Return to Master Builder – Design-Build Solution Benefits Complex Aviation Projects
About 5,000 years ago, the ancient master builder, a design-build professional, was instrumental in the building structures like the pyramids of Egypt, the Parthenon and the Theatre of Dionysus. Many of the world’s most enduring structures were built by the master builder. Today’s design-build delivery method for large complex infrastructure projects continues to gain acceptance as a preferred solution.
To be ready for the expected doubling of passenger traffic at San Diego International Airport in the next two decades, the San Diego County Regional Airport Authority took an important step toward its future. Knowing the airport’s longevity and the region’s economic vitality depended on the airport’s ability to adequately meet imminent demand, the Authority embarked upon the $1 billion San Diego International Terminal 2 West Building, Airside Expansion, and Landside program — the largest construction project in the airport’s history. The Authority awarded HNTB and a joint venture of Turner Construction, PCL and Flatiron the design-build terminal development contract solely based on qualifications and approach.
HNTB served as lead architect of record and engineer for the new Terminal expansion and airside infrastructure. During the completion of the design, HNTB was integrated with the construction joint venture and continued as part of the design-build team, remaining on-site in a co-located office for more than two years to support construction efforts.
Challenges and Opportunities
Delivering the historic program involved not only facing challenges but overcoming each one with unprecedented collaboration:
- Design-build delivery. As the Authority’s first design-build contract, fast-tracking the project made sense: it would save costs, lower the budget, shorten the time passengers would be inconvenienced and return revenue faster. Yet the accelerated schedule meant the team would need to deliver four major projects in four years.
- A 526,000 square-foot expansion to the existing terminal building, nearly doubling in size
- An airside expansion of 1.3 million square feet
- A larger central utility plant to serve the new expansion
- A fully integrated in-line checked baggage inspection system to accommodate new TSA requirements for the entire terminal
• Limited site area. The project would be built inside the busiest single-runway airport in the country, locked into place by a bay and a highway. Expansion would require innovative, creative approaches.
• Implementing old with new. Requirements called for the 12-year-old terminal building to remain fully operational during construction and for the expansion to seamlessly integrate with the existing building.
The Collaborative Approach
It would take all the partners pooling their best tools, most effective strategies and personal commitments to ensure a successful program. As a first-time design-build project owner, the Authority exhibited particular savvy by instituting several policies intended to effectively launch the program.
Understanding communication and collaboration are keys to successful design-build projects, the design-build team was co-located with the airport’s staff, which facilitated communication, problem solving and expedited decision making. The design-build team also collaborated virtually. Members compiled all design review comments in a Sharepoint database using Bluebeam Review, which made the review process immensely easier and more efficient; they then reviewed that information with the key stakeholders on a monthly basis in the GreenBuild Operations Committee meetings.
Building information modeling was another valuable tool. Autodesk Revit BIM software allowed HNTB to build the project virtually before physical construction began. The team analyzed impacts, worked out conflicts and reduced uncertainty before the groundbreaking took place.
Using BIM 4-D (cost) and BIM 5-D (scheduling), the owner knew the project would meet its time and budget requirements while the contractor could be certain of its constructability. Once the project was completed, BIM served as an as-built model for facilities management to efficiently maintain the building and facilitate future expansion.
LiDAR (light detection and ranging) scans paired with BIM provided extra insurance. HNTB took scans of key systems and assemblies in the existing building and created building information models of every discipline — from the architecture, structure and HVAC, to complex baggage handling systems and more. In the process, the team proactively resolved more than 1,600 coordination issues and identified thousands of clashes, creating a significant savings by drastically limiting on-site changes.
Using both LiDAR and BIM, the team phased construction in a way to minimize disruption to travelers. What’s more, BIM helped the design-build team identify a discreet way to route all building systems within the transition space, addressing the Authority’s request for seamless integration of old and new.
The Results
The design-build delivery method and the collaborative environment it promoted were critical elements to the program’s overall success.
Growth: The expansion extends the life of the 85-year-old airport and dramatically improves airport capacity and air travel for passengers. A passenger favorite, Sunset Cove, is an expansive dining and retail court, gathering area and architectural showpiece. The cove features a dramatic 50-foot-tall curtain of windows, pitched at a 14-degree angle. The glass wall offers superb views of airside activity and San Diego’s famous sunsets. There is also free Wi-Fi, electrical outlets in the two world-class airline departure lounges on the mezzanine, dynamic signs for passenger wayfinding, and a state-of-the-art consolidated passenger screening security checkpoint that has reduced wait times by 15 percent.
Under budget: Guaranteed maximum price contracts set the tone for an efficient and cost-contained approach. Still, when scope increased, the design-build team managed to bring overall costs under budget by 10 percent due to HNTB’s what-if scenarios, innovative design and continual cost-analysis collaboration with the contractor.
On time: The Terminal 2 West Building and Airside Expansion program was completed in August 2013 and instantly became a role model for how future terminals are designed, built and operated.
Design-build is a method of turn-key project delivery – one contract with one entity, with everyone working collaboratively starting from initial design through program completion. The integrated design-build team for San Diego International Airport, much like the ancient master builders, serves as an excellent example of the types of successes a design-build delivery process can achieve.
Peter Aarons is West Division aviation director and associate vice president for HNTB Corporation. He has more than 25 years of experience in planning, development, design, program and project management, and construction for airports. Contact him at [email protected].
About the Author
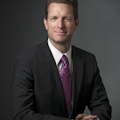