantial reduction in cost over new.”
Overall, the US Airways GSE fleet will largely be looking to go electric, partly because it presents the best opportunity for funding. “Our focus is going to be on improving our electrical fleet, and growing our electric fleet, replacing old diesel equipment and gas-powered equipment with electric equipment,” he says.
About the Author
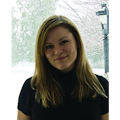