Aviation Ground Operations: 5 Tips for Addressing Labor Shortages, Delays & Baggage Disruption
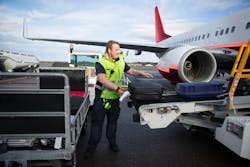
Air travel has been a little bumpy lately. Under-staffed airline and ground operations and maintenance crews, flight delays, cancellations, and lost and delayed luggage are contributing to overworked ground crews, disgruntled passengers, and poor airline performance. Here are five tips aviation operations teams can apply to right-size their technology spend by focusing on smart human-centric technology solutions for quick relief.
1. Approach Problem-Solving with Your Human Workforce in Mind
Pilot shortages are not the only labor issue facing airlines and the industry at large. Aircraft mechanics, flight line employees, baggage handlers, customer service, and other ground operations and service roles are also short staffed. This issue is neither new nor likely to go away soon. Yet it requires a new approach to introducing new technology. Wearable technology can streamline processes for your workforce. Make sure it is human-centered, augments the way your personnel work today, and intelligently connects them to the Internet of Things (IoT) so you can build toward future digitization strategies.
2. Establish Proper Guidance and Priority Handling
Aside from industry expertise, precision and agility are instrumental for critical aviation processes. Take aircraft maintenance for example. Everything hinges on logistics. That’s why you need data capturing technology at the source of asset handling, service transaction, or process workflow that allows for immediate feedback and proper guidance. Just received a spare part for an aircraft on the ground (AOG) that needs express handling? A wearable barcode scanner can automate a dedicated AOG alert to make sure everything is on the right fast track. Maintenance teams work more efficiently, with up-to-the-minute information and real time tracking.
3. Allow for Hands-Free Barcode Scanning in Your Baggage Handling
Surging air travel demand and staffing shortages are contributing to unprecedented lost and delayed checked luggage and baggage handling across the globe. However, throwing any technology at the problem won’t solve the chaos. The right design and form factor are key. Different luggage sizes and bulkiness are a seemingly insurmountable obstacle for some scanning technology. The job is strenuous and requires both hands by handlers. Make sure your staff do not have to pick up a clunky barcode scanner and drop it off after every scan. Choose scanners that are hands free and a natural extension of the way your baggage handlers work. Done correctly, this can lead to invaluable efficiency gains. For example, Talma, one of the largest airport services companies in Latin America, turned to smart wearable barcode scanners from ProGlove to realize a 50 percent gain in baggage handling processes, and 100 percent more efficient use of personnel. The efficiency improvement was so great that Talma was able to strategically relocate operators to other critical areas of operations.
4. Eliminate Paper-Based Workflows
A fast-paced industry such as aviation cannot rely on paper as its sole guiding principle. Unnecessary paper-based instructions waste resources and are error prone. One of our airline customers found that they could reduce flight delays by 15 to 20 percent by eliminating paper in their catering by using wearable barcode scanners.
5. Carefully Evaluate Moonshot Technologies
Whenever a crisis hits, some pundits claim that you should have seen it coming, and often propose an exploratory and arguably “groundbreaking” technology that promises to solve all problems. To that end, there is much talk about how automation and robotics will solve the issues facing the aviation industry today. While automation and robotics can indeed help in certain areas, other areas are not feasible. And these systems are incredibly complex and costly. So, stay calm and carefully evaluate those shiny, new technologies that promise a moonshot. Instead, look for affordable investments that work intuitively with your workforce and can deliver an immediate impact.
As the airline industry continues to navigate today’s challenges, operations teams should look to smart uses of technology and wearables to increase process efficiencies with existing headcount, improve worker experience and ergonomics, and gain operational insights to drive continual process improvement.
Andreas Koenig is CEO of ProGlove, a company that builds the smallest, lightest, and toughest barcode scanners in the world, connecting workers to the Internet of Things. ProGlove’s MARK product family of smart gloves provides an ergonomic, hands-free barcode scanning solution that helps workers increase productivity and optimize workflow.
About the Author
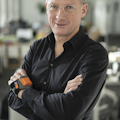
Andreas Koenig
CEO
Andreas Koenig is CEO of ProGlove, a company that builds the smallest, lightest, and toughest barcode scanners in the world, connecting workers to the Internet of Things.