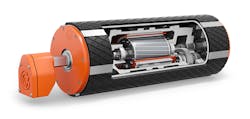
Upgrading an airport baggage handling system offers airports a unique opportunity to address operational reliability, sustainability and a better passenger experience knowing luggage will get to the travelers in a timely fashion.
Energy efficient components are becoming more prevalent in baggage handling systems. Efficiency is a quantifiable standard established by the International Electrotechnical Commission (IEC). The standard defines five International Efficiency (IE) classes for single-speed electric motors, related to efficiency, power output and size for motors.
Picking a motor type for your drivetrain can be difficult, as each has advantages and disadvantages.
Reliable Systems Keep Bags Moving
Airports and airlines need to keep their baggage handling systems online to ensure traffic keeps moving and delays aren’t created by broken systems.
“What I’m seeing is everyone looking to put their best foot forward,” said James Chandler, key markets manager for Nord Drivesystems. “How efficient can I be? Is it from a retrofit or is it looking at a full CAPEX project to renovate or upgrade the complete system? In many cases, airports are taking a deep dive into looking at how they upgrade and be efficient.”
Chandler said U.S. airports want a network connection of their systems to keep on top of their performance and provide a tool for predictive maintenance. This gives customers and end users oversight of their systems. Visibility also helps with efficient commissioning and seeing what drives are up and which are down, etc.
Monitoring these elements provides feedback on how a system is performing and data trends will show when an item needs to be addressed before failure.
“It’s not just all about more efficiency. It’s all about durability and uptime,” Chandler said. “All airports are looking at reliability and being up when those bags need to get on the next airport and keeping in line with the traveler’s schedule.”
Predictive analytics monitors live operational data measured by various sensors and compares it to historical data to identify abnormalities within the measurements and uses probability through machine learning to predict necessary repairs and imminent component failures.
Larry Studdiford, president, Studdiford Technical Solutions, LLC said a good predictive analytics platform can provide many operational benefits; the most promising being the ability to develop a planned, versus a reactionary, maintenance and repair schedule. This reduces the number of surprise outages and potentially helps reduce the staff headcount.
It also identifies equipment irregularities with enough time to ensure that materials required to repair or replace the equipment is available on hand.
“Both these, and other benefits drive towards a status-based maintenance approach instead of a time-based maintenance plan, allow repair and replacement when components require it, and not necessarily based on a calendar-driven schedule,” Studdiford said. “This could also lead to an increased life cycle of equipment while monitoring components during their decline instead of replacing based on the manufacturer’s recommendation. There are huge overall cost savings to be had with regard to the life of a BHS and its overall total cost of ownership.”
Nord Drivesystems recently introduced its generation of IE5+ motors utilizing a reduced noise, high efficiency design suited to acoustically sensitive areas in airports. Mounting solutions are flexible and can be direct mounted to a gearbox or mounted to a NEMA or IEC adapter.
The two frame sizes, 70 and 90, offer a power range from 0.5 – 3HP and a speed range from 0 – 2,100 rpm. IE5+ synchronous motors are outfitted with an integrated encoder that can be programmed for precise control over speed, synchronization and position.
Permanent magnet motors (PMM) like the IE5+ offer durability and sustainable energy savings for airports.
“We’ve seen projects in testing where it provided double-digit efficiency gains over previous installations,” Chandler said. “However, we also look at what we can take out. We’ve looked at direct drive solutions, eliminating pulleys and chains so there’s a lot of opportunity in increased gains.”
Studdiford said the permanent magnet motors promise higher performance and generally lower weight than traditional AC induction motors. They also tend to have a smaller footprint, which makes permanent magnet motors good for retrofitting older systems.
“While more expensive than induction motors in their initial product cost, PMMs and their energy savings can realize a full return on investment in as little as two years,” he said. “They are also synchronous, which allows them to work in applications where induction motors cannot.”
Drum Motors Drive Potential
North American airports and airlines want their luggage systems to handle twice as many bags on a similar footprint as their current baggage handling system. Drum motors provide a solution to meet this demand.
Drum motors hermetically seal the electric motor and gear reducer inside the head drive roller. This eliminates the need for external drive system components, such as chains, sprockets and chain guards. It also eliminates the need for pillow block bearings because the shafts on a drum motor are stationary.
