The FedEx Express maintenance facilities in Indianapolis (IND) are just like any other jet home, except for a few things. Well, a lot of things; but the principles are the same, and the sheer scale of the operation and the airplanes mandates efficiencies and innovation that can scale down, all the way to the one-man shop.
Most of the FedEx Express fleet of MD-10 and -11 freighters, Airbus 300 and 310, and Boeing 757, 767, and 777 can receive light maintenance and the occasional repair; B-checks are routinely performed on all but the MD-11 and triple-sevens. Michael Sanford, senior manager, field line maintenance, IND Region, runs the East side hangar, where they do the quick turnarounds and routine maintenance (up to and including gear changeouts); Garry Lyons, senior manager, IND hangar maintenance, runs the West side, where the crew performs B-checks, repairs, and the occasional manufacture of parts. “Some of the MD-10 parts are becoming scarce,” he notes.
With well over 100 mechanics, six managers, and a bit of administration on the East side and 250 on the West, the roughly 20 flights a day (and 65 per night) get a lot of attention; a typical 757 B-check takes 24 hours. (The MD models take longer; the 767, less time.) Since the aircraft are of varying ages and sport varied equipment, FedEx Express Indy has to be ready for everything. Cockpits are classic or glass; even airframes differ – a handful of the 767s have blended winglets, helpful in their earlier lives as airliners but a mixed bag as freighters that fly heavier and shorter routes. “They’re another 12 feet of wingspan,” notes Sanford, “and sometimes that’s inconvenient on the ground.” [Note: all but five of the current fleet of 767s were delivered as freighters, without winglets.]
The key to efficiency – FedEx Express runs a lean operation, and it doesn’t have a lot of “extra” airplanes or parts – is to assess problems early, be ready with the necessary maintenance, and to stay ahead of trouble. “The moment the airplane is tied down [the nose wheel is tethered until unloading and loading are complete], our crews are doing a walk-around and post-flight inspection. Of course, the flight crew will let us know of anything we’ll need to look at, while still in the air,” says Sanford. There is one more set of eyes: “Our mechanics also drive the tugs.”
The day shift aircraft start arriving around 11 a.m., and they’re out during afternoon rush hour; the night arrivals are times about 12 hours the other side of the clock. Each shift starts with a “daily work release sheet” and brief meeting, where incoming work is noted, with priorities 0-4 (with zero meaning “now!”). The mechanics pick up tools, safety equipment, and supplies; they’re ready as soon as they can get the airplanes.
Not everything at FedEx Express Indy is scalable. The facility has some giant equipment – gantry cranes, huge, tall forklifts, dedicated platforms for tail-mounted engine changes and maintenance (where the parts bins are already located, restocked and ready for the next job). The facility also has a composites shop, complete with air showers and a clean environment; paint and decals are ready any time maintenance or branding calls for them. FedEx is proud of the corporate image, to the point where it contracts crews to wax the planes. It takes 60 man-hours to clean a wide-body; that’s typically six hours, with 10 people.
And here is where the FedEx Express systems start to be a big-scale model for any maintenance shop.
Starting around 2007, “We did time studies,” Lyons says, “and were astounded how much time mechanics spent, just walking back and forth, getting tools, parts, supplies, consumables. Literally miles a day. We want to run a ‘lean’ operation, and we can’t waste time. Plus, it wears them out – for nothing.” So it made a lot of changes. “Like any change, even if it’s in the right direction, it takes a while for them to settle in. In our case, it took about a year; but now, nobody wants to go back [to the old ways].”
Since all mechanics are trained on all the models, each aircraft can be addressed as it needs attention. “We’re always cross-training,” says Sanford. Still, there are specialists: in avionics (17 positions) and structures (27). “The work there is just too specialized.”
How to do more, with less: that’s always a good question. The answer is in finding efficiencies. Having the tools, parts, and consumables ready, at the airplane saves time and shoe leather.
Picking and assigning tools is simplified through color-coding; each type’s special tools follow a code, making spotting them easy. Dedicated carts – for common tasks, like gear changes – mount every tool needed for the job, from floor mats to creepers, to dedicated crow’s foot end wrenches in the right sizes. They also have a small but handy selection of common hardware items – right-size bolts, nuts, and washers; safety wire; O-rings. The idea is that the mechanic will have everything he or she needs to complete the job, without interrupting work to fetch parts or tools. When the job is finished, the cart goes back to its station, where it is restocked.
A common problem in most shops is the use of consumables – shop towels come immediately to mind. When they are in short supply, things get dirty; when they are readily available, they can sometimes migrate to home garages. Some shops require a cloth, for instance, to be turned in to get a new one issued; paper wipes, though, cannot be accounted for this way. And the mechanic waits while the tool room guy does the dispensing. FedEx Express is soon to implement “vending machines” where the mechanic simply swipes his card, and the consumable pops out. No waiting, and over-use is flagged. “We’re going to see how that works,” says Lyons.
