Airports Turn to Autonomous Cleaning Robots to Maintain Cleanliness
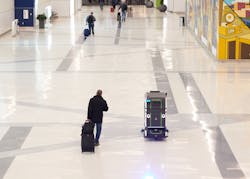
Autonomous cleaning robots offer many benefits to airport operations and the traveler’s experience. They show guests that the airport cares about cleanliness and they can help alleviate staff workload allowing them to focus their attention on other duties. But before an airport decides to implement these robots, there are many things to consider such as which products? Is the airport properly set up for autonomous cleaners? What impact will they have on staff? How will they improve day-to-day operations? Hear from airports that are already using these robots.
Build with Robots Breezy One and Breezy Blue at the Albuquerque International Sunport
The Albuquerque International Sunport (ABQ) is currently using four of Build with Robots products, models Breezy One and Breezy Blue.
The Breezy One is a fully autonomous mobile robot made for cleaning large spaces while the Breezy Blue is a smart device that can be carried around or left to disinfect smaller rooms on a schedule via a mobile app.
The Sunport decided to demo these products in June 2020 to learn more about the technology before fully implementing them.
Airport Facilities Manager for the City of Albuquerque at the Albuquerque International Sunport David Urioste said since implementation, the experience has been positive.
“It allows us to provide the sanitation and disinfection without reduction in labor force. We're able to utilize our custodial staff for their same task of duties that they normally have with their job descriptions,” Urioste said. “And we're able to sanitize our airport, keep it in a clean and safe manner for our travelers so our custodians can actually focus on the service that they provide here for the Sunport and their travelers.”
Urioste said the robots are very user-friendly and each device is mapped out to the specific area of the airport it is servicing.
“We have the ability to change the routing very simply. They can come in one day and change the routing for alterations here in the Sunport,” Urioste said. “It has a basic map of our Sunport and they can change due to layout of chairs, they can change to a current project we're having here due to construction. If we have to make alterations, it's simple changes to a map and it's uploaded into the robot. Easy functionality.”
Build with Robots CEO Chris Ziomek said the implementation of the robots has helped the Sunport to achieve GBAC STAR accreditation.
“There's accreditation facilities like GBAC, they're a subgroup of the largest cleaning and sanitization trade group, ISSA. They've selected our products as part of established protocols to get certified,” Ziomek said. “They have a star rating, and some of the airports we're in are using our products to get their star accreditation.”
The Breezy One robots are currently set up in the passenger spaces and the secures spaces while Breezy Blue products are being utilized in the staff spaces.
“It's great to be keeping all the passengers safe, but the staff are equally, maybe more important in some cases, because if they get ill, you're down workers,” Ziomek said. “I guess the way to think about it is that it really is best practice, and it's a way for the airport to show the traveling public that they're doing everything to keep them safe. So, they help with worker safety certainly, but it also helped with passenger confidence. So, it helped keep the airports, keep passengers feeling more safe when they're entering the airports, getting more passengers back traveling.”
Tennant at Baltimore Washington Thurgood International Airport
At Baltimore Washington Thurgood International Airport (BWI), Chimes staff are using eight of Tennant’s autonomous robots in three different models that vary in size: the T380AMR, T7AMR and the T16AMR.
“Everyone knows when you're traveling, you're with however many thousands of your best friends that you've never met, you don't know where they are, and I think when you see an airport investing in technology around cleaning, it gives a lot of people that peace of mind because they're taking their cleaning seriously by investing in the latest and greatest technology,” said Tennant Senior Product Line Category Manager Dennis Collins. “So having a robot running around is, I think, a major mind easer. People are at different comfort levels with travel right now, and I think that is a great way that airports have been able to address that.”
According to Tennant National Strategic Account Manager Ryan Fergus, the airport installed these robots over three phases. First, they installed the small and medium size units. During the second phase, another batch of small and medium units were installed and during the final phase two large industrial size units were implemented.
Due to the number of robots that were installed, Tennant worked closely with the airport to map out the regions that each robot would be responsible for cleaning.
“So for us, from an implementation standpoint, as I understand it, this is the most AMR scrubbers at any single customer location currently, so we had to get very strategic with where each machine was going to be, so that involved working with the customer and setting up different zones throughout the airport, and then essentially assigning robots from the fleet to essentially "patrol" each of those specific zones,” Fergus said. “So, it really involved getting into an overall mapping of the airport, cutting it up into different subsections, and then being able to assign the appropriate robot to handle that section of the airport. That was really some key pre-work we had to do.”
The T380AMR is Tennant’s smallest autonomous cleaner, the T7AMR is Tennant’s medium size cleaner and the T16AMR is the largest cleaner.
“Some are going to cover more space because their scrub deck is bigger and they're just bigger machines, they have bigger water tanks, they're going to have larger batteries, like our T16AMR, it would be great in large open concourses like the main stretches of a concourse or even anywhere that's a large open area,” Collins said. “T7AMR is going to be smaller, it's going to be a bit more maneuverable and it's going to take tighter turns, getting in between the rope lines and potentially security. Then our T380AMR is going to be really great actually for the food court, even if the chairs are there, depending on how close the tables are to each other, and then especially if there's hard floor and the gates, a T3 could potentially go around the benches as well.”
Collins added that safety is one, two and three in terms of operational concern.
