A Deeper Look: Aircraft Engine Inspection Techniques Using Ultra-Thin Video Borescopes
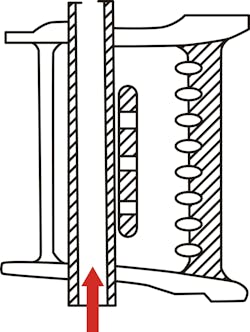
Borescope inspections inside aero engines are essential for safe and reliable operation of aircraft. However, to maintain the integrity of aero engines used in harsh environments, defects cannot be overlooked—even in narrow areas that are difficult to access with the outer diameter of a typical borescope (6 mm or 4 mm). For example, borescope inspections are required in aircraft gearbox housings, fuel lines, and the narrow cooling channels inside turbine blades. An ultra-thin video borescope with an outer diameter of about 2 mm is an effective tool for inspecting these extremely narrow areas.
In this article, we introduce aircraft engine inspection techniques for using an ultra-thin video borescope, highlighting key points to keep in mind.
Challenges of Inspecting Cooling Channels Inside Aircraft Turbine Blades
Cooling of turbines, combustors, and other high-temperature parts of an aircraft engine is important to improve its performance. One of the leading cooling technologies for turbines is the design of cooling channels in the turbine blades. This is done by internally convecting cooling air to the turbine blades to cool the moving and static blades (hereafter referred to as turbine blades) and to help ensure their durability. During engine operation, water and oil may flow into this cooling distribution channel in addition to cooling air.
If burrs or clogs occur in the cooling channels during the turbine blade manufacturing process, or if the cooling channels become blocked by water or oil during engine operation, the turbine blades cannot be sufficiently cooled. In the worst case, the turbine blades could crack or break, causing a serious accident.
Techniques and Tips Using Ultra-Thin Video Borescopes in Cooling Channel Inspection
The cooling channels inside aircraft turbine blades are 1 mm to 3 mm at the narrowest point. To find defects in the cooling channels, operators often observe the inside of turbine blades using an ultra-thin video borescope with an outer diameter of about 2 mm.
Figure 1 shows a cross-sectional view of a static blade and its cooling flow path. When inspecting with an ultra-thin video borescope, the operator inserts the scope into the cooling channel from the direction illustrated and observes the interior for burrs or clogs.
For internal observation of the cooling channels in turbine blades, we recommend an ultra-thin video borescope with excellent curvature capabilities that can be inserted into the gaps between their bends and branches.
Some ultra-thin video borescopes with an outer diameter of about 2 mm have curvature capabilities, and these can follow the bends and branches of cooling channels. This scope flexibility enables high defect detection capability in the inspection of cooling channels in turbine blades.
On the other hand, since the outer diameter of the insertion portion of an ultra-thin video borescope is smaller than that of a standard borescope, the outer braid of the scope may rub against the inner wall or contact the edge when inserted into the cooling channels in the turbine blades, resulting in possible damage.
To prepare for these cases, it is essential to select an ultra-thin video borescope with a highly durable articulation structure, as the articulation portion of the insertion tube is the part most likely to be subjected to stress during examination. We also recommend an ultra-thin video borescope that can be fitted with a protection braid that protects the exterior of the scope and increases its durability.
Techniques and Tips Using Ultra-Thin Video Borescopes in Aircraft Gearbox Housing Inspection
In the internal inspection of aircraft gearbox housings, the internal passageway to be inspected is about 5 mm in diameter at the narrowest point and may have a shape such as an S-shape. For these inspections, operators often detect defects by observing the inside of the housing with an ultra-thin video borescope of about 2 mm in outer diameter.
The housing of a gearbox may have a complicated internal passageway, which may be unable to pass through without forcefully twisting and inserting an ultra-thin video borescope of about 2 mm in outer diameter. Therefore, it is preferable to select a video borescope with a short distal end length and sufficient durability. Especially in the case of an ultra-thin video borescope with articulation, it is important to select a scope with a durable structure because the curved part is one of the most vulnerable parts in use.
Also, internal passageways of the housing can vary from narrow areas with a diameter of about 5 mm to wide areas. To avoid missing any defects, select an ultra-thin video borescope with a wide 120-degree viewing angle and a large adjustment range for brightness settings. This lets the operator observe images of a large area on a large screen monitor while adjusting the brightness.
Challenges in Aircraft Fuel Line Inspection
Aircraft fuel line inspections are an important part of the work performed to help ensure the safety and performance of the aircraft. Fuel lines are components such as pipes that control the flow of fuel from the fuel tank to the engine. Abnormalities such as fuel leakage or clogs due to foreign matter, corrosion, or oxidation at the brazed joints can lead to serious accidents.
Techniques and Tips Using Ultra-Thin Video Borescopes in Aircraft Fuel Line Inspection
Borescope inspection of aircraft fuel piping can identify internal dirt, rust, cracks, and other abnormalities. Similar to the inspection of cooling channels and gearbox housings, operators often find defects in the internal inspection of fuel lines using an ultra-thin video borescope of about 2 mm in outer diameter.
There are many different types of fuel piping, ranging from complex shapes that include very narrow bends at right angles to simple shapes with thin straight lines.
Flexible-type ultra-thin video borescopes are used for the most complicated fuel piping. However, because there are many very narrow bends, some scopes cannot pass through without the operator delicately curving and twisting it. For this reason, it is preferable to select a video borescope that is sufficiently durable. In particular, the articulation section of the scope is the part that is most vulnerable to stress during examination, so it is essential to select a video borescope with a highly durable curved structure.
On the other hand, for aircraft fuel lines with thin, straight, and simple shapes, rigid-type video borescopes can also be selected. Especially in the manufacturing process, when a shorter inspection time is required, rigid-type video borescopes can contribute to a shorter time. Therefore, it is recommended to adopt an ultra-thin video borescope that enables the selection of both flexible and rigid scopes in the same system for various applications.
In aircraft engine inspections, ultra-thin video borescopes are effective for inspecting various areas, such as gearbox housings, fuel lines, and the cooling channels inside turbine blades. It enables visual inspection of narrow areas that are difficult to access with the outer diameter of a typical borescope (6 mm or 4 mm), contributing to improved engine safety.
About the Author
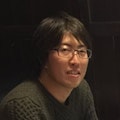
Masateru Ito
Marketing Specialist, Remote Visual Inspection
Masateru Ito joined Evident in 2008 with an intellectual property background in the solar energy system and electronic components industry. He has held various positions supporting Evident’s remote visual inspection (RVI) solutions in the product management and marketing field.