If you have heard a lot of buzz about OSHA recently, it is for good reason. What is happening with OSHA? OSHA has recently revised its current hazard Communication Standard, 29 CFR 1910.1200 so it will align with what is known as the GHS, Globally Harmonized System of Classification and Labeling of Chemicals.
The original Hazard Communication Standard of 1983 gave workers the right to know. The revised standard gives workers the right to understand. OSHA cites that the revisions will enhance worker comprehension, especially for low and limited literacy workers and reduce confusion in the workplace. The new standard should provide workers quicker and more efficient access to information on Safety Data Sheets resulting in safer handling of potentially dangerous chemicals.
Addressing common questions
Why is OSHA changing its requirement?
OSHA is simply getting on the same page as the rest of the world. In 1992 the United Nations Conference on Environment and Development came to an agreement that a globally harmonized system of recognition and placarding be developed and managed by an international group of countries to promote enhanced understanding of hazardous material exposure and handling. The UN adopted the Global Harmonization System (GHS), modeled after the US, Canadian, and European systems in 2003 with a goal of each country adopting and implementing by 2008. Not only does the new system protect humans and the environment, it also will serve to heighten global trade by reducing barriers to communication that formerly existed. GHS will create a system in countries where systems did not exist.
What part of the standard is affected by GHS?
The classification criteria for health and environmental standards as well as physical standards are now in sync with GHS. Communication requirements for labeling, Safety Data Sheets, and training fall within the scope of the new requirements. With the exception of aquatic toxicity the DOT is already harmonized with the international transport system.
Who is affected and what is the dateline?
The second Advance Notice of Public Rulemaking was published in 2009, followed by a final ruling. Employers are now required to train employees by Dec. 1, 2013.
Who needs this revised GHS training?
Employees in virtually all industries and occupations, especially pilots, mechanics and line service personnel in general aviation, who are continually exposed to jet fuel, oils, lubes, will benefit from training. OSHA-compliant Hazmat GHS training is essential for any worker who has any exposure to hazardous chemicals. OSHA has mandated that all affected workers must be trained to read and understand the new safety data sheets and chemical labeling criteria.
What specifically should training address?
Compliant training courses should familiarize workers with knowledge of the new safety data sheet (SDS) format and the new chemical labeling criteria of the Globally Harmonized System of Classification and Labeling of Chemicals (GHS), as well as highlight OSHA-mandated guidelines, OSHA 1910.1200 regulations.
How often does an employer have to train its employees?
A new hazmat employee who changes job functions may perform those functions prior to completion of this training provided the employee performs those functions under direct supervision of a properly trained and knowledgeable hazmat employee; and the training is completed within 90 days after employment or job function change.
Employees must receive the required training every three years, or any time there is a change in job function. A change in the Hazardous Materials Regulations constitutes a change in job function.
Who is considered a hazmat employer?
A hazmat employer means a person who employs or uses at least one hazmat employee on a full-time, part-time, or temporary basis; or is self-employed (including an owner-operator of a motor vehicle, vessel, or aircraft) transporting hazardous material in commerce; and who:
• Transports hazardous material in commerce;
• Causes hazardous material to be transported in commerce; or
• Designs, manufactures, fabricates, inspects, marks, maintains, reconditions, repairs, or tests a package, container, or packaging component that is represented, marked, certified, or sold as qualified for use in transporting hazardous material in commerce.
Who is considered a hazmat employee?
A hazmat employee is an individual, employed by a hazmat employer who, in the course of employment:
• Loads, unloads, or handles hazardous materials
• Prepares hazardous materials for transportation
• Is responsible for safety of transporting hazardous materials
• Operates a vehicle used to transport hazardous materials
Hazmat employees are to be trained at the time they are assigned to work with a hazardous material/chemical. The intent is to have information in the employee’s hands prior to exposure to prevent the occurrence of adverse health effects.
Satisfying the training provisions
Simply giving an employee the MSDS to read does not satisfy the training provisions of the GHS. An employer's training program is to be a forum for explaining to employees, not only the hazards of the chemicals in their work area, but also how to use the information generated in the company’s hazard communication program. This can be accomplished in many ways (audiovisuals, classroom instruction, interactive video, online training).
Training need not be conducted on each specific chemical found in the workplace, but may be conducted by hazard category that are, or may be, encountered by an employee during the course of his duties.
GHS vs. HCS
There are several changes with the new GHS system versus the HCS system, which is being phased out. One major change is that the previous Material Safety Data Sheet (MSDS) has 12 sections, where it did not matter in which order they were placed on the sheet. The newly created Safety Data Sheet (SDS) has 16 sections. Each of these sections on the new SDS must be listed in the same order and they will have subsections where the additional, more in-depth information, will apply.
Another major change is with the packaging labels. The hazard symbols, signal words and hazard statements on the labels have all been standardized and assigned to each of the hazard categories. These standardized elements should not be subject to variation, and should appear on the GHS label. At this time the actual label format or layout is not specified in the GHS however, National authorities may choose to specify where the information should appear on the label or allow supplier discretion. The GHS label requirements are a significant change from performance-oriented HCS labels.
OSHA recognizes that hazard communication programs would go through a period of time where labels and Safety Data Sheets under both standards will be present in the workplace. It is considered acceptable that employers would not be required to maintain two sets of labels or SDS for compliance purposes. However, hazard communication must continually be in effect and information must always be available in the workplace under either the existing HCS standard, or the new GHS standard for all exposed employees.
Additionally OSHA requires that employers provide training regarding the new GHS labels and Safety Data Sheets by Dec. 1, 2013. The intent of this training is to ensure that when employees begin to see such labels and SDS in their workplaces, they understand how to use them and access the information effectively.
Online courses, such as Hazardous Materials Awareness offered by Aviation Training Academy provide both an affordable and convenient platform to meet the new requirements.
DeborahAnn Cavalcante earned her Masters in Aeronautical Science, with a specialization in Safety Management from Embry Riddle Aeronautical University in Daytona, FL, and her Bachelor of Science from VA Tech in Business and Risk Management.
DeborahAnn Cavalcante leads Diversified Aviation Consulting (DAC) and along with her associates has firsthand experience in air carrier operations, private charter aircraft, general aviation operations, military/civilian interface, FBO management, maintenance repair station training, safety training, human factors training, and customer service training. For more information on DAC visit http://www.dac.aero.
About the Author
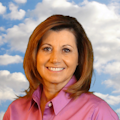
DeborahAnn Cavalcante
DeborahAnn Cavalcante earned her Masters in Aeronautical Science, with a specialization in Safety Management from Embry Riddle Aeronautical University in Daytona, FL, and her Bachelor of Science from VA Tech in Business and Risk Management.
DeborahAnn Cavalcante leads Diversified Aviation Consulting (DAC) and along with her associates has firsthand experience in air carrier operations, private charter aircraft, general aviation operations, military/civilian interface, FBO management, maintenance repair station training, safety training, human factors training, and customer service training. For more information on DAC visit http://www.dac.aero.