“We want to make sure these products are safe, and they are designed to work around people,” Collins said. “And so, we have redundancies and sensors. Also, there's redundancies in software, and so if anything were to be going wrong, the default is for the machine to say, ‘Hey, something's wrong, I need help’. We do rigorous testing with every software update, third-party testing, etc.”
Contract Administrator for Chimes (operator of Tennant robots at BWI) Douglas Rosenberger said it’s been fun to see the robots in action with guests.
“We have people that like to walk in front of it to see what it's going to do. The kids get excited about it because you're watching something that's relatively large, and it's going along with a seat belt on and a flashing light, and it's like an invisible person is on it. They like to stand there and watch that,” Rosenberger said. “That's something that draws a lot of people's attention. But sometimes I think they want to just test it out to see what it will do. And with the technology that's built into it, it'll prove it. It will stop if you walk out in front of it. So that's a good feature.”
Neo Avidbots at Cincinnati/Northern Kentucky International Airport
The Cincinnati/Northern Kentucky International Airport (CVG) is another airport that is currently utilizing autonomous cleaners. In 2019, CVG implemented two Neo Avidbots robots.
Avidbots CEO and Co-Founder Faizan Sheikh said the passengers at CVG love it.
“There's a lot of passengers who take pictures, selfies, videos with the robot while it's cleaning. Especially kids take pictures, their parents take pictures of their kids with a robot,” Sheikh said.
Sheikh said Avidbots Neo was designed to be as simple as possible for operators. With just three clicks on the robot’s touchscreen, they are ready to start cleaning.
“They've had to sign no extra staff or anything. In fact, they've taken the staff they had who were previously running a manual machine cleaning and redirected them to other higher value tasks, like taking care of the restrooms at a higher frequency than they did before,” Sheikh said. “So, it's been a net positive in terms of how the staff have adapted to it and how the staff has been reallocated to do other work.”
Cincinnati/Northern Kentucky International Airport Chief Innovation Officer Brian Cobb said the airport saw the need to implement these robots due to an increase in passenger growth rate.
“Our passenger growth rate has just continued to skyrocket over the last decade. However, with that comes challenges,” Cobb said. “Our floor care team was coming back to us saying, ‘hey, our operational day continues to get tighter and tighter with flights arriving in the wee hours of the morning, which is leaving us less and less time to actually dedicate to cleaning large areas of the flooring.’ And we started kind of running different scenarios. The last thing that we would want to do obviously is shut down large sections of flooring and really encroach on the customer experience, number one, and disrupt the passenger flow. So, we kind of hypothesized, what if we were able to find a robotic floor cleaner?
Cobb said they initially started the robots on the overnight shift making sure that it was functioning fine before operating it during the day.
“We take pride in the cleanliness of our airport environment, so super critical from a customer experience aspect,” Cobb said. “I'm sure as you go to a restaurant, you walk in, if you were to see a dirty environment, you immediately formulate an opinion of that restaurant. Much the same operates in an airport environment.”
Cobb said one thing they did not account for was how big of a social media hit the robots would become.
“We did not necessarily anticipate that the phones would come out, the videotaping starts or the taping begins, and we started to see Twitter comments hit pretty rapidly,” Cobb said. “What we also didn't anticipate is - we launched that right about January in the operational day of 2020. COVID was shortly thereafter. So indirectly the positive social media hit became, ‘look how much this airport is concerned about the cleanliness of their environment and subsequently our health and safety’. So, it just became a win-win-win across the board. And from our staffing perspective, immediately our staff saw the benefit of, ‘hey, we could never get in there during the operational day with this amount of passengers, but the bot is able to actually become a stop gap for us’.”
Usability
Cobb said the airport has some displays from local museums and one of the staff’s favorite feature of Neo is being able to tell the robot how close it can get to the display for safety purposes.
“We could bring it [the robots] up as close to a few inches or as far away as three feet. So, from that perspective, we could pretty much tailor the mapping process around where the bot could go, where we wanted it to go,” Cobb said. “And then when it's finished with its assignment, it will send a report to our local supervisor who's in charge of that bot on their mobile device. It's just phenomenal on the capabilities.”
Cobb said in terms of reporting capabilities, the amount of data the robots are providing is very impressive.
“It provides as far as how much water it’s used, the cleaning capabilities, the square footage that it's cleaned, the hours that it took or minutes in that particular situation in that area,” Cobb said.
Cobb also said because of how many cameras are on board these robots, they can also see what’s happening in real time.
“There's a whole other layer to this, is that it's not just a cleaning bot,” Cobb said. “There's almost like a security implication to this as well that's frankly to some degree, yet to be explored that we continue to work with Avidbots on.”
Cobb continued, “The beauty of all of that is that it doesn't require somebody to come back and constantly map and be concerned about what else are we putting in place and what do we have to do now with the bot that's going to impact it. So as construction occurs, as say, kiosks are erected and concessions are being sold, perhaps now in the middle of the floor, the bot accounts for that.”
About the Author
Christina Marsh
Editor
Christina Marsh (Basken) is a passionate aviation enthusiast and sport pilot with industry knowledge and experience in writing and editing for digital and print publications as well as creative content in photography, videography, and podcasting.
Christina graduated from the University of Wisconsin-Oshkosh with a bachelor’s degree in journalism with a visual emphasis.