Nondestructive Testing, Then, Now and in the Future
Aviation has changed quite a bit since Orville and Wilber Wright made their first flight at Kitty Hawk, NC, aircraft like life was much simpler. A visual inspection was all that was needed to locate any possible damage. The life extension programs we have today were never dreamed of. Because of this simpler construction, this first generation of aircraft did not require much if any nondestructive testing.
Over the years with changes in aircraft design and specifically the materials used for construction, nondestructive testing has become an integral part of aircraft manufacture and operation. By applying different methods of nondestructive testing during the manufacturing process, defective parts can be identified and removed before they are put into service. Using nondestructive testing while the aircraft is in service ensures continued structural integrity of the airframe, engine, and components.
When the Wright brothers designed and flew the Wright flyer, inspecting the structure probably was never considered. That is until Dec. 14, 1903, when making an attempt to fly the aircraft it stalled. The left wing hit a sandy hillside breaking several parts. The brothers had to bring the aircraft back to the hangar and replace several broken parts. At this time variations of both liquid penetrant and magnetic particle inspection methods were being used in other industries, there simply was no need for the still new aviation market. Even the term “nondestructive testing” (NDT) was not readily used until 1914.
Liquid penetrant
At this time the common methods of NDT were liquid penetrant and magnetic particle. Variations of both of these methods had been used for many years. The penetrant inspection method was first developed by the railroad industry. This inspection technique was referred to as “Oil and Whiting”. Heavy oil was commonly available in the railroad workshops; this oil was diluted with kerosene and applied to the surface of parts. After a period of time the surface was carefully cleaned and coated with a chalk powder in alcohol. Once the alcohol evaporated a coating of chalk was left on the surface of the part. The part was then struck with a hammer causing the residual oil in a surface defect to seep out and leave a stain in the chalk coating. Can you imagine the damage one would cause by hammering on an aluminum part to do penetrant inspections like this? In the 1920s more effective penetrating oils with highly visible dyes were developed by Magnaflux and the Switzer Brothers in Cleveland, OH.
It wasn’t until 1942 that the penetrant method we know today was introduced by Magnaflux, the Zyglo system of penetrant inspection where fluorescent dyes were added to the penetrant. This is when the five different levels of penetrant sensitivity were developed. Today for the inspection of aircraft parts we use levels 2 and 3 sensitivity for general structure and level 4 ultrahigh sensitivity penetrant for critical structure and rotating engine parts. Today all penetrant materials are evaluated to verify they meet current industry requirements. Aerospace Material Specification (AMS) 2644 is now the primary specification used in the United States for evaluating these materials. Once a material has been accepted by this specification it is added to the Qualified Products List (QPL). Only materials on this list may be used for the inspection of aircraft structure and materials.
Magnetic particle
Magnetic particle was being used in machine shops, a fine ferromagnetic powder was applied to magnetized parts, and this powder collected over flaws and formed a visible indication. In the early 1930s magnetic particle started to replace the liquid penetrant method in the rail industry. While steel is not widely used in aviation, there are a number of parts made from high strength steel requiring inspection and magnetic particle is still the preferred method for the inspection of steel.
Eddy current
The eddy current and ultrasound inspection methods came to being when aircraft started to be manufactured from aluminum. Eddy current inspection techniques were first developed during the 1940s and used to inspect metal aircraft during World War II. After the war the advances made in construction of aircraft for military applications were being applied to civilian aircraft. The new metal structures were lighter and stronger than the old materials. With the use of these new materials came new problems like metal fatigue, cracking, and corrosion. Eddy current inspection was advanced in the 1950s and '60s primarily by the aircraft and nuclear industries. The physics of the method had not changed, but the equipment used was being advanced mainly due to the development of computers. New probe designs using ferrite to shape the eddy current field increased inspection sensitivity.
New eddy current probes are available using multiple coils flexible enough to wrap around corners or follow complex shapes. These probes with array coils can scan a large area up to 4 inches with each pass.
Ultrasonics
Ultrasonics is another method of NDT that has evolved greatly over the last few years. This technology was first developed for the medical industry. Equipment manufacturers took the phased array ultrasound technology used to look at the fetus in the mother’s womb and applied it to the pipeline industry inspecting welds. Northwest Airlines became familiar with phased array technology in the 1990s, while it was being used to inspect welds on the Alaskan pipeline. It was the first airline to use phased array ultrasonics on aircraft. The manager of NDT at Northwest working with the aircraft and equipment manufacturers developed an inspection on the main landing gear to look for cracking. Conventional ultrasound could have been used but because the orientation and depth of the flaw was not known many different scans would have to be made to ensure defect detection. Phased array was able to inspect the entire area with only one scan. Phased array technology allows the NDT inspector to choose the angles the sound beam is traveling within the material. It also allows the instrument to “sweep” through selected angles of sound and display all of them on the instrument in what is known as a S scan.
