Additive Manufacturing: A Giant Leap for the Aviation Industry?
Additive manufacturing, also known as 3D-printing, has captured the aviation industry's imagination, but even as the first parts make their way to the actual aircraft, the technological possibilities are only just beginning to be realized. As manufacturers experiment with new materials and optimized designs made possible by 3-D printing, the potential scale of the revolution in manufacturing is yet to be fully perceived.
Slowly but surely 3D printing is taking over the process of aircraft manufacturing. For instance, Pratt & Whitney is using the technique in making blades and vanes for compressors inside jet engines. Honeywell exploits it to build heat exchangers and metal brackets. Boeing already makes about 300 different smaller aircraft parts using 3D printing, including ducts that carry cool air to electronic equipment.
“One of the attractions of printing parts is that it saves materials. Instead of machining components from solid billets of metal, in which much of the materials may be cut away, only the ones that are needed to shape the part are used. Therefore, it can be safely said that additive manufacturing could help produce any complex parts without typical waste. In addition, printed parts can be made lighter which promises substantial fuel savings,” commented Zilvinas Sadauskas, the CEO of Locatory.com. “Moreover, the technology provides the possibility to re-localize manufacturing of many items, as printers can be set up almost anywhere thus eliminating the costs of shipping and warehousing. So it’s not surprising that OEMs want to implement this technology throughout their supply base.”
Multiple tests have shown that replacing a cast-steel nacelle hinge bracket on an Airbus A320 with an additively manufactured titanium part can cut down the raw-material consumption by 75%, thus saving 10 kg per shipset, reducing the energy and emissions in production. As for the cost-savings, after successfully using 3D-printed metal components on board of its Tornado aircraft, the Royal Air Force has reported that using this technology could reduce the maintenance and service bill by over $1.9 million over the next four years. However, according to the industry experts, this technology is still far from being able to really revolutionize the way that the things are done in the industry.
“The currently produced 3D-printed polymer parts are low-strength and can be used for ducting but not load-carrying components only. Moreover, despite the fact that the technology doesn't require many workers, it does require high-skilled professionals to operate or make machines and develop the appropriate computer code,” shares Zilvinas Sadauskas, the CEO of Locatory.com.
According to Z.Sadauskas, it’s still far from the point where the industry can make giant steps. For all its advantages, 3-D printing is limited by high costs for the special types of materials needed. The technology also tends to be slower for high-volume production and thus doesn’t offer enough capacity to handle the industry’s production needs. “Another obstacle is the lack of industry-recognized standards for the materials, processes and testing methods. Moreover, there is still the lack of a supply chain for this kind of work to consider. Therefore, despite the magnitude of the recent hype, the technology will have to get much faster and cheaper before it can account for a sizable chunk of industrial production,” shares the CEO of Locatory.com.
About the Author
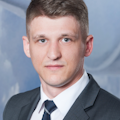