In September of 2018, Satair inaugurated a new building located literally a stone throw from the London Heathrow Airport in a commercial development area called Space Waye and as close as possible to Satair customers. AMT was invited to attend the grand opening along with others so we could get a firsthand look at the facility, which beside the warehouse accommodates a new battery overhaul and repair shop.
Chief executive officer of Satair A/S Denmark, Bart Reijen, said in a speech prior the ribbon cutting that the company basically didn’t have any choice not to open this new facility because “since 2011, in six following years we were growing by 150 percent what is a real success story."
The facility was designed and built in close collaboration with Satair which is a stand-alone and Airbus Services Company.The facility, at Space Waye, North Feltham Trading Estate, became fully operational on March 19, 2018 and has six times the area and 11 times the cubic capacity of its previous Heston, Middlesex, facility which Satair had occupied for almost 30 years.
Beside its numerous aviation activities, Satair is one of the world’s largest aviation battery distributors, representing the top five battery manufacturers such as ACME, Concorde, Hawker Enersys, Marathon Norco Aerospace, and Saft, serving some 180 customers like international scheduled airlines, charter carriers, large low-cost airlines, and regional airlines to MRO companies, helicopter owners, business jets, and private aircraft owners.
The increased warehousing and workshop space at Space Waye, with some 1,000 pallet spaces on 20,000 square feet, gives opportunities for expanded capabilities. According to Jon Ravenhall, managing director Satair UK and head of Operations Repair Europe (UK): “It is also our intention to widen the scope of our offering to the market. Being a key part of the Operations Repair Group within Satair, we plan to offer electrically based product repairs, particularly for Airbus proprietary parts. We are working very closely with our Satair and Airbus colleagues in determining a wide range of stocked parts all of which have significant UK demand and we have a development plan for this year and 2019 for both warehousing and repairs.”
Touring the Shop
The next day I was given a personal tour of the new battery repair and overhaul shop by the workshop manager, David Bigley. Currently, Satair handles some 7,500 aircraft batteries a year, making it one of the world’s largest commercial aircraft battery servicing operations. The radically increased warehousing and workshop space at Space Waye allows Satair to expand the battery repair and overhaul shop. Besides being a distribution hub for spares and a battery servicing operation, the Space Waye facility also has expanded office space and being so close to Heathrow it can be used as a convenient meeting location for Airbus, Satair, customers and suppliers. All of the 14 staff previously employed at Heston have moved to Space Waye and have made significant contributions to the design, layout, and functionality of the facility. Six new employees have been recruited both for warehousing and repair operations and the business has started a battery technician apprenticeship scheme through the Way2Work initiative with the first apprentice now engaged. Additional staff is envisaged in 2019.
This Heathrow unit is the single largest commercial shop of its type globally and has been designed to allow growth for at least the next 10 years. Special attention was put on the environment: modern lightning lamps are in use and some 150 solar-panels are mounted on the roof; the excess produced electric energy is fed in the local grid. By the way this environmental friendly solution is not too well suitable for battery charging as the NiCad batteries are charged in two, six hours cycles, between 04:00 a.m. and 9:00 p.m. and the sun shines not all the time. The facility is also a certified battery recycling center (9 MT recycled in 2017).
Safety in the workshop is extremely important, as during the charging process of the lead acid and NiCad batteries gases are produced. All around the shop I could spot H2, O2, and CO monitors. The whole battery shop is kept at 66 F and more than 150 sprinkler heads are attached to a 122,000-gallon water tank (460 m³). The workshop has the capacity of 90 batteries at any time with 49 chargers.
The workshop is divided in three separated units. The biggest one handles the traditional NiCad batteries with attached the Sealed Lead Acid (SLA) batteries unit, and the physically separated smaller room for Lithium-ion batteries. Here it is obvious that the workshop was designed by the staff for the staff - not common these days.
Lithium-ion
The Lithium-ion battery compartment is the smaller one but the Satair people are proud of it. It consists of a separated, windowless room dominated by a huge metal made locker and of an automatic battery care test unit from Saft. David Bigley told me that Satair does not work on this battery type. The battery is only being tested, charged and kept in storage. The unit I could see was from the A350 and I was shown the test procedure, the battery itself is "hidden" in a massive aluminum closed container and is fully integrated - the battery cells and the electronics are not serviceable in the shop only by the manufacturer. This integration makes the test and charging process easy as all the work - after the battery is being hooked up by thick copper cables to the Saft device - is being automatically performed. I witnessed a battery status test which was performed in some 10 minutes; the result (and the eventual problems) is displayed on the device screen. That' all what can be done.
NiCad
The NiCad shop is much larger than the Li-Ion shop and it makes with a wall full of windows a different, pleasant impression and working atmosphere. On a regular working day this shop was really busy; batteries were pushed to their inspection and charging station almost in a minutes pace. Along the shop I could see some 50 battery chargers. On the shop end there was a separated room for SLA batteries. I had an impression that Satair employees love their NiCads and the inspection, repair, overhaul, and charging seemed to make a part of an elegant choreography. We have to have on our mind that some of them weigh around 120 pounds. Satair is handling all kind of NiCad batteries and they vary in size and respectively in capacity and weight and they have different overhaul requirements.
NiCads are overhauled after 1,000 to 2,500 hours depending on their use and aircraft; typically older Airbus A320-family aircraft batteries are overhauled after 1,000 hours, Boeing 737 batteries after 2,000 hours, and those on board of 747 after 2,500 hours. Those overhaul intervals are not really fixed as the batteries health is heavily influenced by their use, number of cycles, and many other factors. Older aircraft batteries are less used ("stressed") as in new MEA (More Electric Aircraft) where a larger number of systems rely on the electric power. Some batteries return to the Satair facility several times a year depending on their use.
The battery that comes to the shop is first subject to a 60-minute capacity test which is then followed by a 12-hour pause. If the battery passes this test, it will then be charged for six hours and in the final phase of this process the electrolyte level is being closely checked and possibly corrected. If the tested battery does not pass the initial test, the trouble shooting is initiated, which may end with a change of a single cell or with the complete overhaul where all cells can be exchanged and the temperature pick up is checked or exchanged. Because the content of each battery-box can be exchanged several times in the battery life, some of them carry the date of manufacture from the end of the 1990s.
Products stored in warehouse are sent to all corners of the globe, and around the corner to the Heathrow airport.
A closing tip
Before leaving I asked David Bigley the following question: "What suggestion do you have to user and mechanics in the field?" I expected a longer, difficult to understand recommendation but he surprised me, saying, "Please turn off the equipment prior to leaving the aircraft. And please, please do not discharge your batteries completely."
About the Author
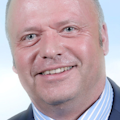
Marino Boric
Marino Boric graduated with a university degree as an aeronautic engineer, and acquired degrees in business development/trade and commerce and in journalism. He is a civil and military pilot and has built experimental aircraft. As a journalist, he specializes in aviation and propulsion and travels worldwide, flight-testing UL, LSA, Experimental, and certified aircraft. He is writing for U.S., European, and Chinese media companies.