When an aircraft on ground (AOG) experience occurs, suddenly an operator must handle an unforeseen situation with normally very high stakes. Over the years the providers of aircraft maintenance, repair and overhaul (MRO) services have developed dedicated packages of services for mobile response maintenance that serve for a return to normal operations. In this article we have reached out to industry experts to discuss best practices and latest trends in the domain of mobile response maintenance.
Need for Mobile Response Maintenance
According to FEAM, how often maintenance that goes beyond the capabilities of line maintenance providers is needed depends very much on the maintenance providers and their capabilities.
“In 2021 we responded to our customers' AOG requests 385 times. FEAM AOG performed avionics repairs, structural repairs, rigged flight controls, resealed main landing gear, changed flight controls and performed engine changes,” says FEAM.
Jörg Speri, Senior Director Network Sales & Customer Service - Aircraft Maintenance Services at Lufthansa Technik, observes that AOGs, by their very nature, cannot be planned.
“This is also why a broad range of events can occur, such as structural defects, defects on engines or landing gears, and other system failures. Some weeks it happens nearly every day and then there are times when we hardly see any request for support. Some of these events are of such nature that they require specific tooling and infrastructure that normally go beyond a line maintenance provider’s capability,” he says. “This is where the strength of our recently established ‘Aircraft Maintenance Services’ product segment – which is a merger of former line- and base maintenance segments – comes into play. Whenever the limits of classic line maintenance are reached, we can provide a solution out of one hand.”
Best Practices
There are three main practices to getting mobile response maintenance services up to speed for AOGs, according to FEAM.
“One is developing a team that is adaptable to both the customers’ needs and the industry. The second is communication with all the parties that make up a speedy AOG recovery, while the third is logistics of moving parts, tooling, and manpower to and from the AOG”, says FEAM.
According to Speri, one main principle to observe is to “expect the unexpected.”
“Solutions range from standby teams with small jets that are available 24/7 and can be deployed quickly, to structural experts on hand at various locations near our customers. Our 24/7 AOG desk is the mastermind behind it all and can quickly decide which resources are needed and deploy them accordingly,” he says. “Our experts at the AOG desk also have the expertise to assess damage at first glance based on a few photos or a few lines description. The ideal basis for this operation is provided by our network approach in Europe.”
Organizational Set-Up
A specific organizational set-up is needed for an MRO to deliver mobile response maintenance services. “One needs a combination of fast deployable units on site, proper tooling, infrastructure, as well as a mastermind steering unit with the necessary know-how”, says Speri.
A top-down approach of support to the AOG group is also needed, according to FEAM.
“AOG maintenance is never the same scenario. Every event needs a custom-built approach. The key players are the director of AOG maintenance, the operational control center, the structures department head, the avionics department head, the A&P technician department head, and the quality department head,” says FEAM. “All these team members are critical to the way they support each other along with the AOG team performing the repair.”
Dr. Mario Pierobon provides solutions in the areas of documentation, training and consulting to organizations operating in safety sensitive industries. He has conducted a doctoral research project investigating aircraft ground handling safety. He may be reached at [email protected].
About the Author
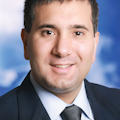
Mario Pierobon
Dr. Mario Pierobon provides solutions in the areas of documentation, training and consulting to organizations operating in safety-sensitive industries. He has conducted a doctoral research project investigating aircraft ground handling safety. He may be reached at [email protected].