“We’ve kitted over 1,500 rotable parts. When a mechanic goes to, say, replace a starter, they don’t have just that starter; they have the clamps, O-rings, tools – everything they need to do the job. It’s made a huge difference in lowering frustration, in saving time,” adds Greg Hall, senior vice president, air safety and business operations, FedEx Express.
The dedicated tool carts have expanded efficiency. They’re shop-built, to specifications derived from the mechanics’ requests. “If they design it, they’ll use it,” says Sanford, who notes that the cart program is extremely popular. “They really help to get the tools, the mechanic, and the plane together, and to keep them together until the job is done.”
Lyons notes that the carts, built to a common design but specialized for the tasks, are not cheap. “They’re actually fairly expensive to build; they’re all steel. We tried PVC and some other approaches, but the good carts do the job.” Then he discovered something else. “Even with top-quality components, the carts need maintenance, too.” So the carts are on a regular preventive maintenance program.
And in some ways, FedEx Express Indy isn’t everyman’s shop. They have sophisticated CNC and manual machine tools, two engineers, and five machinists.
IT is a tool
While it’s great to have all the parts and tools necessary for a specific task within reach on a cart, it’s also important to perform each task properly. FedEx Express mechanics don’t use paper manuals. Everything they need is available on their issued iPads – current and correct. And communicable across facilities, so that one mechanic in, say Los Angeles can help a mechanic in Indy. They can exchange videos, photos, and personal knowledge.
Scot Struminger, vice president, information technology, FedEx Express, notes that with the iPad, “You can look at the MEL; if you haven’t done something before, you can even look at a short video, right there. Not only are we training in the classroom, we have visual aids for just about any task you can think of. And visual aids are much more powerful than the written word. That keeps us more efficient while staying within the guidelines and regulations.
“Written instructions are great, but when you have a visual, you can do it more easily. They still read the manual for detail, but the videos – and Face Time for Mac – help our technicians communicate with engineers and supervisors. So a guy in Indy can contact a specialist in LA, for instance, at all our service stations, where a number of techs are trained to be specialists – Dallas and Atlanta specialize in engine changes; LAX handles that for the MD-10 and -11. We have specialists on fuel quantity in Atlanta – any tech across the system can get immediate specialist support across the system.
“A journey like this is so interesting. iPads and mobile tech weren’t what we were after when we started; but in the middle of it, it became clear that mobile was what we needed to do; so because of the flexible project plan, we kept our eyes on the goal and entertained new ideas on the way. We created a system that can manage the fleet from anywhere in the world.
“It was a joint exercise between the IT folks and A&Ps, so the IT folks could understand and work with A&Ps. We didn’t build things based on IT; our ideas came from the front lines. Greg and I sometimes couldn’t tell who was the IT person and who was the A&P.”
Still, as with any major shift, Greg Hall notes that “It took a bit of getting used to, going with an iPad instead of a computer.”
But Struminger had an idea, and may have coined a new B-school term: Forced adoption. The concept is easy, he says: “Once the new system is in operation, you turn off the old one. You have to, or you’ll end up with parallel systems. We didn’t want to see green-screens. And we don’t.”
Indianapolis is a popular center
FedEx Express looks for employees internally first, based on seniority. “We get probably 20 bidders for each opening,” says Lyons. “Indy is a popular place to work.”
But while that system leads to an experienced workforce, Sanford notes that “the average age of our mechanics is around 50; our youngest is 39.”
But that pipeline needs to be filled. To that end, FedEx Express has two programs. “We have a maintenance training program,” says Sanford, “for A&Ps with under three years’ experience. It’s a three-year program, working with our most-experienced mechanics.” Graduates are instantly assimilated into the their facilities across the country.
Younger, less, experienced but enthusiastic students at Vincennes University are starting with FedEx Express Indy in a new program, where three students, recommended by the school, are in paid internships at the Indy facility. “We see three students for three months, and we have three rotations per year,” explains Sanford. “They rotate through shifts and lines, and gain a lot of experience.” He adds, “It’s a great resume-builder.”
It all comes together: the lean structure, ongoing training, adoption of ideas from the people who live with them. Senior Vice President Hall sums up: “We believe that everything we do should lead to a safer, more pleasant, more efficient environment. The quality of work is better and more efficient than ever before. We pride ourselves on service, but we also price ourselves on safety. I can’t begin to tell you how proud we are of our workforce, our team.”
Tim Kern, CAM, MBA, has written for over 50 aviation publications, and is a consultant for a variety of companies; www.timkern.com.
About the Author
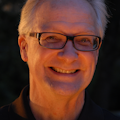
Tim Kern
Tim Kern is an aviation writer, aircraft builder, and private pilot. He is based in Anderson, IN, and can be reached at [email protected].
Tim Kern, CAM, MBA, has written for over 50 aviation publications, and is a consultant for a variety of companies; www.timkern.com.