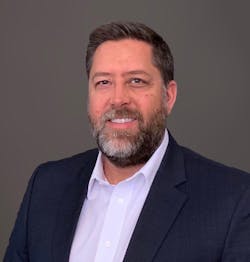
As with the aircraft they support, ground support equipment (GSE) has traditionally been powered by internal combustion (IC) engines. But burning diesel, gas or propane results in carbon emissions that can have a negative effect on the global environment.
The use of IC engines in GSE is changing, as more airlines are choosing to electrify their GSE fleets.
One of the primary drivers of fleet electrification has been the need to comply with government agency regulations around emissions. IC technology has improved over the years to reduce the level of emissions, however, electric GSE is emission-free.
The California Air Resources Board will consider a measure later this year that will promote “the development and use of zero-emission airport ground support equipment (airport GSE)” as part of a strategy to help reduce emissions at several California airports.
Starting in September, airlines at Salt Lake City International Airport (SLC), “will transition to electric ground support equipment reducing 8,000 metric tons of greenhouse gases (GHG) annually.”
While the elimination of emissions is an important consideration for making the switch to electric GSE, there are other benefits.
Electric GSE
Along with the elimination of emissions, electric GSE also helps do away with something else – noise. Compared to IC-powered equipment, electric GSE is much quieter. In a noisy environment, like the ramp at an airport, this can be a big plus for equipment operators.
Electric GSE can also be easier to maintain, as the drive system uses fewer moving parts that are subject to wear over time. Simplifying the maintenance routine can lead to higher GSE fleet availability, which is critical for equipment that supports multi-million-dollar aircraft. After all, a ground service provider wouldn’t want to delay a departure because a baggage tractor is out of service for maintenance.
The typical usage patterns for GSE are also a good fit for battery power. Frequent starts and stops don’t strain an electric powertrain the same way it does an internal combustion engine with a lubrication system, since much of the wear occurs during start-up.
Operators can benefit from using electric GSE as well. One of the most appreciated aspects of using electric GSE is the “inching device.” This feature allows operators to “stand behind luggage tugs and inch it into the hitch of the luggage trailer” ensuring they are in a safe position where they can see the hitch connection.
Lithium-ion Battery Benefits
Electric GSE offers some significant advantages over internal combustion-powered equipment. There are even more benefits to using lithium-ion batteries instead of lead acid batteries to power the equipment.
While it is true that lithium-ion batteries typically come with a higher price tag for the initial purchase, that price can be offset by a longer service life. Modern lithium-ion batteries for GSE can perform for 2,000-3,000 cycles and are often backed by warranty.
Lithium-ion batteries can remain in the equipment while being charged, and they can be “opportunity charged,” meaning an operator can plug it into the charger for 15 or 30 minutes while on break. In comparison, some lead acid batteries don’t support opportunity charging without damaging the battery’s capacity and may require removal from the equipment for charging and cooling.
As mentioned previously, electric GSE has lower maintenance requirements than comparable equipment powered by diesel or gas. Lithium-ion batteries benefit from the design of sealed cells which means there is no requirement to adjust the electrolyte levels as must be done with lead acid batteries.
Lithium-ion batteries also have a higher level of energy efficiency – as much as 50 percent more energy efficient, depending on the specific battery model. That means that more of the energy coming through the charger is available to do work, such as pulling a train of baggage carts.
One downside of using batteries is that their performance level decreases with colder temperatures. Most lithium-ion battery manufacturers offer integrated heaters as an option to ensure that the battery packs are kept at the optimum temperature range. If you have ever been to O’Hare in January, you’ll appreciate the value of a heater to keep the GSE batteries warm.
Making the Transition to Lithium-ion
If interested in implementing lithium-ion battery technology, the first step is to assess the condition of the current fleet of GSE. A good starting point is to consider the following questions:
- Do you have equipment that is near the end of its operating life that would be replaced?
- Do you have existing electric GSE that could easily accept a replacement lithium-ion battery pack?
Once you have answered the first two questions, it makes sense to evaluate the specifics of the fleet operations:
- How many hours per day is the GSE being used?
- What are the battery charging infrastructure requirements?
- What are the environmental/regulatory requirements? (not just today, but in the future)
A detailed return on investment (ROI) calculation can provide insight into the economic benefits of making the conversion to a different power source, whether it is lithium-ion or lead acid. To get a true understanding of the total cost of ownership, do not forget to include items like maintenance costs, replacement battery costs and refueling/charging infrastructure costs.
The demand for zero-emission, high performance GSE is on the rise. The transition from IC engines to lithium-ion batteries is becoming more common because of the significant benefits that lithium-ion provides.
As government regulations on emissions put GSE fleet electrification into the spotlight, now may be the time to start thinking about how to make the switch to a higher performance lithium-ion battery.
Justin Forbes is the director of business development at Flux Power, where he is responsible for developing marketing and customer acquisition initiatives, along with creating new business growth strategies to increase sales. His prior experience includes marketing and product management roles at several industrial companies. He graduated with a degree in Mechanical Engineering from UC- San Diego, and earned his MBA from Duke University.
About the Author
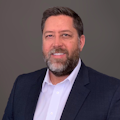
Justin Forbes
Justin Forbes is the director of business development at Flux Power, where he is responsible for developing marketing and customer acquisition initiatives, along with creating new business growth strategies to increase sales. His prior experience includes marketing and product management roles at several industrial companies. He graduated with a degree in Mechanical Engineering from UC-San Diego, and earned his MBA from Duke University.