Supporting the Industry on Maintenance Investigation: Boeing MEDA in the Last Decade
Maintenance Error Decision Aid (MEDA) is a structured process for investigating events caused by maintenance technicians and inspectors. As a jointed effort by Boeing maintenance human factors experts and industry in the early 1990s, MEDA was intended to help airlines shift from blaming maintenance personnel for making errors to systematically investigating and understanding why the errors had occurred. MEDA offers an organization means to learn from its mistakes. Since its inception in 1995, MEDA has been adopted by more than 800 organizations around the world. The MEDA process has set the standard worldwide for maintenance event investigation and has been recognized for its significant contribution to aviation safety (e.g., The Sir Frank Whittle Safety Award by the International Federation of Airworthiness).
How Does MEDA Work?
MEDA is based on the philosophy that errors and violations result from a series of contributing factors (anything that can affect how the mechanic does his/her job) in maintenance operations, such as misleading or incorrect information, design issues, inadequate communication, time pressure, and so on. Most of them (as high as 90 percent) are under management’s direct control. Once they are identified, the organization can take actions to eliminate those contributing factors to prevent similar events from happening again.
Visually, this is how the MEDA process works. It’s a reactive process. The event occurred, a maintenance organization has to decide the event was caused by mechanic/inspector performance, and then find the mechanic/inspector who did the work or who observed the work being done to interview them. The investigator typically knows what the system failures are before he/she conducts the interview. For example, mechanic did not connect the hose correctly and the system started leaking. There was a bolt missing on the side of the pump. Through the interview the investigator talks to technicians to get the contributing factors and their ideas for process improvement. Some follow-up interviews may be needed. For example, mechanic said “I went to the store but a part was not available. There is another part that was compatible, so I used it. Later on I found that the part was not compatible.” So in this situation, the investigator may want to go to the store to find out how they determine the part compatibility. Maintenance event database is helpful for identifying and tracking patterns. Sometimes MEDA investigations reveal problems that need to be fixed right away. Sometimes it is reasonable to wait and see if a common theme will emerge out of multiple MEDA investigations, especially if the corrective action is a costly investment. It is also important to let the employees know what the company is doing with MEDA investigation findings. System improvements through MEDA will be the best promotion to foster trust and willingness to participate in any future MEDA investigations.
Key MEDA References
There are two main MEDA references:
(1) MEDA Results Form — used during the investigation, and also a template for writing an investigation report
(2) 70-page-long MEDA User’s Guide — a “how-to” manual on carrying out a MEDA investigation.
The main references complemented by practice scenarios and training, are updated on a regular basis.
The most important section in the MEDA Results Form is a checklist of 10 categories of contribution factors, which explain why errors and violations occur and result in system failures, which eventually resulted in an event.
Most of the causal relationships discovered in event investigations are probabilistic in nature (e.g., existence of contributing factors increases the likelihood of an error). Six rules of causation help to guide MEDA investigators to collect more, better data and be more effective in authoring investigator reports:
1. Each human error must have a preceding cause.
2. Each procedural deviation (violation) must have a preceding cause.
3. Causal statements must clearly show the “cause and effect” relationship.
4. Negative descriptors (such as poorly or inadequate) may not be used in causal statements.
5. Failure to act is only causal when there is a pre-existing duty to act.
6. Causal searches must look beyond that which is within the control of the investigator.
MEDA Investigators Apply Cognitive Interviewing Techniques
The primary method to gather data in MEDA investigation is through conducting interviews with technicians or inspectors who were involved in the event. MEDA investigators are trained to apply some specific techniques to help the person being interviewed to remember and communicate while following a structured process during the interview.
