Maintenance providers that support customers on the road are particularly vulnerable to an owner’s desire to fix the aircraft “right now.” The ability to provide mobile maintenance services either through a repair station working away from its fixed location or as an independent part 65 mechanic is definitely not limitless. The provisions of parts 43, 65 and 145 all prevent work from being performed improperly. Maintenance providers must always ensure they have the proper housing, facilities, tools, equipment, technical data and knowledge to accomplish the work in such a manner as to return the item to at least its original condition. If a discrepancy cannot be fixed, the aircraft must be ferried.
Whether fixed or ferried, the certificated person (either the repair station or mechanic) must deem the aircraft safe for operation. To deem an aircraft safe to operate, a careful inspection must be accomplished to delineate those items that create unairworthy conditions from those issues that can be resolved at a later date.
The Federal Aviation Administration (FAA) has issued several legal interpretations stating that not every discrepancy renders an aircraft unairworthy — the best summary of the agency’s position can be found in its letter to Christopher Witkowski dated March 26, 2008 found here. Unfortunately, the determination of what does and does not create an unairworthy condition depends upon the knowledge, expertise and mental acuity of a maintenance provider. The individual making determinations of whether an aircraft has to be fixed or can fly as is will have to justify the decision based upon what a “court” would think.
Nevertheless, the language used by judges and lawyers using 20/20 hindsight is important to understand. The National Transportation Safety Board (and subsequently, the FAA’s legal opinion) stated that not “…every scratch, dent, ‘pinhole’ of corrosion, missing screw, or other defect, no matter how minor, or where located on the aircraft…” creates unairworthiness. Rather, the defect must be such that it has an “adverse impact on the level of safety that an aircraft’s conformity with its type [design] is intended to insure.” The maintenance provider’s knowledge must encompass the aircraft’s “original condition” which includes its certification basis. Without understanding the product’s (aircraft, aircraft engine or propeller) certification standard, it is hard to make and hold to determinations of whether a defect has an adverse impact on the ability of the design to uphold its safety requirements.
When working on the road with limited housing, facilities, equipment, tools and other necessities, the maintenance provider must not only understand the basic airworthiness standards but what can and cannot be fixed with the tools and information at hand, deferred or determined to have no impact on the aircraft’s required level of safety. Those facts must be balanced against the pilot (or owner’s) desire to get home or to accomplish the next leg. The individuals tasked with servicing customers on the road must enhance their technical skills right along with their communication capabilities. Whether the decision is to fix, defer, or ferry, it must be clearly documented against the facts and regulations so an owner’s expectations can be tempered with genuine safety considerations. It is a maintenance provider’s responsibility to determine airworthiness; those decisions have to be made in the hangar or shop and on the road.
Sarah MacLeod is executive director of the Aeronautical Repair Station Association (ARSA), an organization she helped found more than 25 years ago. For more information visit www.arsa.org.
About the Author
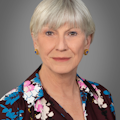