New Innovations in Composites Will Help Improve Safety
The use of composite materials was pioneered in general aviation, dating back to the very beginning when dope and fabric materials were used for covering wings and airframes. In the last few decades, high-strength composites utilized in the airframe and wing structures as well as for skins have become a popular choice among general aviation aircraft manufacturers. After all, composite materials — such as carbon fiber and fiberglass — can be easily molded into complex shapes for aircraft of all sizes. Modern composites are also lighter and stronger than aluminum, and provide excellent longevity.
Cirrus Aircraft — which produces the majority of composite general aviation aircraft globally and recently delivered its 6,000th all-composite aircraft — pioneered much of the efforts to improve the safety of these machines. For example, Cirrus implemented the airframe parachute, mass shedding to move energy away from the cabin in the event of a crash, and designed the forward area of the fuselage to prevent it from “digging in” during an emergency landing and allowing the energy to dissipate over more distance.
But recently, there’s been a greater effort to understand how composite structures react in emergency landing scenarios. As AMT readers know, while metals tend to deform and absorb energy in a crash, composites tend to flex without as much deformation. This flexing ability is helpful in maintaining the survivable volume of the fuselage, but it can also cause higher loads to transfer onto seats —potentially injuring passengers — or other important parts of the aircraft in ways that metal structures do not.
So Flight Design, which specializes in light sport aircraft, has been working on a design to mitigate this problem. Its C4 airplane features a “SafetyBox” — a fuselage design that includes specifically designed crash absorbers to reduce peak forces on the seats and transfer them to dedicated load paths around the survivable space in the cabin. The interior design decreases the likelihood that passengers will be injured, and the load paths prevent damage from reaching the engine. Flight Design’s holistic approach — considering the response of the complete load path in an accident scenario rather than just the design of the seat structure — is similar to that used by the auto industry, and is expected to significantly improve passengers’ likelihood of survival in the unfortunate event of an emergency landing.
In a great example of international cooperation, Flight Design is partnering with NASA to demonstrate the airplane’s capabilities with a full-scale crash test at the Langley crash test site, likely early next year. Once the test is over, Flight Design plans to share the results with other companies in an effort to help the industry learn from its experience.
The results will not only benefit those who read them, but could find their way into new industry standards for structural design that the ASTM’s General Aviation Aircraft Committee, F44, is creating. This will help all manufacturers as new certification Part/CS 23 requirements take shape.
To be sure, even with these new safety developments, composite aircraft still require unique skill sets for maintenance and repair, with guidance for specific repairs often provided by the airframe manufacturer. As composite materials grow in utility and use, the need for education among the maintenance community will continue to increase as well.
It’s exciting to see a new period of innovation in composites and the important strides our industry continues to make every day to improve safety. I look forward to seeing just how far all-composite aircraft soar in the coming years.
Pete Bunce is President and CEO of the General Aviation Manufacturers Association.
About the Author
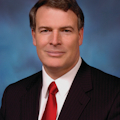
Pete Bunce
Pete Bunce is the president and CEO of GAMA, an international trade association representing more than 100 of the world’s leading manufacturers of general aviation airplanes and rotorcraft, engines, avionics, components and related services. GAMA’s members also operate repair stations, fixed based operations, pilot and maintenance training facilities and they manage fleets of aircraft. You can read more about GAMA’s activities on our Web site at www.gama.aero and on our Facebook page at https://www.facebook.com/#!/General.Aviation.Manufacturers.Association.