An Important Tool in a Safety Management System
Safety management systems (SMS) at airlines and maintenance organizations around the world have advanced rapidly in the past decade. Risk management, one major component of an SMS, requires that safety of flight hazards be identified, that the hazards be assessed for risk, and that unacceptable risk be mitigated to acceptable levels. Among the three approaches for identifying hazards (reactive, proactive, and predictive), event investigation is mainly responsible for identifying and communicating human performance issues within an organization. Boeing MEDA has been an important tool in the SMS reactive hazard identification process. It helps an organization systematically determine the hazards or contributing factors to events, and, based on these findings, allows the organization to develop and monitor a comprehensive fix.
A Connection to Managing Human Behaviors in a Just Culture
Both errors and violations can contribute to maintenance events. They often occur together to produce an unwanted outcome. MEDA investigators are trained to recognize errors, violations, and different types of violations (routine, situational, or exceptional), and investigate the preceding cause(s) to the errors and violations. In the next revision of MEDA Results Form, a new section will be added to help to document errors and different types of violations, which require different mitigation strategies. This new addition will offer a connection to how different human behaviors should be managed within a Just Culture:
1. Human errors – “To err is human …”
Human errors should be managed through consoling and other actions such as changes in processes, procedures, training, design, and environment. Upon close examination, repetitive human errors may warrant punitive actions.
2. At-risk behaviors (routine and situational violations) – “To drift is human …”
At-risk behaviors should be managed through coaching and the following:
• Removing incentives for at-risk behaviors
• Creating incentives for healthy behaviors
• Increasing situation awareness
Upon close examination, repetitive situational violations may warrant punitive actions.
3. (Occasional) Reckless behavior
Accountability rests wholly with the individual who chooses the reckless act.
Harness the Power of Visual Communication
A map or a diagram offers a level of information density that words and sentences alone cannot offer. For example, the amount of information that is captured and easily communicated on a single street map. Traditional written investigation reports do not illustrate causal relationships well. In the past few years, Boeing has been recommending a MEDA best practice – upon completion of an investigation, use a diagram to visualize and document causal relationships discovered in the investigation and produce “the big picture view.” The diagram is also a great communication tool and helps to preserve the learning through the investigation.
In the next revision of MEDA Results Form, a new section will be added to offer a template for constructing the causal relationships discovered in the MEDA investigation.
MEDA Best Practices
Several factors contribute to MEDA’s wide adoption and acceptance:
· The Boeing Company has been offering continuous and consistent support. For instance, between January 2012 and March 2018, 75 sessions of MEDA investigator workshops were offered to Boeing customers and maintenance organizations around the world, which trained and retrained over 2,300 investigators.
· MEDA is a systematic and comprehensive yet highly customizable investigative process/tool; it can be easily integrated with other existing investigative programs.
· MEDA helps a maintenance organization to fulfill the “event investigation” requirement by national aviation authorities for maintenance human factors program.
· Airlines and other maintenance organizations are not required to share data.
· MEDA is supported/endorsed by labor unions/groups.
Boeing works closely with safety programs with Lufthansa Technik (LHT) and provided MEDA support to seven different LHT sites and Lufthansa Airlines around the world between April 2013 and March 2018.
How Lufthansa Technik Uses MEDA within Its SMS
At the beginning of 2000, Lufthansa Technik (LHT) started to use the MEDA concept for error management within line maintenance, which enabled LHT to support transparent analysis and error solutions, and consequently created conditions for sustainable improvement. Soon after, LHT became interested in making this standard usable for the entire product range of the LHT Group. In addition to the standardized risk assessment, the collection of error and cause categories helps to identify systematic issues. So it was natural that the MEDA methodology was integrated as a part of the LHT’s SMS.
Due to the variety of products (e.g., line, base, shop maintenance), it was necessary to adapt the MEDA concept to the needs of LHT. In the MEDA concept the error categories are focused on maintenance system failure (Section III in the MEDA Results Form). This is perfectly designed for the needs of line maintenance and was easily transferred to base maintenance. For the component and engine service, however, it was necessary to expand the categorization. The same applied to the requirements of the design and production organization of LHT. There are similar considerations in the industry today that have led to the discussion about Component Error Decision Aid as a counterpart to MEDA. However, since LHT conducts the investigations worldwide using a standard IT system called q/star, the error categories were simply extended to meet LHT specific needs. For this reason LHT uses the term “error categories” instead of “maintenance system failure.”