The current material of choice for aircraft construction is carbon graphite reinforced plastic (CGRP), this material has caused the manufacturers of NDT equipment to develop new equipment to overcome the new inspection needs. Using computer-based equipment to developing more complex ultrasound techniques manufacturers are able to overcome these new issues. On a recent trip to General Electric Inspection Technologies (GEIT) in Lewistown, PA, a computer-controlled robotic ultrasonic immersion system was being demonstrated to a group of inspectors with varied NDT backgrounds. This system is able to scan complex composite structure using through transmission ultrasound (TTU). Inspection results are displayed as a “C” scan on the computer display for evaluation. It is not a portable system, but it can be used to develop new inspection techniques or to inspect panels during manufacture. GE will allow companies to bring parts to its facility in Lewistown to help develop new inspection techniques.
Radiography
Other technology developed by the medical industry is radiography. Early radiography used radioactive materials like radium. Because the hazards of radiation were not understood, many of the early scientists overexposed themselves while experimenting with these radioactive materials. Early industrial radiography used a process called “fishpoling”. A radiographer would hold a weak radiation source attached to a pole in position for the duration of the exposure. Using this method today would probably overexpose the radiographer to radiation. While gamma radiation is widely used for industrial radiography, in aviation where the structure is not as heavy, X-rays are preferred. With the development of computer radiography (CR) and digital radiography (DR) the use of chemicals and standard film is reduced or eliminated. New cabinet X-ray machines using micro focus technology can produce radiographs with very high levels of sensitivity. Marrying this technology with computer programs allows the radiographer to inspect for internal defects, do dimensional checks, and even reverse engineer the part. With the development of the CR and DR, lower levels of radiation can be used thereby lowering the risk of overexposure of the radiographer and other personnel in the area.
Thermography
Thermography a relatively new technology as compared to the other methods talked about is something developed for the inspection of composites. This method uses temperature differences to detect flaws within a part. Conventional thermography uses a heat source to warm the part, then the heat source is removed. Over a period of time different materials cool at different rates, if one knows the rate a specific material cools one can see differences in material or specific defects within the material. A process called flash thermography uses a strobe for the heat source, using a high-speed camera and a computer the technician is able to gather data as the heat moves through the material being inspected.
New technology, new training
With the development of new composite materials, manufacturers keep looking for new ways to inspect them for flaws. As these new techniques get more technical the equipment used becomes more sophisticated. Training of the NDT technician is becoming an issue; new instrumentation is becoming very complex. It is no longer a simple procedure to set up the instrument for an inspection. The setup can be quite extensive and take more than an hour to accomplish. To meet this challenge equipment manufacturers have given the instrument the ability to save calibration files. Because these files are so complex the Level 3 can lock out the technician and allow only certain adjustments to be made. The technician can pull up these calibration files, do the inspection, and the Level 3 can be confident the inspection is being done the same by everyone.
These new instruments are capable of using the “Cloud”. Cloud technology allows the inspector to upload inspection information to a secure site. This allows others from various locations to access inspection results and to evaluate results or even help engineer a repair.
Going forward with all the advancements in technology, I see the Level 1 NDT technician being replaced with equipment operators. Other industries have started moving in this direction already. While someone will always have to be on site to move the probe or apply the penetrant, the on-site inspector will not have the ability to evaluate inspection results. As in the other industries the inspection results would be uploaded to a secure site and the Level 2 or 3 wherever they are would do the evaluation.
Greg Linkert has worked in the aerospace industry for 36 years, 26 of those years he has been certified in nondestructive testing as a Level 2 and/or Level 3. He has previously sat on the ASNT Aerospace committee, was a voting member of SAE AMS Committee K, and sits on the Airlines 4 America’s NDT steering committee. In 1996 he was awarded the model of excellence and the Silver Eagle award from McDonnell Douglas for his work on the DC9 Wingbox inspection. Currently he is president/accountable manager of NDI Consultants Inc., an FAA certificated 145 repair station located in Minnesota providing third-party Level 2 and 3 services in nondestructive testing. More information can be found by visiting www.NDI-CO.com.
About the Author
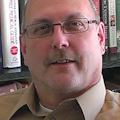
Gregory Linkert
President/Accountable Manager
Greg Linkert has worked in the aerospace industry for 36 years, 26 of those years he has been certified in nondestructive testing as a Level 2 and/or Level 3. He has previously sat on the ASNT Aerospace committee, was a voting member of SAE AMS Committee K, and sits on the Airlines 4 America’s NDT steering committee. In 1996 he was awarded the model of excellence and the Silver Eagle award from McDonnell Douglas for his work on the DC9 Wingbox inspection. Currently he is president/accountable manager of NDI Consultants Inc., an FAA certificated 145 repair station located in Minnesota providing third-party Level 2 and 3 services in nondestructive testing. More information can be found by visiting facebook or on the web at www.NDI-CO.com.