Almost every week a mechanic or a mechanic's group will raise an ethical issue in our conversations. The black and white issues are just that, black and white. Signing off for an annual or 100-hour inspection when you haven’t done one is obviously not OK from an ethical standpoint, not to mention a clear violation of the Federal Aviation Regulations that can have significant consequences for your livelihood. The same is true for signing off for a repair that you have not done.
Rushed jobs
But what about the gray areas? The two most frequently discussed issues in my experience, are the rushed jobs and what to do when the maintenance manual or task cards are wrong. In the first instance, the question revolves around signing off work that you’re asked to do in a shorter amount of time than you normally require or would like. Is a rushed annual still an annual that you can ethically and legally sign off for? Of course, the answer depends on how rushed. Do a job too quickly and you risk missing some potentially significant airworthiness problems. Do a job too slowly and you risk missing out on additional income or angering your boss. But the point of this article is not to answer the question of how fast is too fast, but to get you to start planning ahead for those rush jobs so that you can spend your time more effectively and consequently feel comfortable that the time saved has not negatively affected the quality of the work you have been assigned.
As soon as work is assigned or contracted for, make sure the most up-to-date paperwork, manuals, airworthiness directives, etc., are reviewed and understood. Don’t wait until the aircraft actually shows up at the shop to do this. It will eat up unnecessary time that could be spent doing the tasks necessary. Many times, I see mechanics at large and small shops waiting until an aircraft arrives to get the paperwork ready. Usually, this work can be done before the aircraft even arrives in the shop. This is also a good time to ensure that you have all the tools ready and properly calibrated, as necessary. If a special tool is required, securing access to it ahead of the aircraft’s arrival will make the job go faster and more smoothly.
What if the paperwork is wrong?
The other issue that comes up frequently is what to do when the paperwork is wrong – or at least you believe it to be wrong. Clearly you can’t ethically do a maintenance job that you believe is incorrect just because the paperwork says to do it that way. On the other hand, you don’t have the authority to deviate from the paperwork. And, of course, just because you think the paperwork is wrong doesn’t mean that it is wrong. The problem I usually find is that the shop where the mechanic works – be it a repair station, an air carrier, or a one-person operation – hasn’t planned ahead for this pretty common problem. The time to figure out the process for dealing with incorrect paperwork is not in the middle of a repair where time pressures are significant. The time to put the process in place is now. Every shop needs to have a process in place for getting paperwork issues resolved so that a mechanic is not left to make decisions on his or her own. Then it’s up to every mechanic who identifies a problem with the paperwork to follow the process to get it corrected, whether that requires an engineering order or other approval. So if you’re in a shop that doesn’t have a process in place, ask management to establish one. It’s in their best interests, too.
About the Author
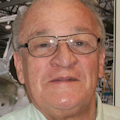
John Goglia
John Goglia has 40+ years experience in the aviation industry. He was the first NTSB member to hold an FAA aircraft mechanic's certificate. He can be reached at [email protected].
John Goglia is an independent aviation safety consultant and Adjunct Professor at Vaughn College of Aeronautics and Technology and regular monthly columnist for four aviation trade publications. He was an airline mechanic for more than 30 years. He has co-authored two text books (Safety Management Systems in Aviation, Ashgate Publishing 2009 and Implementation of Safety Management Systems in Aviation, Ashgate Publishing 2011).