To make specific extensions of MEDA concept transparent, the LHT investigation process in q/star is called MEDAplus, which is considered an important tool in its quality/safety toolbox.
LHT experience in collecting investigation data has shown that the categorization of contributing factors or cause categories (as LHT named it), is commonly applicable. When combined with the product or process data, the categories are informative, allow quick detection of systematic vulnerabilities, and thus help to ensure better product and process stability (see Figure 2). On this basis, appropriate significant improvements can then be demonstrated within a reasonable period of time.
Dr. Maggie J. Ma is a Certified Human Factors Professional (CHFP) who specializes in maintenance human factors. She is an associate technical fellow at Boeing where she enjoys supporting Boeing customers and other maintenance organizations on safety programs such as MEDA and Maintenance Line Operations Safety Assessment (M-LOSA) around the world.
Ms. Anja Koschinski is head of quality monitoring and reporting at Lufthansa Technik AG, Ms. Koschinski has a diploma in business education and is a Certified Systemic Consultant. She is responsible for the central processes of the LHT Group around SMS as well as the associated IT applications.
About the Author
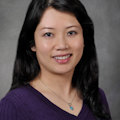
Maggie J. Ma
Associate Technical Fellow, Boeing
Maggie Ma is a Certified Human Factors Professional (CHFP) who specializes in maintenance human factors, and a Boeing Technical Fellow. Maggie received her Ph.D. in Industrial Engineering/Human Factors Engineering in 2005 from State University of New York at Buffalo. Maggie has 20 years of experience in conducting applied human factors research to improve aviation safety through developing various safety programs (e.g., event investigation, training, self-reporting, and observation of normal operations). She has authored over 70 technical publications, has chaired technical sessions, and is frequently a speaker at aviation safety conferences and workshops. She has worked closely with airlines, manufacturers, maintenance organizations, ground service providers, and regulatory agencies around the world.
Maggie joined the Boeing Company in January 2012. Her primary responsibilities include providing implementation support to customer airlines, maintenance organizations, and internal customers on a wide array of safety processes/programs, e.g., the Maintenance Event Decision Aid (MEDA) process, the Ramp Event Decision Aid process, Maintenance Human Factors training, a Safety Management System, Maintenance Line Operations Safety Assessment (LOSA), and Ramp LOSA. She also leads several Boeing initiatives and innovation projects. Maggie and her former lead, Dr. Bill Rankin received the Engineering Team of the Year Award for Boeing Commercial Aviation Services in February 2013. Maggie received the Boeing Service Culture Excellence Award in June 2018.
Previously, Maggie was a faculty member of Aviation Science at Saint Louis University and also worked as a senior usability consultant at Perficient Inc. She was an Amelia Earhart Fellow 2004-05.
Education
- Bachelor of Science (1999), Engineering Management, Beijing University of Technology.
- Master of Science (2002), Industrial Engineering/ Human Factors Engineering, SUNY-Buffalo.
- Ph.D. (2005), Industrial Engineering/ Human Factors Engineering, SUNY-Buffalo.
- Certificate (2019), Psychology of Leadership, Cornell University.
Professional Affiliation
- Human Factors and Ergonomics Society (HFES)
- Board of Certification in Professional Ergonomics: certified Human Factors Professional (CHFP)
- Boeing Community of Excellence in Human Engineering
- International Civil Aviation Organization (ICAO) Human Performance Task Force
- European Union Aviation Safety Agency (EASA) Human Factors Collaborative Analysis Group (HF CAG)
- FAA’s Research, Engineering, and Development Human Factors Subcommittee
- Airlines for America (A4A) Maintenance Safety Committee
- UK Royal Aeronautical Society Human Factors Group: Engineering (RAeS HFG:E) (corresponding member)