“When you use our drive system, you can put conveyors closer together in a closer space so you can achieve better space utilization,” said Alex Kanaris, president and owner of Van Der Graaf (VDF). “And using these drive systems are going to cost them about 30 percent less than what they’re using now.”
Drum motor mechanical efficiency is about 96 percent compared to 70 percent or 80 percent efficiency of an external drive. The gears are manufactured to AGMA 12 standards, that is honed and ground for low noise standards to 46db compared to 56-60db for conventional systems.
When the conveyor load is higher than what it was designed for and the windings temperature reaches 135 degrees Celsius, an overload protection device connected to the motor control stops feeding voltage to the motor.
Kanaris said VDG designs its drum motors to be maintenance-free for almost 10 years or 80,000 hours. This compares to 37,000 for conventional drive systems, according to VDG testing.
VDG uses high quality components for its motors and all units are sealed under a vacuum to increase the life of the motor. They’re permanently lubricated, so vibration analysis isn’t needed.
“It’s a safer system to use, it doesn’t need to be maintained, you save money on electricity and it provides the same work with less space,” Kanaris said.
Traditional conveyor motors are fan cooled. The newest generation of drum motors address heat via magnetic density of the core and current density of the winding. Kanaris said this redesign allows VDG drum motors to run cooler without the need for external cooling methods. The operating temperature of the VDG motors is 75 degrees Celsius, giving the oil a viscosity of 50-60 centistokes.
“The true source of the heat is current density and magnetic density,” Kanaris said.
Baggage handling systems depend on lagging for operation. Cold bond and hot bond vulcanized conventional lagging relies solely on the adhesive bond between the lagging and the shell to transmit power to the belt. If the lagging process is not properly executed or expired material used, the shear force on the adhesive can result in lagging delamination.
VDG introduced the IronGrip lagging system in 2019, which has steel bars welded across the drive drum with lagging materials between these bars. The system eliminates uneven lagging wear, since the rubber cannot wear below the steel bars.
The IronGrip provides higher pulling force so the belt can perform with less tension. This extends the life of the belt and other mechanical components like bearings and idlers.
In-house tests by VDG estimated the life of the IronGrip lagging to be 4 to 5 times longer than the standard lagging.
“The question is, if we have a conveyor belt drive that consumes 30 percent less energy, requires no maintenance, streamlines the conveyor design, improves belt tracking, increases the life of the belt and the service life of other mechanical components, and lasts longer than traditional external drives that are used today, why the VDG Drum Motor is not used in airline baggage systems,” Kanaris said. “VDG drum motors are very popular in other industries like postal parcel, warehousing, mining, aggregates, agriculture, food processing and others.”
Think Long Term on Your Investment
Supply chain currently remains a challenge and baggage handling systems are not immune to this issue.
Studdiford said many ongoing baggage handling system projects are experiencing delays in various components and parts manufactured overseas, but airports considering improvement projects should not slow down the upfront planning and design phase. By the time those projects go to contract, he believes those supply chain issues should be resolved.
There’s a lot of opportunity when it comes to upgrading baggage handling systems, so Studdiford advises airports to think longer term on their investment.
“If there is one thing that the global pandemic has shown us is that there needs to be more consideration of the total cost of ownership (TCO) of the baggage handling system with regards to maintenance, staffing and longevity of the system,” he said. “In other words, balance out the focus from CAPEX to look at the operational expenditures (OPEX) more closely and the overall best value for the airport in the long run.”
33% of Airport Business readers are planning to upgrade their baggage handling systems within the next five years.
Source: Airport Business 2021 State of the Industry Survey
About the Author
Joe Petrie
Editor & Chief
Joe Petrie is the Editorial Director for the Endeavor Aviation Group.
Joe has spent the past 20 years writing about the most cutting-edge topics related to transportation and policy in a variety of sectors with an emphasis on transportation issues for the past 15 years.
Contact: Joe Petrie
Editor & Chief | Airport Business
+1-920-568-8399
>> To download the AviationPros media kits, visit: Marketing Resource Center
>>Check out our aviation magazines: Ground Support Worldwide | Airport Business | Aircraft Maintenance Technology